Wie eine Software-Plattform Lebensmittelherstellern bei der Planung hilft
Sep 16, 2024 • 8 min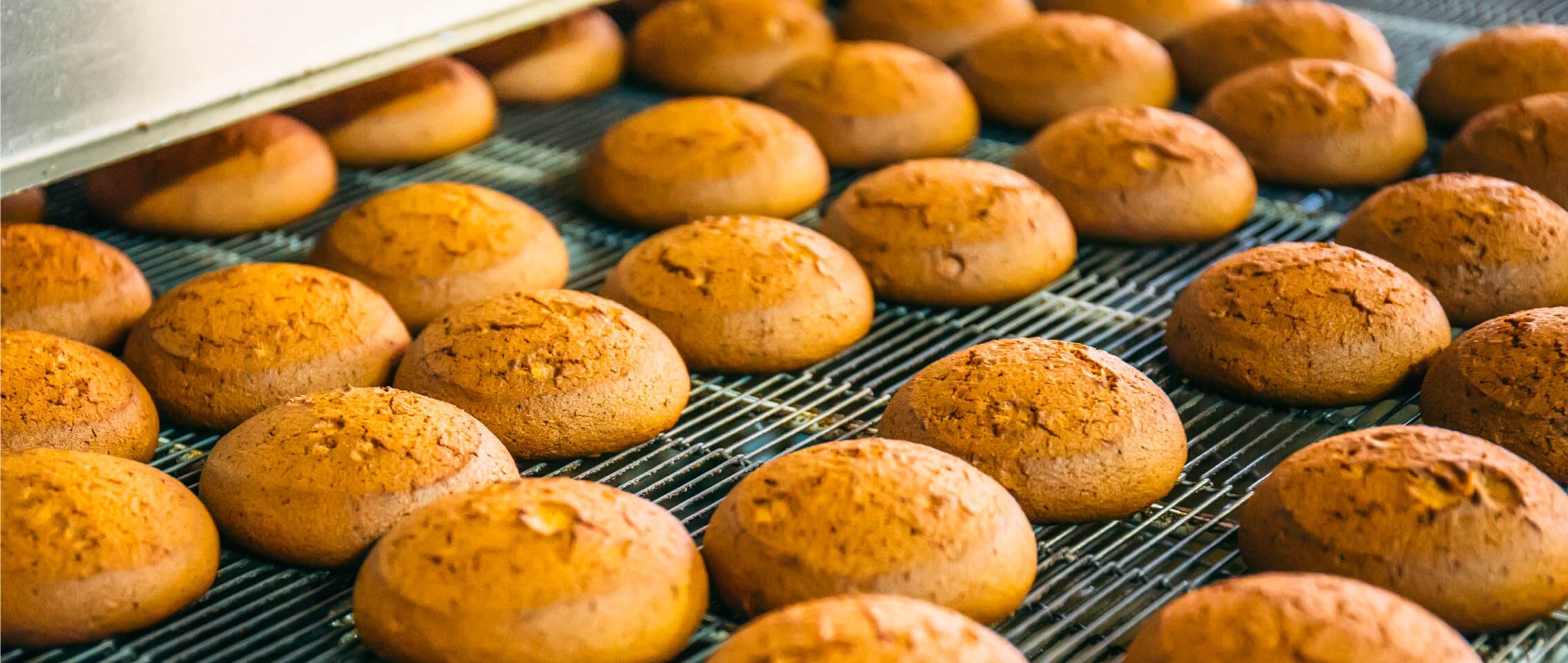
Nachfragebedarf einerseits – Angebotsrealität andererseits. Produktionsbeschränkungen versus Kundenverpflichtungen. Langfristige Planungsziele gegenüber der Aufrechterhaltung kurzfristiger Flexibilität.
Für lebensmittelverarbeitende Betriebe ist effektive Planung ein ständiger Drahtseilakt: Sie müssen Produktionspläne, betriebswirtschaftliche Zwänge und Materialknappheit gegen eine schwankende Nachfrage und die drohende Gefahr des Verderbs abwägen. Ändert sich nur eine einzige Variable, kann das die Serviceanforderungen in die Höhe treiben und die Rentabilität ins Tal der Tränen stürzen – katastrophal in einer Branche, die mit hauchdünnen Gewinnspannen arbeitet.
