Découvrez pourquoi l’optimisation de la chaîne d’approvisionnement est essentielle pour les entreprises manufacturières qui cherchent à rationaliser leurs opérations et à maximiser leurs profits.
Les fabricants doivent prendre des décisions en temps réel, fondées sur des données, afin de garantir des opérations efficaces et un service à la clientèle de premier ordre. Pourtant, de nombreuses entreprises s’appuient encore sur des feuilles de calcul ou sur des outils de planification obsolètes (MRP – Material Requirements Planning).
La planification de la chaîne d’approvisionnement basée sur l’optimisation mathématique est fondamentalement différente des méthodes de planification traditionnelles et des calculs heuristiques plus simples qui sont souvent connus sous le nom d’optimisation. La planification mathématiquement optimisée permet aux fabricants de réagir rapidement et en toute confiance à l’évolution des conditions et de maximiser les performances de la chaîne d’approvisionnement.
Ce livre blanc illustre comment l’optimisation mathématique fonctionne comme l’une des capacités clés d’une solution solide de planification de la chaîne logistique – et comment les organisations peuvent l’utiliser pour rationaliser les opérations et maximiser les profits.
Pourquoi avez-vous besoin d’une optimisation ?
Les logiciels d’optimisation peuvent transformer la façon dont les entreprises planifient et gèrent leurs chaînes d’approvisionnement. Il offre plusieurs avantages distincts par rapport aux méthodes de planification traditionnelles, qui se concentrent souvent sur l’échelonnement des processus et la prise de décisions heuristiques.
Des plans réalistes
Les logiciels de planification et d’optimisation de la chaîne logistique adoptent une approche différente et plus réaliste que d’autres méthodes telles que le MRP, qui suppose une capacité et une disponibilité matérielle infinies. Les plans générés par le système prennent en compte les coûts et les contraintes de la chaîne d’approvisionnement dès le départ, ce qui les rend plus facilement réalisables. Les plans optimisés nécessitent rarement des ajustements manuels, ce qui réduit l’écart entre la planification et l’exécution.
Les plans générés par le système prennent en compte les coûts et les contraintes de la chaîne d’approvisionnement dès le départ, ce qui les rend plus facilement réalisables.
Optimisation des bénéfices
Les logiciels d’optimisation renvoient toujours le plan qui répond le mieux aux objectifs commerciaux globaux de l’entreprise : en général, le profit maximum. Cela est possible parce que le système évalue et optimise l’ensemble de la chaîne d’approvisionnement comme une entité unique, en tenant compte des coûts associés à chaque activité.
Vitesse de planification
Les algorithmes d’optimisation rapides comme l’éclair permettent aux planificateurs de générer des plans entièrement optimisés en quelques secondes. Ainsi, l’organisation peut toujours travailler sur des plans actualisés basés sur les données les plus récentes.
Planification de scénarios
La rapidité du système permet également aux planificateurs de simuler et d’évaluer rapidement l’impact de différents scénarios avant de prendre des décisions importantes en matière de planification.
Comment fonctionne l’optimisation de la chaîne d’approvisionnement ?
Il n’est pas nécessaire que l’utilisateur moyen comprenne les rouages de la modélisation mathématique et des techniques d’optimisation. Cela dit, il est utile que les planificateurs et les utilisateurs professionnels aient une compréhension de base de l’architecture du système afin d’établir la confiance dans le processus et ses résultats.
Examinons plus en détail les principaux composants d’une solution d’optimisation de la chaîne d’approvisionnement et leur impact sur les opérations commerciales au sens large :
1. Un jumeau numérique de la chaîne d’approvisionnement
Un jumeau numérique de la chaîne d’approvisionnement est une réplique virtuelle de votre chaîne d’approvisionnement physique. Il fournit le schéma directeur de la solution de planification et est stocké dans une base de données en mémoire pour un accès instantané et un traitement rapide.
Un jumeau numérique modélise les processus et les ressources de la chaîne d’approvisionnement d’une entreprise, y compris les coûts et les contraintes associés. Les usines, les lignes de production, les machines, les outils, les entrepôts, les véhicules et le personnel sont tous représentés ici. Il s’agit d’une simulation avancée de l’ensemble de la chaîne d’approvisionnement qui reçoit des mises à jour régulières de données provenant de nombreuses sources, ce qui permet de déterminer la manière dont les marchandises et les informations circulent dans le système.
