Comment une solution de planification permet de relever les défis de la production alimentaire
Nov 29, 2023 • 10 min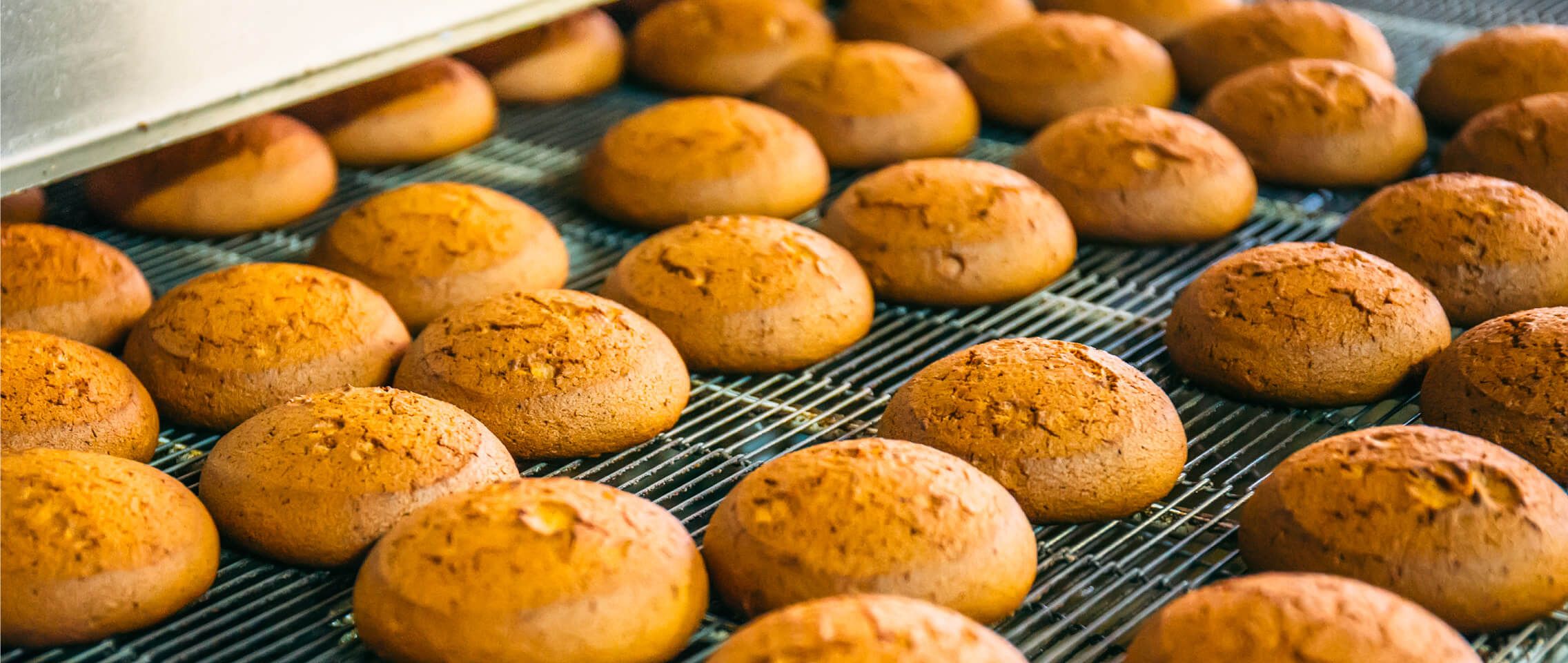
Les besoins de la demande par rapport aux réalités de l’offre. Contraintes de production et obligations des clients. Planification à long terme contre flexibilité à court terme.
Les planificateurs de l’industrie agroalimentaire sont perpétuellement sur la corde raide pour équilibrer les calendriers de production, les contraintes commerciales et la rareté des matériaux face à une demande en constante évolution et à la menace imminente de la détérioration des produits. Un changement dans l’une ou l’autre des variables peut faire grimper en flèche les niveaux de service et faire chuter la rentabilité – des résultats catastrophiques dans un secteur où les marges sont très étroites.