Egal, wie erfahren das Team von Planungsexperten eines Lebensmittelherstellers ist: Manuelle Prozesse, unzusammenhängende Planung und mangelnde Transparenz entlang der Lieferkette erschweren sämtliche Bemühungen, Produktionsverpflichtungen funktionsübergreifend auszugleichen. Ohne einen einheitlichen Plan, auf den sich alle Beteiligten verständigen, arbeiten die Planer in den verschiedenen Teams möglicherweise gegeneinander – anstatt zusammen die Kundenanforderungen zu erfüllen und den Unternehmensgewinn zu maximieren.
Die Planung in der Lebensmittelverarbeitung muss sich jedoch nicht so schwierig gestalten wie eine artistische Nummer am Trapez. Das richtige digitale Tool verleiht einem Unternehmen Planungstransparenz und Möglichkeiten zur Zusammenarbeit, mit denen es die Herausforderungen in der Lebensmittelherstellung meistert und Kundenaufträge auf die profitabelste Weise ausführt.
Push- und Pull-Modelle ausbalancieren
Lebensmittelhersteller müssen einerseits ein konstantes Angebot aufrechterhalten und andererseits die sich ständig ändernde Kundennachfrage befriedigen. Keine leichte Aufgabe.
Nehmen wir beispielsweise einen Molkereibetrieb. Die wöchentliche Milchproduktion lässt sich nicht genau vorhersehen. Fällt die Produktion in einer bestimmten Woche geringer aus als erwartet, muss das Unternehmen entscheiden, welche Produkte es herstellen und welche ausstehenden Kundenaufträge es erfüllen soll. Es gibt auch das gegenteilige Problem: Oft sind Hersteller verpflichtet, die gesamte Milchmenge eines Erzeugers abzunehmen – unabhängig von der Nachfrage. Folglich müssen sie dann die gesamte Menge unabhängig von der Nachfrage verwerten oder riskieren einen kostspieligen Verderb.
Push-, Pull- und Hybrid-Produktion
An diesem Beispiel zeigt sich das Spannungsfeld zwischen Push- und Pull-gesteuerten Produktionsmodellen, wie sie in der Lebensmittelverarbeitung üblich sind. Beim Push-Modell (auch „Make-to-Stock“-Modell oder Fertigung auf Lager genannt) produzieren Unternehmen Waren auf Grundlage von Absatzprognosen. Die Betriebe produzieren die Artikel also im Voraus, so dass sie Kundenaufträge sofort erfüllen können. Dieses Modell eignet sich gut für Tiefkühlprodukte oder länger haltbare Produkte wie Getränke. Für frische Lebensmittel verarbeitende Hersteller kann die Notwendigkeit, Produkte auf Lager zu halten, jedoch das Risiko des Verderbs erhöhen.
Für frische Lebensmittel verarbeitende Hersteller kann die Notwendigkeit, Produkte auf Lager zu halten, das Risiko des Verderbs erhöhen.
Ein Pull-Modell (auch „Make-to-Order“-Modell bzw. Auftragsfertigung genannt) arbeitet vom anderen Ende des Spektrums aus. Hier fertigt und bestellt der Hersteller Rohstoffe auf der Grundlage von Prognosen, da die Kundenanfragen in der Regel nur wenige Tage vor der Erfüllungsfrist eintreffen. Die Produkte werden also meist buchstäblich auf Zuruf beziehungsweise nach Auftrag hergestellt. Prognosen ermöglichen es den Herstellern, nur so viele Rohstoffe wie nötig zu kaufen und so die Lagerkosten zu senken. Dieses Modell versagt jedoch, wenn die Nachfrage plötzlich in die Höhe schießt. In der Folge kann es passieren, dass Aufträge nicht erfüllt werden oder die Kundenbeziehungen leiden.
Frische Lebensmittel lassen sich naturgemäß nicht lange lagern. Unternehmen brauchen jedoch auch Grundnahrungsmittel, die bei Nachfrageverlagerungen sofort verfügbar sind. Um diesen Problemen zuvorzukommen, setzen die meisten Hersteller auf hybride Push-Pull-Modelle. Leider steht ihnen dabei selten ein System zur Verfügung, mit dem sie erkennen können, welche Mischung aus Push- und Pull-Methoden sowohl die betriebliche Effizienz als auch die Rentabilität maximiert.