2. Exigences en matière de données
La solution doit accéder à des informations précises et actualisées provenant de vos systèmes d’entreprise existants.
La plupart des données requises peuvent provenir du système ERP. Toutefois, des interfaces avec les systèmes de gestion du cycle de vie des produits (PLM), de gestion de la relation client (CRM), de gestion des transports et de gestion des entrepôts peuvent également s’avérer nécessaires.
Voici quelques exemples d’informations requises :
- Prévisions de vente
- Commandes des clients
- Données de base des produits
- Niveaux de stock
Il est important de disposer d’une solution flexible qui puisse s’interfacer avec toutes les sources de données potentielles.
3. Optimisation mathématique
Les problèmes à variables multiples sont difficiles à résoudre sans optimisation mathématique. Une solution d’optimisation utilise plusieurs algorithmes et solveurs en combinaison pour maximiser l’objectif défini. Elle le fait en tenant compte des contraintes définies par le jumeau numérique de la chaîne d’approvisionnement à travers les données d’entrée.
Ces contraintes comprennent (mais ne sont pas limitées à) :
- Recherche de fournisseurs et approvisionnement. Cette tâche implique l’optimisation du plan d’approvisionnement, y compris la sélection des fournisseurs, les quantités commandées et les fréquences de commande.
- Fabrication. Cette activité consiste à optimiser les plans de production, y compris les options d’externalisation et les calendriers de production détaillés.
- Inventaire. Le moteur de règles de gestion établit des niveaux de stock de sécurité dynamiques et d’autres paramètres d’inventaire.
- Distribution. Cette tâche implique l’optimisation des itinéraires d’expédition, la sélection des modes de transport et les calendriers de livraison.
Le plus souvent, l’objectif est soit un profit maximal, soit un service à la clientèle maximal au coût le plus bas. Il est également possible d’optimiser en fonction d’autres facteurs, tels que la production la plus faible de CO2.
Quelle que soit l’option choisie par l’entreprise, la solution trouvera l’option globale optimale pour l’entreprise tout en tenant compte des règles, des coûts et des contraintes prédéfinis.
4. Interface utilisateur
L’interface utilisateur est conçue pour maximiser la productivité des planificateurs. Elle sépare l’utilisateur final de la complexité de la modélisation mathématique et des calculs qui ont lieu dans les coulisses.
Des tableaux de bord configurables et des outils de visualisation soutiennent le travail du planificateur, et les utilisateurs peuvent facilement surveiller les indicateurs clés de performance et suivre l’évolution de leurs efforts d’optimisation.
Le système émet des alertes, des exceptions et des notifications en temps réel pour informer les utilisateurs des événements critiques ou des écarts par rapport au plan optimisé. Les planificateurs peuvent alors choisir de traiter les problèmes manuellement ou d’exploiter les capacités de simulation du système pour explorer les options et s’assurer qu’ils prennent les bonnes décisions.
Les outils de flux de travail garantissent le respect des processus de planification et des protocoles de communication. En outre, les planificateurs peuvent facilement regrouper les informations pour obtenir une vue d’ensemble de la chaîne d’approvisionnement, car il n’y a qu’une seule source de données de planification. Ils peuvent également approfondir les données pour déterminer la cause première de problèmes spécifiques.
Pour trouver le plan optimal, il faut d’abord définir le problème de planification et les paramètres qui l’encadrent. Une fois qu’un modèle numérique de la chaîne d’approvisionnement est en place, les algorithmes d’optimisation mathématique peuvent se mettre au travail.
Exemples d’optimisation
Pour mieux comprendre la différence entre l’optimisation de la chaîne logistique et le MRP, examinons comment chaque système répond à deux défis communs en matière de planification.
Exemple 1 : Gamme de produits
Dans le premier exemple, nous examinons de plus près la manière dont le système utilise la modélisation mathématique pour optimiser un problème de planification.
