Warum Hersteller sich für eine synchronisierte, adaptive und autonome Planungslösung entscheiden sollten
Sep 18, 2024 • 8 min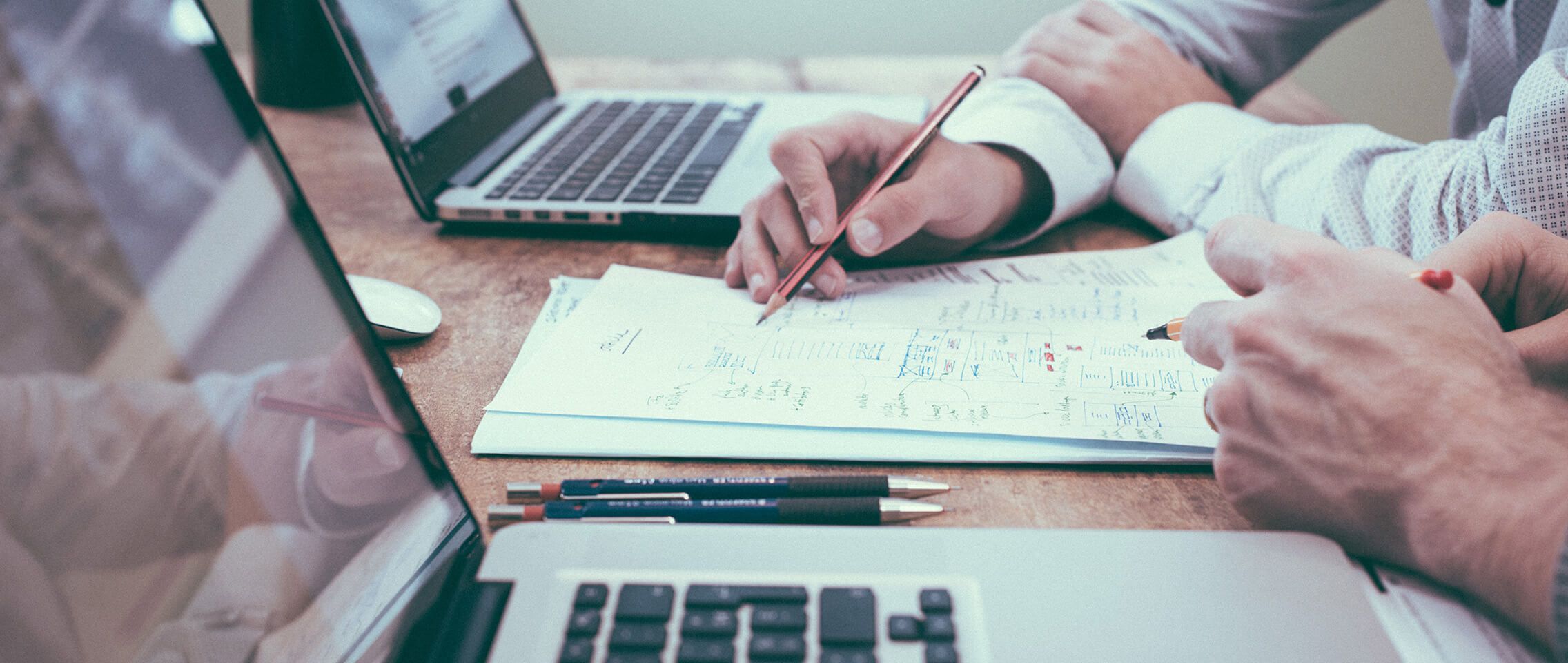
Materialbedarfsplanung (MRP) ist in der verarbeitenden Industrie schon so lange fester Bestandteil, dass heute kaum jemand in der Branche sich an eine Zeit davor erinnern kann. In den siebziger Jahren schrieben Experten über die Vorzüge von MRP: In einer Zeit, als sie zu Recht als bemerkenswerter Fortschritt in der Material- und Bestandsverwaltung galt.