Même les équipes de planificateurs les plus compétentes constatent que les processus manuels, la planification déconnectée et le manque de visibilité sur la chaîne d’approvisionnement de bout en bout les empêchent d’équilibrer les obligations de production interfonctionnelles. En l’absence d’un plan unique, les planificateurs des différentes équipes peuvent se retrouver à travailler les uns contre les autres au lieu de collaborer pour satisfaire les obligations des clients et maximiser les bénéfices de l’entreprise.
La planification dans le secteur de la transformation alimentaire ne doit pas ressembler à un numéro de cirque. L’outil digital adéquat offrira aux entreprises la visibilité et les capacités de collaboration nécessaires pour relever les défis auxquels elles sont confrontées en matière de fabrication de produits alimentaires et pour exécuter les commandes des clients de la manière la plus rentable possible.
Équilibrer les modèles de production en flux tendu et en flux poussé
Les fabricants de produits alimentaires ont souvent du mal à trouver un équilibre entre la nécessité de maintenir un approvisionnement régulier et l’obligation de satisfaire la demande en constante évolution des clients.
Prenons l’exemple d’un fabricant de produits laitiers. La production hebdomadaire de lait est imprévisible. Si la production d’une semaine donnée est inférieure aux prévisions, l’entreprise aura du mal à déterminer les produits à fabriquer et les commandes clients en cours à satisfaire. Le problème inverse se pose également. Les fabricants sont souvent obligés de prendre la totalité du lait d’une ferme, quelle que soit la demande, et doivent utiliser la totalité du volume, quelle que soit la demande, sous peine de subir une détérioration coûteuse.
Poussée, traction et production hybride
Cet exemple illustre la tension entre les modèles de production “push” et “pull” communs à la transformation alimentaire. Dans un modèle “push” (également appelé “make-to-stock”), les entreprises produisent des biens en fonction des prévisions de la demande. Les entreprises produisent des articles à l’avance, ce qui leur permet d’honorer immédiatement les commandes des clients. Ce modèle fonctionne bien pour les produits congelés ou les produits de longue conservation comme les boissons, mais la nécessité de garder les produits en stock peut entraîner des risques accrus de détérioration pour les fabricants qui traitent des aliments frais.
La nécessité de garder le produit en stock peut entraîner des risques accrus de détérioration pour les fabricants qui traitent des aliments frais
Les modèles à flux tiré, “pull” (ou modèles “make-to-order”) fonctionnent à l’opposé du spectre. Les fabricants fabriquent et commandent des matières premières sur la base de prévisions, les demandes des clients n’arrivant généralement que quelques jours avant la date limite d’exécution. En d’autres termes, les produits sont essentiellement fabriqués sur commande. Les prévisions permettent aux fabricants de n’acheter que la quantité de matières premières nécessaire, ce qui réduit les coûts de stockage. Toutefois, ce modèle ne fonctionne pas lorsque la demande augmente, ce qui peut entraîner des commandes manquées et des relations tendues avec les clients.
Les aliments frais ne peuvent pas rester stockés longtemps, mais les entreprises ont également besoin de produits de base prêts à partir lorsque la demande évolue. La plupart des fabricants utilisent des modèles hybrides “push-pull” pour résoudre ces problèmes. Malheureusement, ces entreprises disposent rarement d’un système permettant de déterminer quelle combinaison de méthodologies “push” et “pull” maximise l’efficacité opérationnelle et la rentabilité.
Modèles push-pull optimisés en termes de rentabilité
Une plateforme de planification robuste peut équilibrer les prévisions de la demande et les commandes des clients, mais les meilleures vont plus loin. Au lieu de considérer les résultats en termes de méthodes “push” et “pull”, les plateformes avancées simulent tous les plans possibles pour identifier celui qui est le plus rentable ou le plus économique. Les fabricants atteignent toujours leurs objectifs grâce à un modèle de production hybride “push-pull”, mais ce sont les données qui déterminent la voie optimale à suivre, et non l’intuition ou les pratiques antérieures.
