Effizienz in der Ersatzteillogistik
Nov 5, 2008 • 8 min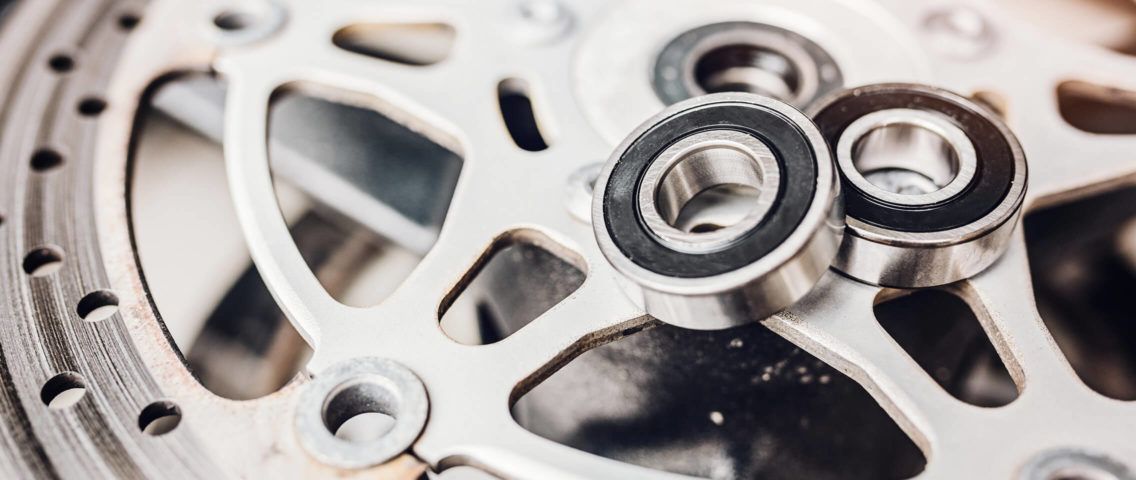
In der Ersatzteillogistik gibt es zahlreiche Herausforderungen. Das Handlungsumfeld ist ausgesprochen komplex, da Ersatzteile auf verschiedenen Ebenen und in verschiedenen Niederlassungen eingelagert werden (Hersteller, Großhandel, Händler und Endverbraucher). Außerdem ist die Vielfalt der abzuwickelnden Artikel ausgesprochen hoch. Es werden tausende oder mehrere tausend Artikel verwaltet, die unterschiedliche Merkmale aufweisen (Wert, Produktlebenszyklus, Gewicht, Größe, Prozessbedeutung, Prognostizierbarkeit des Absatzverhaltens etc.). Typische Merkmale des Ersatzteilhandels sind auch eine zerstreute Nachfrage und eine schwierige Vorhersagbarkeit. Wenn man dazu noch die hohen Anforderungen an das Serviceniveau und an die Kosteneffizienz der Logistik zählt, kann man sich vorstellen, mit welchen Problemen die Ersatzteillogistik zu kämpfen hat. In vielen Fällen konnte die Effizienz des Ersatzteilmanagements jedoch deutlich gesteigert werden. Mit Hilfe von Entwicklungsmaßnahmen konnten sowohl Serviceniveau als auch Kosteneffizienz erheblich verbessert werden. Es darf jedoch nicht vergessen werden, dass herkömmliche für Lieferketten entwickelte Steuermodelle und Methoden nicht in jeder Hinsicht für das Ersatzteilmanagement geeignet sind. Bei der Entwicklung der Ersatzteillogistik müssen die besonderen Merkmale der Branche berücksichtigt werden.
Besondere Merkmale des Ersatzteilhandels
Ersatzteil- und Fertigproduktlieferketten unterscheiden sich in ihrem Handlungsumfeld und den Eigenschaften der Produkte. Cohen et al. (2006) haben die Unterschiede von Herstellungs- und After-Sales-Markt-Lieferketten zusammengefasst (Tabelle 1).