Viele Unternehmen verlassen sich noch immer auf Materialbedarfsplanung – ziemlich beachtlich für ein derart in die Jahre gekommenes System. Die zunehmende Komplexität globaler Lieferketten hat jedoch die Grenzen dieser jahrzehntealten Technologie aufgezeigt. Und diese kosten Hersteller viel Geld.
Doch keine Sorge. Das Upgrade für MRP gibt es bereits: In Form von synchronisierten, anpassungsfähigen und autonomen Planungssystemen.
Moderne Planungstools bauen auf dem auf, was MRP einmal zum Standard in der Fertigung gemacht hat. Sie bieten jedoch robustere Lösungen für die Supply-Chain-Probleme, die Hersteller heute plagen. Denn die heutige Fertigung erfordert mehr Flexibilität, Transparenz und Optimierungsmöglichkeiten, als MRP-Systeme bieten können.
Was MRP kann – und was nicht
Bevor es MRP gab, lautete das Schlüsselwort bei der Planung „von Hand“. Die Planer erfassten die vorhandenen Bestände in Tabellen und berechneten die Rohstoffbestellungen selbst. Bestellungen bei Lieferanten gaben sie entweder per Telefon oder schriftlich in Auftrag. Jeder Schritt des Prozesses erforderte menschliche Eingaben. Dadurch war das gesamte System naturgemäß auch anfällig für menschliche Fehler.
Seit MRP-Software existiert, spart sie den Herstellern die Kosten dieser händischen Fehler. Sie führt erweiterte Berechnungen durch, um sicherzustellen, dass die richtigen Materialien zur richtigen Zeit verfügbar sind und Endprodukte termingerecht hergestellt werden können. Ein MRP-System verbessert die betriebliche Gesamteffizienz und Rentabilität in einer Weise, die Menschen mit manuellen Mitteln wie Tabellenkalkulation und Taschenrechner nicht erreichen könnten.
Ein MRP-System verbessert die betriebliche Gesamteffizienz und Rentabilität in einer Weise, die Menschen mit manuellen Mitteln wie Tabellenkalkulation und Taschenrechner nicht erreichen könnten.
MRP-Logik funktioniert rückwärts: Sie geht von einem Produktionsplan für Fertigerzeugnisse aus und verwendet die Stückliste (auch „Bill of Materials“ oder kurz „BOM“) jedes Produkts zur Berechnung der Rohmaterialkomponenten. Unternehmen leiten ihre Produktionspläne in der Regel aus einer Absatzprognose, Kundenbestellungen oder einer Kombination aus beidem ab. Dabei müssen auch der aktuelle Lagerbestand und die geforderten Sicherheitsbestände berücksichtigt werden.
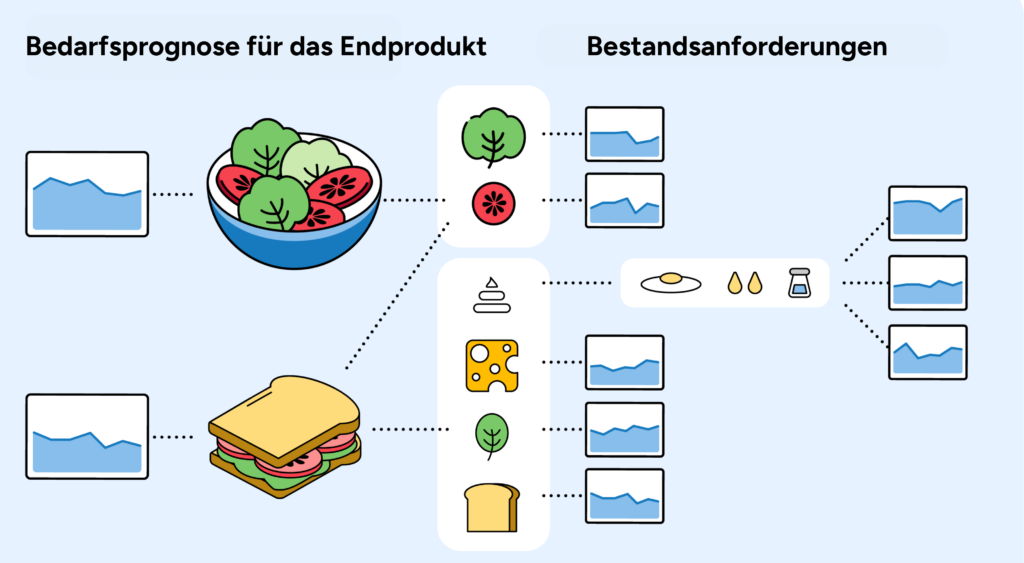
Diese Logik funktioniert insbesondere bei zwei Szenarien gut:
- Wenn Angebot und Nachfrage über einen langen Zeitraum ausgeglichen sind.