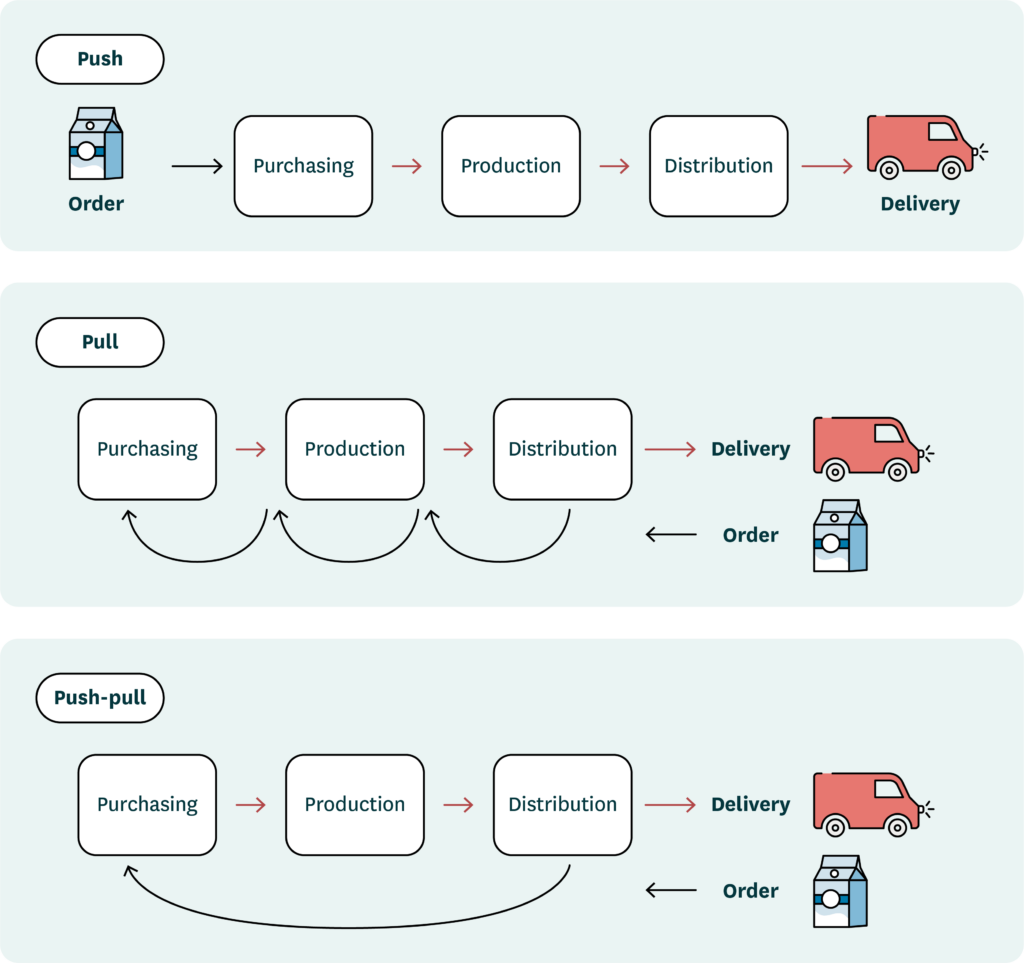
Le problème ? Ce qui est optimal en termes de coûts pour un fabricant n’est pas toujours satisfaisant pour ses clients. En l’absence de conseils, un logiciel d’optimisation peut déterminer qu’il est moins coûteux d’ignorer complètement les commandes d’un client sur une période donnée pour satisfaire les commandes d’un autre partenaire commercial.
Cette possibilité impose aux fabricants d’ajouter leurs contraintes et règles commerciales dans les calculs afin de garantir la prise en compte des obligations contractuelles et des limites de production. Heureusement, cette possibilité est offerte en standard par une plateforme de planification complète telle que RELEX.
L’ajout de ces contraintes et règles commerciales aide les fabricants de produits alimentaires à hiérarchiser les méthodes de production en fonction de leurs besoins et objectifs commerciaux. Un fabricant de produits frais peut créer un plan optimisé en fonction de ses préoccupations en matière de détérioration. De leur côté, les fabricants de produits de longue conservation qui maîtrisent mieux leurs approvisionnements peuvent créer des plans optimisés pour satisfaire au mieux les commandes de leurs clients.