Herstellungslieferkette | After-Sales-Markt-Lieferkette | |
Wesen der Nachfrage | Nachfrage vorhersagbar | Nachfrage nicht vorhersagbar, oft zerstreut |
Lieferzeit | Lieferzeit standardisierbar | Sehr hohe Lieferzeitanforderungen |
Artikelmenge | Begrenzt | 15–20 Mal größer |
Produktportfolio | Oft sehr homogen | Stets heterogen |
Ziel des Lagermanagements | Maximierung der Umschlaggeschwindigkeit | Richtige Positionierung der Lagerartikel |
Leistungsfähigkeitsmaße | Lagerfüllrate | Produktverfügbarkeit |
Lagerumschlag | 6 -50 | 1 – 4 |
Tabelle 1. Besondere Merkmale des Ersatzteilhandels (Vgl. Cohen et al., 2006).
Im Prinzip bedeuten die Unterschiede zwischen den Lieferketten zweierlei:
- In der Ersatzteillogistik sollten nicht die gleichen Ziele angestrebt werden wie in der Herstellungslieferkette.
- Die Steuermodelle von Herstellungslieferketten können in der Ersatzteillieferkette zu schlechten Ergebnissen führen.
In Herstellungslieferketten wird ein gutes Serviceniveau und Produktverfügbarkeit mit einem möglichst effizienten Lagerumschlag angestrebt. Ersatzteile dienen jedoch als Reserve, müssen daher also auf Vorrat gelagert werden. Hauptziel der Ersatzteillogistik kann also nicht eine Maximierung des Lagerumschlags sein. Der durchschnittliche Umschlagswert in Lieferketten von Unternehmen, die für ihre gute Ersatzteillogistik bekannt sind, beträgt nur 0,87 (Cohen et al., 1997).
Entwicklung der Ersatzteillogistik
Bei der Entwicklung der Ersatzteillogistik müssen die besonderen Merkmale der Produkte und deren Nachfrage berücksichtigt werden. Diese wirken sich erheblich auf die Funktion der gewählten Steuermodelle aus, besonders wenn es um Nachfrageprognosen, Einteilung der Produkte in verschiedene Steuerungskategorien, Festlegung von Sicherheitsbeständen oder Wahl der effizientesten Liefermodelle geht. Eine positive Entwicklung setzt die systematische artikelspezifische Nutzung von Artikel- und Nachfragedaten voraus.
Nachfrageprognosen
Ein Problem bei der Erstellung von Prognosen für den Ersatzteilhandel ist die verteilte Nachfrage. Einzelne Nachfragespitzen wechseln sich mit ruhigeren Perioden ab.
Herkömmlich genutzte Modelle (z. B. gleitender Durchschnitt oder Exponentielle Glättung), die auf unterschiedlich ermittelten Durchschnittswerten basieren, bringen daher keine guten Ergebnisse hervor.
Für verteilte Nachfrage existieren jedoch eigene Prognosemodelle. Im Croston-Modell (Croston, 1972) wird zum Beispiel angestrebt, den Umfang der Nachfragespitzen und die Länge der Perioden dazwischen vorherzusagen.
Durch Erfassen von Daten zu Schadensfrequenz von Anlagen und Produktlebenszyklus von Ersatzteilen kann die Nachfrage auch in gewissem Umfang vorausgesagt werden (Ghodrati und Kumar, 2005). Diese Herangehensweisen eignen sich jedoch am besten für die Verwaltung von einzelnen, ausgesprochen teuren Komponenten auf Einsatzbereichebene, wobei diese detaillierten Analysen mit dem ausgesprochen hohen Wert und dem prozesskritischen Charakter der Komponenten zu begründen sind. Oder für die statistische Erfassung der Gesamtnachfrage eines Ersatzteils, wobei z. B. Informationen über die Absatzentwicklung die Herstellungsplanung stützen. Selbst im besten Fall kann die Nachfrage für Ersatzteile jedoch nur schlecht vorhergesagt werden, weshalb am wichtigsten ist zu wissen, welches Prognoseniveau erreicht werden kann und auf welche unsichere Situation mit Sicherheitsbeständen reagiert werden muss.