- Wenn der Hersteller über nahezu unbegrenzte kurzfristige Produktionskapazitäten verfügt und alle Rohstoffe leicht verfügbar sind.
In vielen Branchen, insbesondere in der Lebensmittel- und Getränkeindustrie, sind diese Szenarien jedoch selten. Fleisch-, Geflügel- und Fisch-verarbeitende Betriebe können sich am wenigsten auf Materialbedarfsplanung verlassen. Es gibt einfach zu viele Variablen, die plötzliche Nachfrageschwankungen verursachen können, zum Beispiel:
- Saisonalität wie beispielsweise die erhöhte Nachfrage nach Speiseeis im Sommer.
- Geschäftsentscheidungen wie etwa Werbeaktionen, insbesondere solche, die kurzfristig eingeleitet werden, um Monats- oder Quartals-Verkaufsziele zu erreichen.
- Betriebswirtschaftliche Beschränkungen und Herausforderungen wie z. B. Rohstoffknappheit, Maschinenverfügbarkeit und unerwartete Qualitätseinbußen.
Supply-Chain-Planer sind oft gleichzeitig mit Angebots- und Nachfrageschwankungen konfrontiert. Zwar bewältigt MRP die Aufteilung der Materialien problemlos, jedoch greift das System an anderer Stelle zu kurz. Nämlich wenn es darum geht, zu bestimmen, was, wann und wie viel produziert werden soll. Grund sind Faktoren wie diese:
- Eine Unfähigkeit, mit begrenzten Kapazitäten zu arbeiten, da Hersteller die Produktion auf der Grundlage fester Lieferzeiten planen.
- Begrenzte Kostenauswirkungen des Plans, da Aspekte wie Überstundenkosten, Lagerkosten und Betriebskapital keine Berücksichtigung finden.
- Bestehende physische Platzbeschränkungen, die die Anzahl der produzierten Waren, die realistischerweise gelagert werden können, begrenzen.
Ein Ungleichgewicht zwischen Angebot und Nachfrage führt häufig dazu, dass Disponenten verschiedene Datenelemente aus ihrem ERP-System und anderen Quellen extrahieren, um damit in Excel manuell einen ausbalancierten Plan zu erstellen. Diese Vorgehensweise hat jedoch häufig zur Folge, dass die Teams in arbeitsintensiven Aufgaben versinken – etwa der Validierung von Berechnungslogiken und der Überprüfung der Sinnhaftigkeit von Ein- und Ausgaben.
Häufig nimmt das Erstellen und Validieren eines Plans so viel Zeit in Anspruch, dass sich Angebot und Nachfrage in der Zwischenzeit verschieben und direkt wieder ein neuer Plan erstellt werden muss.
Leider endet die manuelle Arbeit nicht damit, dass ein Plan erstellt wurde. Als Nächstes muss das Team validieren, ob der Plan für das Unternehmen optimal ist – ein weiterer Zeitfresser. Häufig nimmt das Erstellen und Validieren eines Plans so viel Zeit in Anspruch, dass sich Angebot und Nachfrage in der Zwischenzeit verschieben und direkt wieder ein neuer Plan erstellt werden muss. Letztendlich stecken die Supply-Chain-Planer somit knietief in manuellen Arbeiten, die durch MRP eigentlich minimiert werden sollten.