LIRE : Pourquoi les fabricants d’aliments frais emballés doivent-ils donner la priorité à la fraîcheur ?
Convertir une source de matériaux en plusieurs produits
Les plans d’optimisation des coûts doivent également tenir compte de la complexité de la désagrégation, qui consiste à produire plusieurs produits différents à partir d’un seul type de matière première. Prenons l’exemple des boisseaux de pommes, à partir desquels les fabricants pourraient théoriquement produire toute une gamme de produits, notamment de la compote, du jus, du cidre, du vinaigre et des tartes.
La difficulté consiste à déterminer quelle combinaison de ces produits finis possibles répond de la manière la plus rentable aux commandes des clients. Pour ce faire, les fabricants doivent tenir compte de plusieurs variables, notamment
- La priorité de la commande du client. Quels sont les produits dont on a besoin immédiatement pour satisfaire aux obligations des contrats les plus lucratifs ?
- La demande prévue. Quels sont les produits qui seront bientôt nécessaires pour répondre aux variations prévues de la demande ?
- Les contraintes de production. Quel est le programme de production le plus efficace compte tenu des lignes de production disponibles, des temps d’arrêt pour le changement et le nettoyage, et de la main-d’œuvre disponible ?
- Rareté des matières premières. Quand le prochain lot de matières premières arrivera-t-il et quel volume contiendra-t-il ?
Même l’équipe de planification la plus compétente aurait du mal à effectuer les calculs nécessaires pour déterminer le plan le plus rentable compte tenu de ces variables. Si une équipe parvenait à déterminer manuellement la combinaison optimale de produits, les calculs prendraient probablement beaucoup trop de temps pour être appliqués. C’est particulièrement vrai pour les nombreux fabricants qui travaillent encore avec des processus manuels et qui utilisent un nombre incalculable de feuilles de calcul.
La difficulté consiste à déterminer quelle combinaison de produits finis possibles permet de répondre aux commandes des clients de la manière la plus rentable.
Les plateformes de planification telles que RELEX simulent tous les scénarios possibles et imaginables, en tenant compte des obligations de commande, des réalités de l’approvisionnement et des contraintes de production, afin de déterminer le plan le plus rentable et le plus réaliste pour la période concernée. Les plans de production sont mis à jour chaque nuit à l’aide de données actualisées, ce qui garantit que le plan de production d’une semaine donnée reste optimisé malgré les modifications de la chaîne d’approvisionnement.
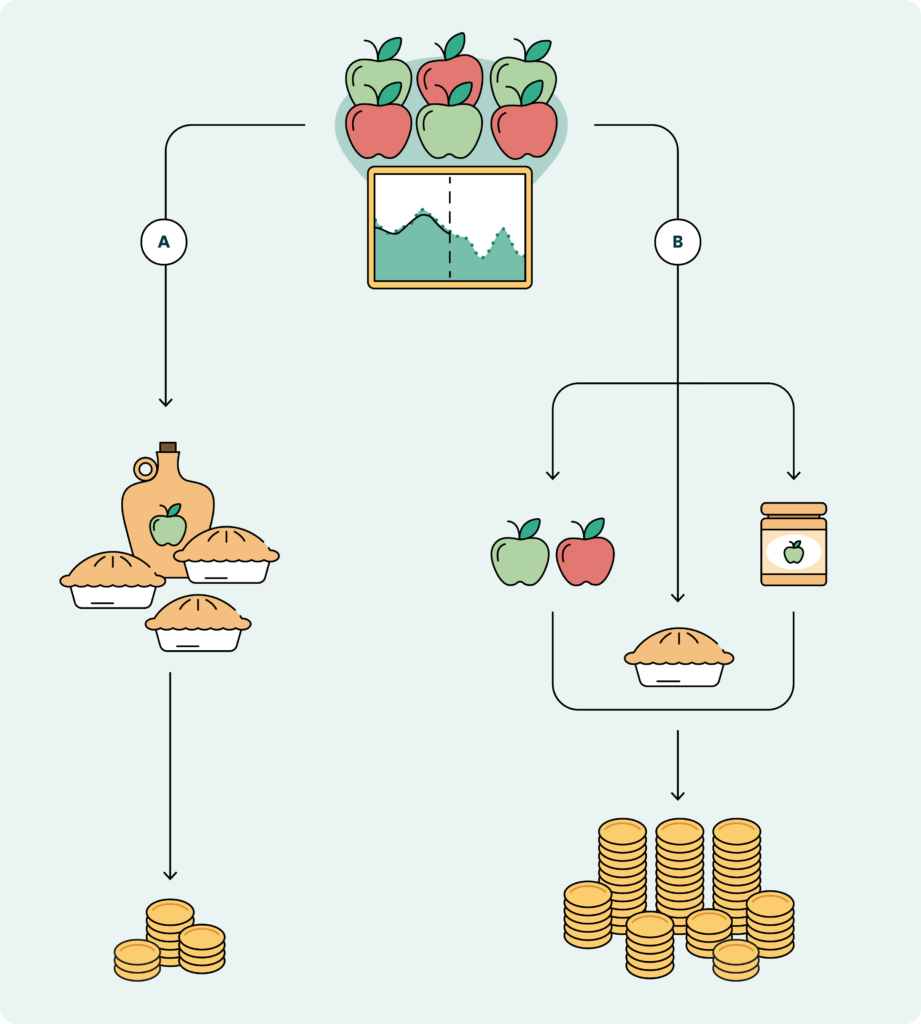