Klassifikation der Produkte
Aufgrund der großen Artikelmengen und zahlreichen Lager ist die zu verwaltende Gesamheit umfangreich und komplex. Eine regelmäßige manuelle Bearbeitung sämtlicher Artikel-Lager-Kombinationen würde einen hohen Aufwand an Ressourcen voraussetzen.
Gewöhnlich wird zur Unterstützung der Steuerung die ABC-Analyse der Produkte eingesetzt. Die ABC-Analyse basiert auf der Klassifikation der Produkte je nach deren Volumen in Euro, wobei die Steuerungsressourcen auf die hinsichtlich Umsatz und Handelsspanne wichtigsten Produkte konzentriert werden. Die Anwendung der ABC-Analyse für Ersatzteile birgt jedoch Probleme. Aufgrund der ständigen Wechsel von Preisen und Eigenschaften der zu verwaltenden Ersatzteile kann die ABC-Analyse irreführend sein. In der Praxis können ein Kurzblockmotor, von dem zwei Stück pro Jahr verkauft werden, und eine Flügelschraube mit einem Absatzvolumen von tausend Stück leicht in dieselbe ABC-Klasse eingestuft werden, obwohl es nicht sinnvoll ist, beide mit derselben Logik und entsprechend gleicher Lagerziele zu steuern. Problematisch sind auch Lagerentscheidungen auf Grundlage der ABC-Klassifikation. In die oberen Klassen werden die teuren Artikel eingestuft, die jedoch ein geringes und schwankendes Absatzvolumen aufweisen. Diese teuren Artikel weisen ein hohes Veraltungsrisiko auf und sollten daher nicht auf Vorrat gelagert werden, wenn sie möglicherweise mit Hilfe anderer Modelle verteilt werden können. Die anhand von empirischen Erfahrungen und Bedarfshäufigkeit erfolgende XYZ-Analyse und Steuerung sind aus der Sicht des Endkunden oft zweckgerechter. Ziel sollte die maximale Erfüllung jeder Bedarfssituation des Kunden sein und kein mittelmäßiges Serviceniveau.
Wie in vielen anderen Produktbereichen können bei Ersatzteilen qualitativ bessere klassenbezogene Entscheidungen getroffen werden, indem ABC- und XYZ-Klassifikationen für die Steuerung kombiniert werden. Die gleichzeitige Nutzung von ABC- und XYZ-Analyse wird an einem Beispiel in Tabelle 2 vorgestellt.
A | B | C | |
X | Streben nach möglichst präziser Steuerung (Kosteneinschätzungen und Prognosen) | Lagerung allgemeinStreben nach präziser Steuerung (Kosteneinschätzungen und Prognosen) | Lagerung, außer AusnahmefälleGroße Lieferpartien |
Y | Streben nach präziser Steuerung (Lagerentscheidung, Kosteneinschätzungen und Prognosen) | Lagerung von kritischen Produkten, ansonsten kostenabhängig | Lagerung, außer AusnahmefälleGroße Lieferpartien |
Z | Hauptsächlich als BestellprodukteLagerung nur für kritische Produkte | Lagerung von kritischen Produkten, ansonsten kostenabhängig | Lagerung von kritischen Produkten, ansonsten kostenabhängig |
Tabelle 2. Nutzung von ABC- und XYZ-Analysen für die Steuerung von Ersatzteilen
Wenn Ersatzteile große Unterschiede in Preisen und Vorgangsmengen aufweisen, muss auch ein höheres Augenmerk auf der Festlegung der Klassengrenzen liegen. Es muss zum Beispiel sichergestellt sein, dass für Artikel der X-Klasse auch die richtige Anzahl an Lieferzeilen festgelegt ist. Klassengrenzen, die sich für normale Artikel eignen, führen bei Ersatzteilen selten zu einem guten Ergebnis.