Moderne digitale Lösungen bauen auf Materialbedarfsplanung auf und verbessern sie
Dass der MRP-Prozess so viel manuelle Arbeit beinhaltet, ist größtenteils in seinem auf Schritten basierenden Aufbau begründet: Um Artikel A zu produzieren, müssen Artikel B und C produziert werden, welche wiederum die Artikel D, E, F und G erfordern. Dieser Prozess gerät ins Stocken, sobald das System mit höherer Komplexität konfrontiert wird: zum Beispiel mit mehreren Produktlinien, Echtzeit-Aktualisierungen von Angebot und Nachfrage und spezifischen Produktionsbeschränkungen.
Optimierungslösungen wurden entwickelt, um zusätzliche Ebenen von Komplexität zu meistern. Die effektivsten Lösungen decken drei entscheidende Bereiche ab:
- Synchronisierte Planung, die die Entscheidungsfindung über alle Abteilungen, Funktionen und Planungsebenen hinweg vereinheitlicht;
- Adaptive Planung, die das gesamte Geschäft täglich an die tagesaktuellen Marktbedingungen anpasst;
- Autonome Planung, die Entscheidungen automatisiert, um die Effizienz zu steigern und profitabler zu werden.
Eine Lösung, die diese drei Bereiche adressiert, kann einen Plan auf der Grundlage der MRP-Logik vorschlagen und dabei alle definierten Geschäftsregeln und Einschränkungen gleichzeitig berücksichtigen. Die Software erkennt die Beschränkungen automatisch im Rahmen einer täglichen oder wöchentlichen Aktualisierung.
Hier einige Beispiele für definierte Beschränkungen:
- Maximale und minimale Produktionskapazität,
- Lagerkapazität,
- Distributionskapazität,
- Mindestbestellungen,
- Produktionsmengen.
Zusätzlich zu den oben genannten Beschränkungen müssen Hersteller gegebenenfalls verschiedene Geschäftsregeln berücksichtigen. Diese sind nicht immer so offensichtlich zu verstehen wie Beschränkungen. Sie können beispielsweise Folgendes vorsehen:
- Die Priorisierung von Produkt A gegenüber Produkt B auf Grundlage bestimmter Kriterien.
- Die Priorisierung von Kunde C gegenüber Kunde D auf Grundlage bestimmter Kriterien.
- Eine Präferenzsetzung, um zu verhindern, dass das Betriebskapital einen bestimmten Geldbetrag nicht überschreitet.
Moderne Lösungen bieten die Möglichkeit, solche Regeln festzulegen: Auf diese Weise erlauben sie es einem Unternehmen, optimierte Pläne im Einklang mit vordefinierten Geschäftszielen zu erstellen. In den meisten Fällen ist die Optimierung entweder auf Gewinnmaximierung oder auf Kosteneffizienz ausgerichtet. Die Regeln müssen nur dann aktualisiert werden, wenn sich das allgemeine Geschäftsumfeld ändert.
Eine Nachfragespitze kann ein MRP-System dazu veranlassen, einen Plan zu erstellen, der die Produktionskapazitäten eines Standorts übersteigt. Ein optimierter Plan dagegen kennt die Beschränkungen und arbeitet innerhalb dieser Grenzen.
Insbesondere wenn der Bedarf größer ist als das tatsächliche Angebot, ist die Fähigkeit, Pläne innerhalb einer Reihe von Beschränkungen und Regeln zu erstellen, Gold wert. Eine Nachfragespitze kann ein MRP-System dazu veranlassen, einen Plan zu erstellen, der die Produktionskapazitäten eines Standorts übersteigt. Ein optimierter Plan dagegen kennt die Beschränkungen und arbeitet innerhalb dieser Grenzen.
Bedenkt man, dass MRP-Systeme schon bei einfacheren Berechnungen einen zusätzlichen manuellen Aufwand für die Supply-Chain-Planer erzeugen, könnte man auf die Idee kommen, dass die wesentlich ausgefeilteren Berechnungen einer Optimierungssoftware die Arbeitsbelastung eines Planungsteams erst recht in die Höhe treiben.