Profit-optimierte Push-Pull-Modelle
Eine robuste Planungsplattform kann Absatzprognosen und Kundenaufträge abgleichen – die modernsten Plattformen gehen jedoch noch weiter. Anstatt die Ergebnisse in Form von „Push“- und „Pull“-basierten Methoden zu betrachten, simulieren fortschrittliche Plattformen jeden möglichen Plan, um den profitabelsten oder kosteneffizientesten zu ermitteln. Die Hersteller erreichen ihre Ziele somit nach wie vor durch ein hybrides Push-Pull-Produktionsmodell. Der Unterschied ist, dass die vorliegenden Daten den optimalen Weg weisen, und nicht das Bauchgefühl oder frühere Vorgehensweisen.
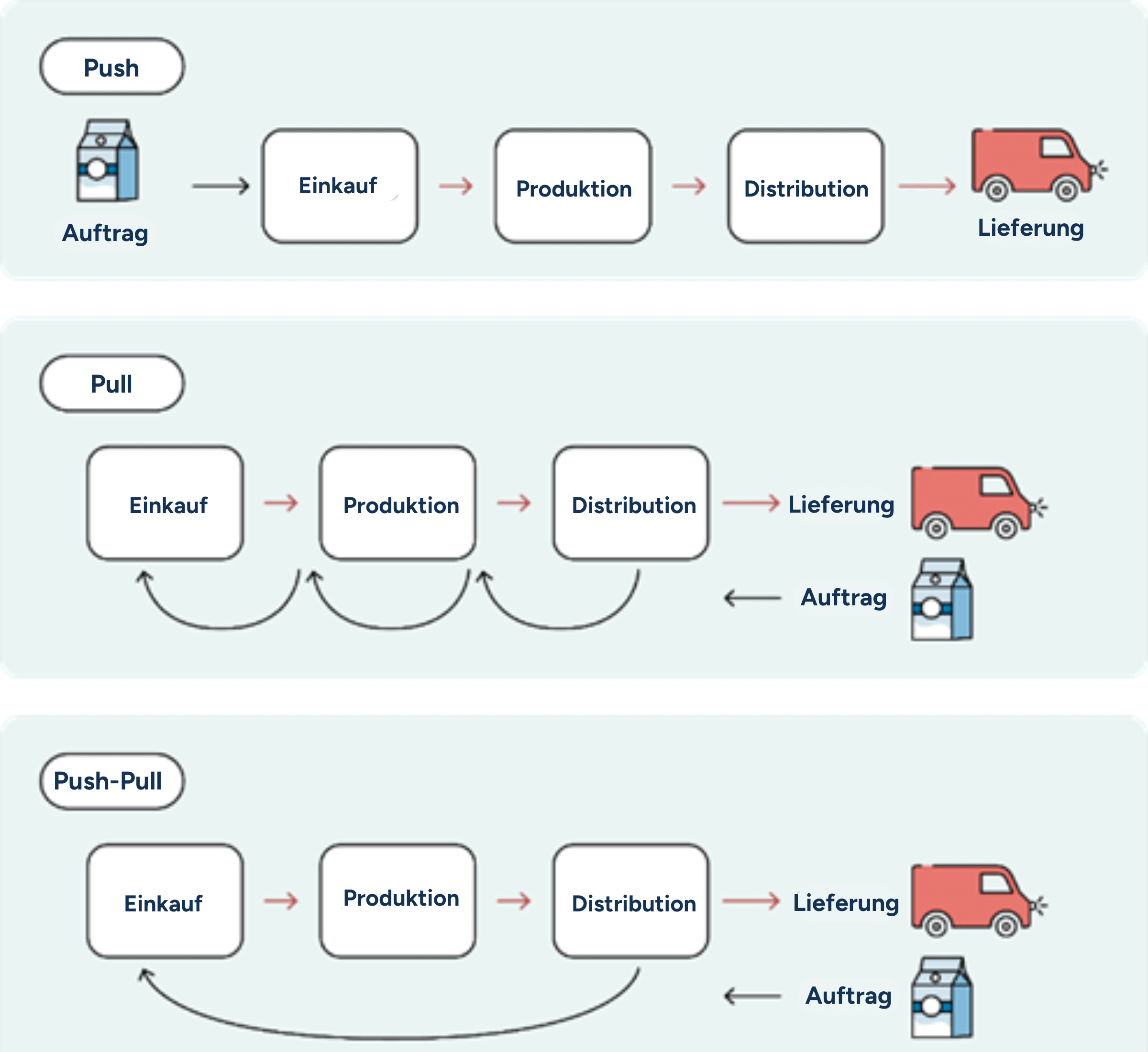
Der Haken dabei? Was kostenoptimal für den Hersteller ist, ist für seine Kunden nicht automatisch eine zufriedenstellende Lösung. So kann eine Optimierungssoftware ohne die entsprechenden Konfigurationen zu dem Schluss kommen, dass es billiger ist, die Aufträge eines Kunden in einem bestimmten Zeitraum komplett zu ignorieren, um die Aufträge eines anderen Handelspartners zu erfüllen.