Festlegung von Sicherheitsbeständen
Eine effiziente Klassifikation von Artikeln stützt die Festlegung von Bestandszielen. Auf dieser Grundlage können jedoch keine optimalen artikelspezifischen Sicherheitsbestände erstellt werden, auf die sich u. a. die Vorhersagbarkeit der Nachfrage, die Lieferzeit und die Unsicherheit bezüglich der Lieferzeit sowie das Veraltungsrisiko auswirken. Aufgrund der großen Menge der Ersatzteilartikel wird für die Festlegung von Sicherheitsbeständen ein gewisses Maß an Automatisierung benötigt. Die Steuerparameter können nicht für alle Artikel effizient manuell verwaltet werden. Das Problem ist, dass für Ersatzteile gewöhnlich keine zuverlässigen Steuerparameter auf Basis von durchschnittlichem Verbrauch, Prognosefehlern oder Nachfragestreuung ermittelt werden können. Die Ersatzteilnachfrage sollte nicht entsprechend des durchschnittlichen Verbrauchs evaluiert werden. Da in der Nachfrage Spitzenzeiten und ruhige Zeiten abwechseln, ist der durchschnittliche Verbrauch kein guter Indikator für den Bevorratungsbedarf. Im Prinzip kann eine Absatzspitze über einen ziemlich langen Zeitraum den Durchschnittsverbrauch übersteigen. Die Frequenz der Spitzenzeiten variiert auch je nach Artikel. Bei einem Artikel kann sich als Sicherheitsbestand der Durchschnittsverbrauch von zwei Monaten anbieten, bei einem anderen von zwei Jahren.
Die herkömmlich zur Festlegung von Sicherheitsbeständen verwendeten Kalkulationsmodelle (z. B. Vollman et.al., 1997) eignen sich auch nicht besonders gut für die Bestimmung von Ersatzteil-Sicherheitsbeständen, denn sie gehen von der Normalverteilung der Nachfrage aus. Die Ersatzteilnachfrage weist gewöhnlich keine Normalverteilung auf, sondern ist zerstreut und hat Spitzen. Einzelne Artikel, besonders solche, die von ihrem Wesen her eher Grundartikel als Ersatzteile sind (wie Glühlampen) können eine gute Nachfrage mit fast normaler Verteilung aufweisen, aber die Steuerung solcher Artikel ist sowieso nicht problematisch.
RELEX legt Alarmgrenzwerte und Sicherheitsbestände mit Hilfe von Simulation fest. Für die Lagerauffüllung wird im System ein Modell erstellt, in dem u. a. Lieferverzögerungen und Liefergrößeneinschränkungen berücksichtigt werden. Es werden reelle Nachfragedaten, einschließlich natürlicher Nachfragespitzen, eingegeben, mittels derer das System automatisch die Steuerparameter erstellt, die hinsichtlich der Erfüllung der Serviceziele am effizientesten sind. So können das Wesen des Lieferprozesses, Nachfrageschwankungen und Vorhersagbarkeit sowie tatsächliche Schwankungen der Lieferzeit bei der Optimierung der Steuerparameter berücksichtigt werden. So konnte zum Beispiel beim Agrarhandel Maatalouskesko mit einer präziseren Steuerung das Serviceniveau merklich gehoben werden, ohne dass im Lager zusätzliches Kapital gebunden werden musste. In Folge einer effizienten Nutzung des Systems konnte die Lieferkettensteuerung zusätzlich mit weniger Personalressourcen durchgeführt werden, was Einsparungen von mehreren VZÄ zur Folge hatte. (TIEKE, 2007)
Festlegung von Lagerpunkten
Aufgrund von Lieferzeitbeschränkungen und dem prozesskritischen Wesen bestimmter Artikel müssen solche in Kundennähe gelagert werden. Für einen Großteil der Artikel können jedoch die jeweils kosteneffizientesten Liefermodelle gewählt werden.