Ces simulations sont particulièrement utiles dans le secteur de la viande, où les marges sont généralement faibles. Supposons que la demande de poitrines de poulet soit beaucoup plus élevée que celle de cuisses. Les fabricants doivent récolter l’ensemble de la volaille pour obtenir les morceaux de poitrine nécessaires, ce qui laisse trop de cuisses et une demande insuffisante.
Les solutions de planification les plus avancées peuvent suggérer aux fabricants les coupes optimales pour maximiser la production des produits les plus demandés. La plateforme propose également d’autres utilisations pour les découpes restantes, comme la transformation en produits surgelés, afin d’augmenter la durée de conservation et d’atténuer les risques de détérioration.
Synchroniser la planification entre les équipes et les horizons temporels
Parfois, le plus grand défi consiste simplement à mettre les équipes d’une organisation sur la même longueur d’onde. De nombreux fabricants de produits alimentaires ne disposent pas d’une source unique de vérité en matière de planification et d’analyse des données. Cela oblige les équipes chargées de la demande, de la distribution, de la production et des achats à développer leurs propres systèmes et processus.
Bien que nés de la nécessité, ces systèmes distincts ne font qu’aggraver les problèmes de planification. Les données essentielles sont cloisonnées au sein de chaque équipe. Sans moyen de collaborer autour de données actualisées dans un cadre réel, les équipes ne peuvent pas s’aligner pleinement sur des objectifs plus larges de planification commerciale à long terme. Les équipes travaillent à partir de plans distincts, ce qui rend impossible l’optimisation des coûts.
Les fabricants ont besoin d’une solution qui déconstruise ces silos et synchronise la planification entre les équipes. L’amélioration de la collaboration interne permet aux ventes, aux opérations et aux achats de s’unir derrière un plan unique afin de maximiser l’efficacité du processus de production et d’identifier l’impact des moindres décisions sur les objectifs commerciaux de plus haut niveau.
Un système de planification unifié permet à un fabricant de créer une nouvelle prévision immédiatement visible par toutes les parties prenantes. Cela permet aux équipes de travailler simultanément sur de nombreuses tâches au lieu de les réaliser de manière séquentielle. Par exemple :
- L’équipe commerciale peut tester la faisabilité de l’exécution des prévisions à l’aide du jumeau numérique de la chaîne d’approvisionnement du logiciel de planification, et ajuster les prévisions en fonction des résultats.
- L’équipe chargée des opérations pourrait établir des calendriers de travail et allouer des ressources en fonction de la version la plus récente des prévisions.