Um solche Szenarien zu vermeiden, müssen Hersteller ihre betrieblichen Beschränkungen und Regeln in die Berechnungen einbeziehen können. Nur so können sie die Einhaltung vertraglicher Verpflichtungen und Produktionsbeschränkungen gewährleisten. Bei einer Planungssoftware mit umfassenden Funktionen wie der RELEX-Plattform ist dies Standard.
Das Hinzufügen der betrieblichen Einschränkungen und Regeln hilft Herstellern bei der Priorisierung von Produktionsmethoden: Diese kann dann auf der Grundlage der geschäftlichen Anforderungen und Ziele erfolgen. So kann etwa ein Hersteller von Frischwaren einen Plan erstellen, der darauf optimiert ist, Verderb zu vermeiden. Hersteller lagerfähiger Produkte mit besserer Kontrolle über ihr Angebot können dagegen Pläne erstellen, die die maximale Erfüllung von Kundenaufträgen priorisieren und optimieren.
Ein Rohmaterial in verschiedene Produkte umwandeln
Kostenoptimierte Pläne müssen auch die Komplexität der Zerlegung eines Rohstoffs berücksichtigen – also die Herstellung verschiedener Produkte aus einem einzigen Rohstoffmaterial. Nehmen wir Äpfel, aus denen verschiedene Produkte hergestellt werden können: zum Beispiel Apfelmus, -saft, -wein, -essig und -kuchen.
Hier liegt die Schwierigkeit darin, den Mix möglicher Endprodukte zu ermitteln, der die Kundenaufträge maximal rentabel erfüllt. Dazu muss der Hersteller mehrere Variablen abwägen, wie etwa:
- Die Priorität der Kundenaufträge. Welche Produkte werden sofort benötigt, um die lukrativsten Kundenverträge zu erfüllen?
- Die prognostizierte Nachfrage. Welche Produkte werden in nächster Zeit benötigt, um bevorstehende Nachfrageverschiebungen zu decken?
- Produktionsbeschränkungen. Wie sieht der effizienteste Produktionsplan aus, wenn die verfügbaren Produktionslinien, Stillstandszeiten für Umstellung und Reinigung und die verfügbaren Arbeitskräfte berücksichtigt werden?
- Materialknappheit. Wann kommt das nächste Los Rohstoffe an und wie viel Volumen wird es enthalten?
Selbst ein sehr erfahrenes Planungsteam hätte Schwierigkeiten, angesichts dieser Variablen den kostenoptimalen Plan zu berechnen. Auch wenn der optimale Produktmix manuell ermittelt werden könnte, würden die Berechnungen viel zu lange dauern, um noch darauf reagieren zu können. Insbesondere bei Herstellern, die sich noch auf manuelle Prozesse und unzählige Tabellenkalkulationen verlassen.
Die Schwierigkeit liegt darin, den Mix möglicher Endprodukte zu ermitteln, der die Kundenaufträge maximal rentabel erfüllt.
Eine Planungssoftware wie die RELEX-Plattform simuliert jedes denkbare Szenario. Sie berücksichtigt dabei Auftragsverpflichtungen, die Versorgungssituation und bestehende Produktionsbeschränkungen, um den rentabelsten und realistischsten Plan für den betreffenden Zeitraum zu ermitteln. Die Produktionspläne werden jede Nacht mit aktuellen Daten aktualisiert. So ist stets sichergestellt, dass der Produktionsplan trotz Änderungen in der Lieferkette jede Woche optimiert bleibt.