Zum Glück ist dies nicht der Fall. Moderne Optimierungslösungen automatisieren und vereinfachen die Arbeit der Planer in einer Weise, wie es eine einfache MRP-Berechnung nicht könnte. Die Software automatisiert Schritte wie Datenextraktion, die Anwendung komplexer Geschäftsregeln und die Planvalidierung. Dadurch werden die Planer automatisch entlastet und können sich wertschöpfenden Aufgaben widmen, die Maschinen nicht ausführen können.
Zudem lässt sich Zeit sparen: durch Anpassungen in Echtzeit. Bei unerwarteten Ereignissen wie einem Maschinenausfall oder sich ändernden Kundenaufträgen bewertet die Lösung den Zeitplan neu und passt ihn so an, dass das ursprüngliche Enddatum eingehalten werden kann.
Mit moderner Software zur durchgehend integrierten Supply-Chain
Um betrieblich effizient und profitabel zu sein, muss jeder Teil des Fertigungsprozesses optimiert werden. Unternehmen sollten daher auf ganzheitliche Planungssysteme setzen, die die gesamte Lieferkette berücksichtigen. Eine synchronisierte, adaptive und autonome Lösung schlägt MRP bei der Produktionsplanung, der Produktionsterminierung und der Einkaufsplanung. Nimmt man noch die Distributions- und Absatzplanung hinzu, wird der Unterschied zwischen den beiden Softwaretypen noch eklatanter.
Distributionsplanung
MRP war nie wirklich in der Lage, die Distributionsplanung zu unterstützen, während die meisten heutigen Lösungen dies können.
Um die Distributionsplanung zu meistern, können Unternehmen zusätzliche Systeme oder Erweiterungen wie MRP II erwerben. Optimierungslösungen verfügen jedoch von Haus aus über die nötigen Funktionen zur Distributionsplanung. Diese Lösungen sind weitaus anpassungsfähiger. Sie berücksichtigen eine Vielzahl von Überlegungen, von den Versandkosten bis hin zu Kundenpräferenzen, um Lieferzeiten und Kosten innerhalb des Distributionsnetzes des Unternehmens zu reduzieren.
Integrierte Planung
Der vielleicht wichtigste Vorteil moderner Lösungen gegenüber einer MRP-Software ist ihre Konnektivität. Verschiedene Abteilungen, die alle mit der gleichen Lösung arbeiten, können dieselben aktuellen Daten verwenden, um Entscheidungen zu treffen. So entwickeln sie kurz- und langfristige Strategien anhand derselben Informationen. Diejenigen, die nicht mit einer solchen Lösung arbeiten, benötigen mehrere zusammengestückelte Tools und Integrationen. In der Praxis lässt sich auf diese Weise kein vergleichbares Niveau der Zusammenarbeit erreichen.
Komplexe Herausforderungen verlangen nach hochentwickelten Lösungen
Natürlich sind auch moderne Lösungen „nicht ohne“. Eine moderne Lösung ist komplexer und erfordert meist verschiedene Konfigurationen, um den individuellen Anforderungen des Herstellers gerecht zu werden und sich in seine bestehende IT-Infrastruktur zu fügen. Das spricht für die Anschaffung einer leicht konfigurierbaren Lösung, da diese Unternehmen hilft, die Schwierigkeiten zu überwinden und den Wert ihrer Investition schnell zu realisieren.
Für Sie als Hersteller empfiehlt es sich, einen erfahrenen Anbieter auszuwählen, der sein Wissen mit Ihnen teilt. Leicht konfigurierbare Lösungen können von Ihnen selbst oder im Rahmen eines vertrauenswürdigen Partnernetzes bereitgestellt werden. RELEX verfügt über eine ausgewiesene Erfolgsbilanz mit Optimierungen in Handel und Herstellung.
Wenn uns die Jahre mit massiven Schwankungen von Angebot und Nachfrage, Kostenexplosion und sinkenden Gewinnspannen eines gelehrt haben, dann, dass Lieferketten immer komplexer werden. Mit einer synchronisierten, adaptiven und autonomen Planungslösung vom Marktführer für Supply-Chain-Planung und -Optimierung sind Sie den Problemen in der Supply-Chain immer einen Schritt voraus und bleiben dauerhaft profitabel.