- L’équipe chargée des achats pourrait identifier des fournisseurs supplémentaires ou alternatifs afin de maintenir un flux constant de matières premières au taux le plus rentable.
Les plans d’ordonnancement qui se déroulent en quelques semaines peuvent être alignés sur des plans de fabrication plus vastes exécutés sur plusieurs mois – et sur des initiatives de planification des ventes et des opérations qui s’étalent sur plusieurs années.
Les avantages d’un système de planification unifié vont au-delà de la collaboration horizontale. Les équipes peuvent également synchroniser la planification verticalement à travers les horizons temporels et les couches de planification. Les plans d’ordonnancement qui se déroulent en quelques semaines peuvent être alignés sur des plans de fabrication plus vastes exécutés au fil des mois – et sur des initiatives de planification des ventes et des opérations qui s’étalent sur des années. years.
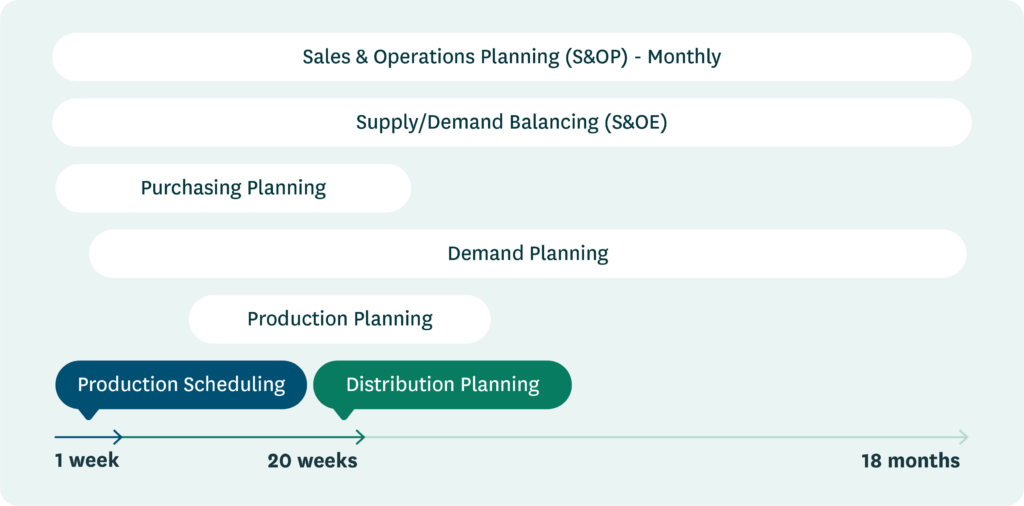
Les ajustements apportés à une couche de planification se répercutent sur les autres, ce qui permet aux fabricants de maintenir l’alignement interne sans sacrifier la capacité d’adaptation. Cette synchronisation horizontale et verticale totale permet aux entreprises d’élaborer des plans optimaux en termes de coûts à court terme sans perdre de vue la croissance du chiffre d’affaires à long terme.
Rechercher une solution de planification de bout en bout pour relever les défis de la production alimentaire
Une véritable optimisation de la chaîne d’approvisionnement de la transformation alimentaire nécessite une compréhension holistique de l’offre et de la demande et un moyen de visualiser le flux de marchandises de la source au supermarché. Il ne s’agit pas d’une chimère. La technologie permettant d’y parvenir existe actuellement et fonctionne à merveille. Malheureusement, de nombreuses solutions de planification ne répondent qu’à une infime partie des besoins importants d’un fabricant, ce qui l’oblige à acheter de multiples outils qui n’améliorent les processus qu’en demi-mesure.
RELEX offre la visibilité de bout en bout et les capacités de planification synchronisée nécessaires pour prospérer sur un marché en perpétuel défi. De plus, nous travaillons depuis des années avec des fabricants de produits frais, des grossistes et des détaillants. Nous connaissons donc mieux que quiconque la planification de la chaîne d’approvisionnement en produits frais, et nous aimerions vous le prouver.
Ne laissez pas le chaos de la chaîne d’approvisionnement gâcher vos chances de satisfaire vos clients et d’augmenter vos profits. Planifiez votre succès avec RELEX.