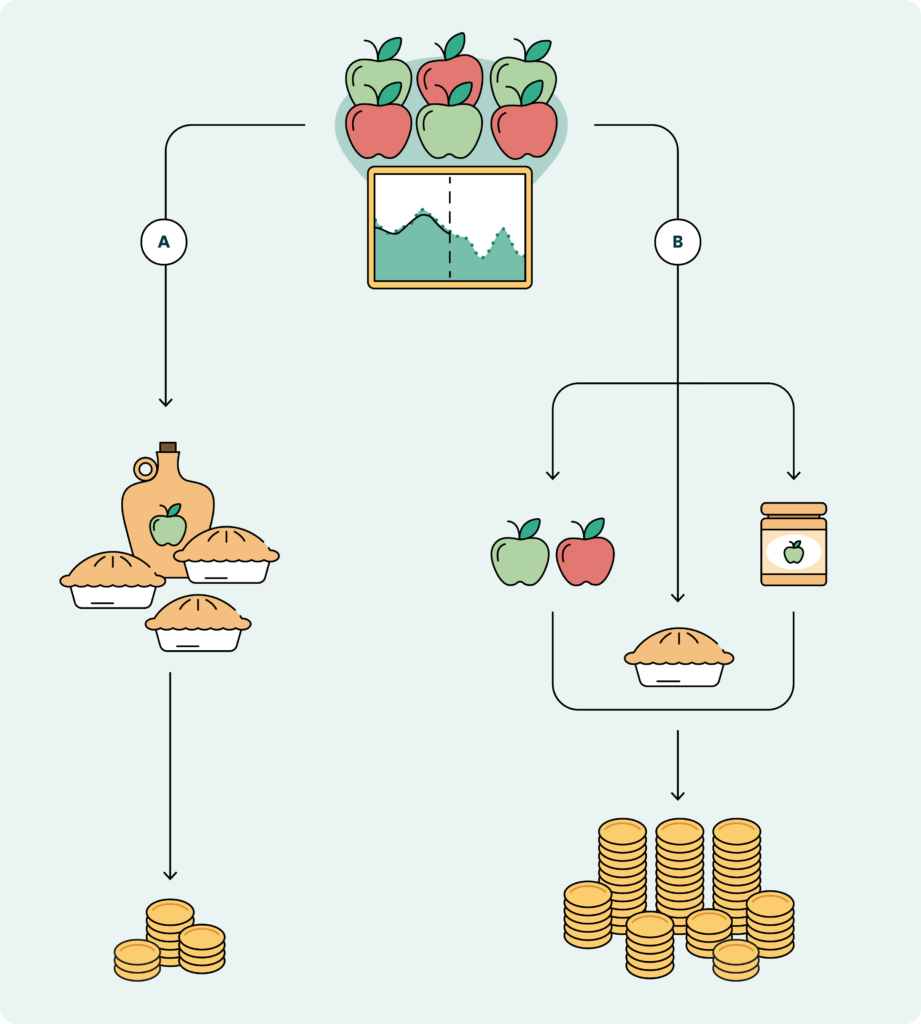
Insbesondere in der Fleischproduktion sind diese Simulationen von Vorteil, da die Gewinnspannen in der Regel gering sind. Ist beispielsweise die Nachfrage nach Hähnchenbrust weitaus höher als nach Hähnchenschenkeln, müsste der Hersteller das gesamte Huhn verwenden, um die benötigten Bruststücke zu erhalten. Dies würde dazu führen, dass zu viele Schenkel übrigbleiben, weil die Nachfrage nach diesen zu gering ist.
Eine moderne Planungssoftware schlägt dem Hersteller jedoch die optimalen Teilstücke vor, um die Produktion der nachgefragten Waren zu maximieren. Gleichzeitig empfiehlt eine solche Software auch alternative Verwendungsmöglichkeiten für die verbleibenden Teilstücke: So zum Beispiel die Umwandlung in Tiefkühlware, wodurch die Haltbarkeit verlängert und das Risiko des Verderbs verringert wird.
Die Planung teamübergreifend und über Zeithorizonte synchron halten
Manchmal besteht die größte Herausforderung darin, die verschiedenen Abteilungen eines Unternehmens an einen Tisch zu bringen. Vielen Lebensmittelherstellern fehlt eine einheitliche Grundlage der Planung und Datenanalyse – ein von allen gemeinsam genutzter „Masterplan“. Dieser Umstand zwingt die einzelnen Teams für Absatzplanung, Vertrieb, Produktion und Einkauf, ihre eigenen Systeme und Prozesse zu entwickeln.