Die günstige Lieferalternative hängt vom Absatzverhalten, Produktwert und den Lager- und Lieferkosten ab. Als Faustregel gilt, dass billige Produkte mit hoher Nachfrage eingelagert werden und teure Produkte mit geringer Nachfrage nur bei Bedarf bestellt werden. Die produkt- und lieferantenabhängigen Kosten weisen jedoch oft erhebliche Unterschiede auf, was sich so auf die Wahl der jeweils effizientesten Lieferalternative auswirkt.
Mit Liefermodellwahl können die Logistikkosten erheblich beeinflusst werden. Bei der Wahl müssen das je nach Einsatzzweck angestrebte Serviceniveau sowie die Kostenstruktur verschiedener Liefermodelle berücksichtigt werden. Die Prüfung der Modelle ist im Prinzip einfach, schwierig ist die Anwendung auf zehntausende Produkte und zahlreiche Niederlassungen. Das größte Problem ist die Erstellung und Verwaltung der nötigen Kostendaten. Bei Ersatzteilen stellt das Veraltungsrisiko oft einen bedeutenden Kostenfaktor dar, aber die wenigsten Unternehmen verfügen über genaue Angaben zur Lebenszykluserwartung verschiedener Produkte. Weiterhin weist das Monitoring von liefer- und zeilenspezifischen Frachtkosten für gewöhnlich Entwicklungsbedarf auf. Je detailliertere Kostendaten vorliegen, desto bessere Entscheidungen können getroffen und desto höhere Einsparungen erzielt werden. Für gewöhnlich können auch schon mit groben Angaben bessere Ergebnisse erreicht werden als in der Ausgangssituation.
Der Arbeitsaufwand für die Ermittlung und Verwaltung der Kostendaten zahlt sich für gewöhnlich hoch aus. Wir können unseren Kunden spürbare Vorteile mit Hilfe von kostenbezogenen Liefermodellen bieten. Beim Wartungsunternehmen Raskone wurde zum Beispiel eine Prüfung in der gesamten Verteilerkette durchgeführt, bei der festgelegt wurde, welche Produkte auf Vorrat gelagert werden sollten und welche vom Distributionsterminal geliefert werden. In der Praxis werden hohe Kosten für Express- und andere Lieferungen eingespart, wenn das Lager mit den richtigen Produkten bevorratet ist. (GS1 Info, 2007; TIEKE, 2007.)
Zusammenfassung
Umfang und Vielfalt der Artikel stellen hohe Herausforderungen an die Ersatzteillogistik dar. Aufgrund der Heterogenität der Artikel setzt eine effiziente Verwaltung die individuelle Prüfung von Artikeln und Filialen voraus; mit grober Verwaltung, z. B. auf Basis der ABC-Analyse, werden selten gute Ergebnisse erreicht. Die Steuerung auf Artikelebene ist möglich, setzt aber qualitativ hochwertige und präzise Nachfrage- und Kostendaten und eine systembasierte und produktspezifische Steuerung und Analyse voraus.
Quellen:
Cohen, M.A., Zheng, Y.-S., Agraval, V. (1997), ”Service parts logistics: a benchmark analysis”, IIE Transactions, Vol. 29, pp. 627-639.
Cohen, M.A., Agrawal, N., Agrawal V. (2006), “Winning in the Aftermarket”, Harvard Business Review, May 2006.
Croston J.D. (1972), Operational Research Quarterly, Vol. 23, No. 3, pp. 289-303.
Ghodrati, B., Kumar, U., (2005), ”Operating environment-based spare parts forecasting and logistics: a case study”, International Journal of Logistics: Research and Application, Vol. 8, No. 2, pp. 95-105.
GS1 Info (2007), ”Automaattinen myymälätäydennys”, 2/2007, sivut 6-8.
TIEKE (2007), “Kysynnän ennustaminen tuo kaupalle huomattavia säästöjä”, http://www.tieke.fi/?E=11687&SINGLE_EMBED=11687&num=6818.
Vollman, T.E., Berry, W.L., Whybark, D.C. (1997), “Manufacturing planning and control”, 4. painos, pp. 708-709.