Obwohl aus der Not entstanden, verschlimmern diese inoffiziellen Systeme die Planungsprobleme nur. Denn Daten, die für alle Abteilungen wichtig sind, liegen nur einer einzelnen Abteilung isoliert vor. Ohne die Möglichkeit, auf der Grundlage aktueller Daten in einer Live-Umgebung zusammenarbeiten zu können, ist es den Abteilungen nicht möglich, umfassende und langfristige Geschäftsziele abzustimmen. Stattdessen wird mit separaten Plänen gearbeitet, was eine Kostenoptimierung unmöglich macht.
Deshalb benötigen Hersteller eine Software-Plattform, die diese Silos auflöst und die Planung abteilungsübergreifend synchronisiert. Eine verbesserte interne Zusammenarbeit ermöglicht es dem Vertrieb, der Produktion und dem Einkauf, sich auf einen einzigen Plan zu verständigen. So können sie gemeinsam die Effizienz im gesamten Produktionsprozess maximieren und erkennen gleichzeitig, wie sich selbst kleine Entscheidungen auf übergeordnete Geschäftsziele auswirken.
Ein einheitliches, integriertes Planungssystem ermöglicht es dem Hersteller, eine neue Prognose zu erstellen, die sofort für alle Stakeholder sichtbar ist. Dadurch können die verschiedenen Teams an vielen Aufgaben gleichzeitig arbeiten, anstatt sie nacheinander zu erledigen. Hier einige Beispiele:
- Der Vertrieb kann mithilfe des digitalen Supply-Chain-Zwillings der Planungssoftware testen, ob die Prognose sich realistisch umsetzen lässt, und die Prognose gegebenenfalls korrigieren.
- Die Produktion kann Arbeitspläne erstellen und Ressourcen entsprechend der aktuellen Prognose zuweisen.
- Der Einkauf kann zusätzliche oder alternative Lieferanten ermitteln, um den Fluss von Rohstoffen konstant und möglichst kostengünstig zu halten.
Terminpläne, die erst in Wochen zum Tragen kommen, können mit umfassenden Fertigungsplänen abgestimmt werden, die über Monate hinweg ausgeführt werden – und mit Maßnahmen der Absatz- und Vertriebsplanung, die Jahre umfassen.
Die Vorteile eines konsolidierenden Planungssystems gehen über die horizontale Zusammenarbeit hinaus. Die verschiedenen Abteilungen können die Planung auch vertikal über Zeithorizonte und Planungsebenen hinweg synchronisieren. Terminpläne, die erst in Wochen zum Tragen kommen, können mit umfassenden Fertigungsplänen abgestimmt werden, die über Monate hinweg ausgeführt werden – und mit Maßnahmen der Absatz- und Vertriebsplanung, die Jahre umfassen.
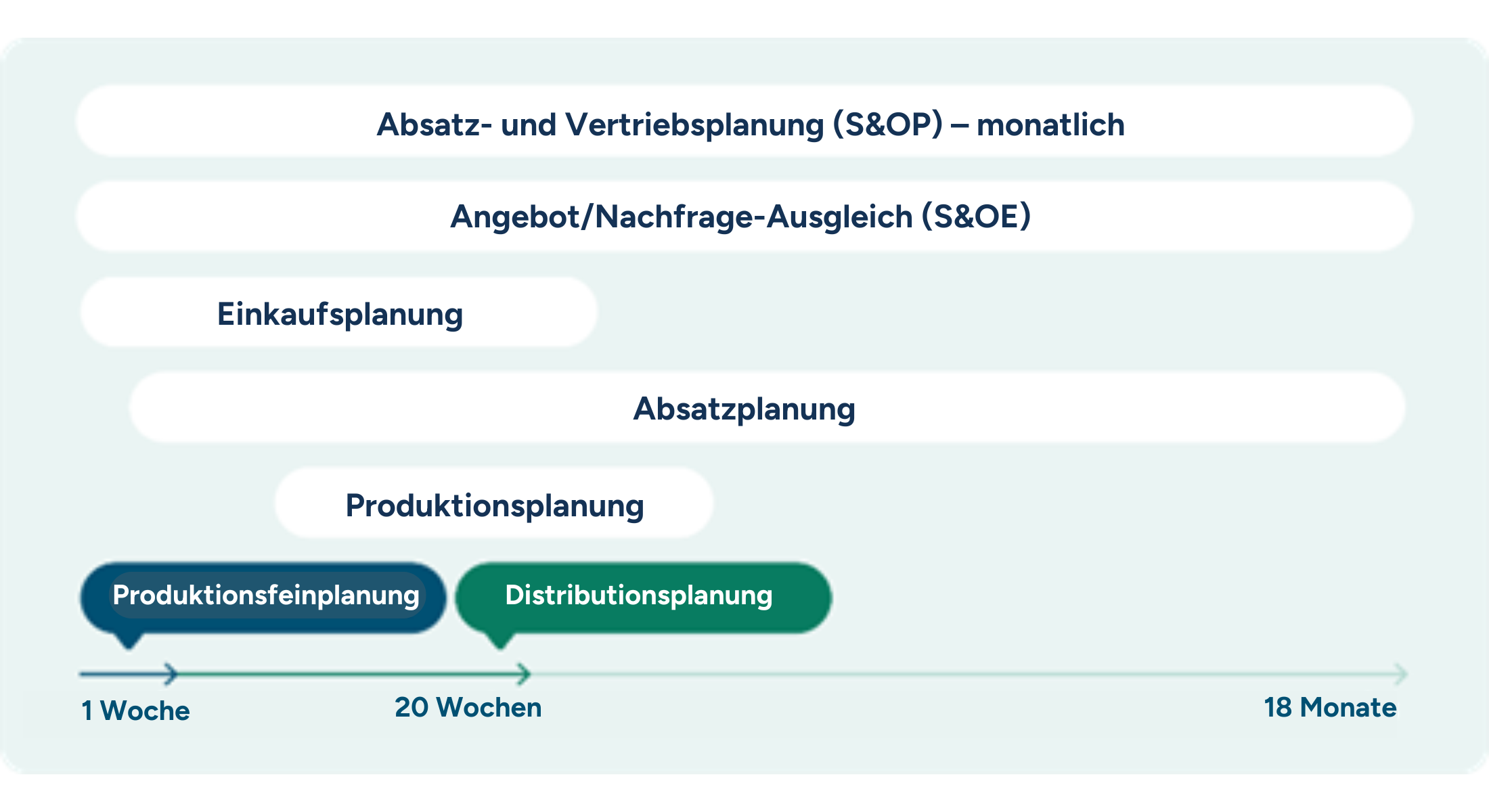
Anpassungen auf der einen Planungsebene wirken sich auf alle anderen Ebenen aus, so dass der Hersteller die interne Abstimmung beibehalten kann, ohne seine Anpassungsfähigkeit zu beeinträchtigen. Diese vollständige horizontale und vertikale Synchronisierung ermöglicht es Unternehmen, kurzfristig kostenoptimale Pläne zu erstellen, ohne dabei das langfristige Umsatzwachstum aus den Augen zu verlieren.
MEHR ERFAHREN: Wie Konsumgüterhersteller S&OP optimieren
Mit einer End-to-End Software-Plattform die Herausforderungen in der Lebensmittelherstellung meistern
Eine echte Optimierung der Lieferkette in der Lebensmittelverarbeitung erfordert ein ganzheitliches Verständnis von Angebot und Nachfrage. Gleichzeitig muss die Möglichkeit vorhanden sein, den Warenfluss von der Quelle bis zum Supermarkt zu visualisieren. Das ist kein Wunschtraum: Die Technologie, mit der dies erreicht wird, existiert bereits, und sie funktioniert. Leider decken viele Planungslösungen nur einen Bruchteil der wesentlichen Bedürfnisse eines Herstellers ab. Das führt dazu, dass er mehrere Tools kauft, die die Prozesse dann nur halbwegs verbessern.
RELEX bietet End-to-End-Transparenz und synchrone Planungsfunktionen: Diese sind erforderlich, um in einem stets herausfordernden Markt erfolgreich zu sein. Darüber hinaus arbeiten wir seit Jahren mit Herstellern, Großhändlern und Einzelhändlern von Lebensmitteln zusammen und kennen uns daher mit der Planung von Frische-Lieferketten besser aus als jedes andere Unternehmen. Gerne stellen wir das unter Beweis.
Lassen Sie sich Ihre Chance auf Kundenzufriedenheit und Gewinnwachstum nicht durch Lieferkettenchaos verbauen: Erfolgreich planen mit RELEX.