Le scénario est celui d’une boulangerie qui souhaite déterminer une combinaison optimale de produits. Pour rester simple, nous considérons deux produits, le pain et les brownies, et deux ingrédients, la farine et le sucre.
Optimiser la gamme de produits grâce à l’optimisation
L’approvisionnement en farine est limité à 50 kg pour la période. Le système de planification accède aux nomenclatures des produits et constate qu’un pain nécessite 1 kg de farine et un brownie ½ kg. Le graphique ci-dessous montre l’assortiment de produits possible compte tenu de la contrainte de farine.
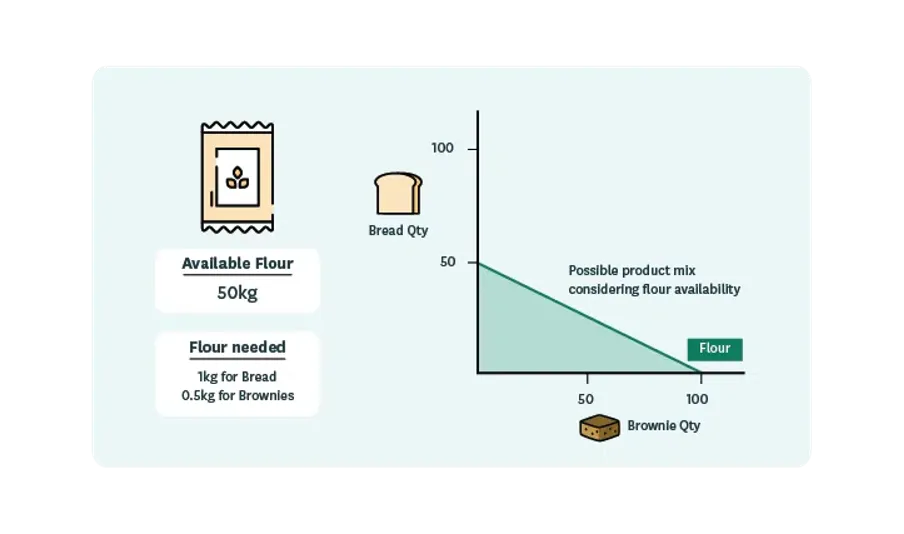
Après l’ajout d’une contrainte d’offre pour le sucre, l’assortiment de produits possible est le suivant.
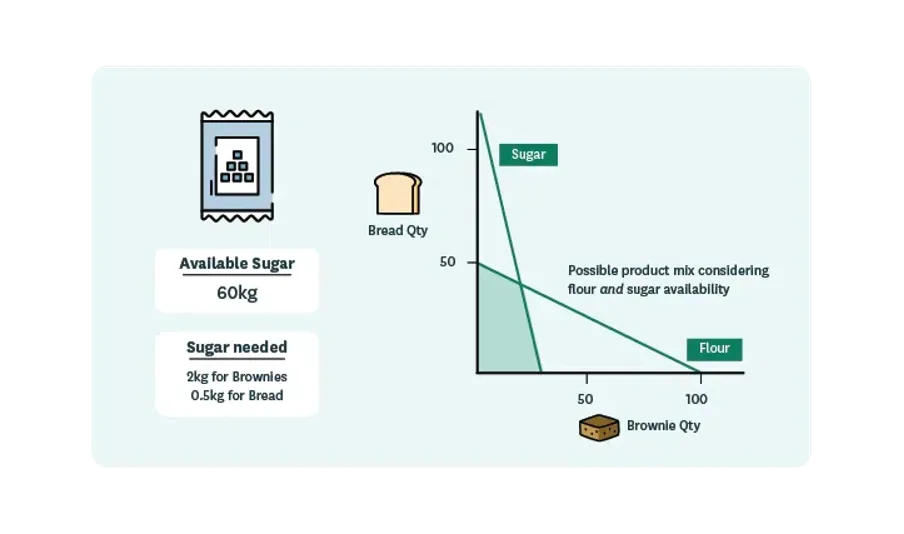
Ensuite, la prévision de la demande est prise en compte. Nous ne voulons pas produire plus que ce pour quoi nous avons une demande (45 pains et 25 brownies), de sorte que l’éventail des produits possibles est encore réduit.
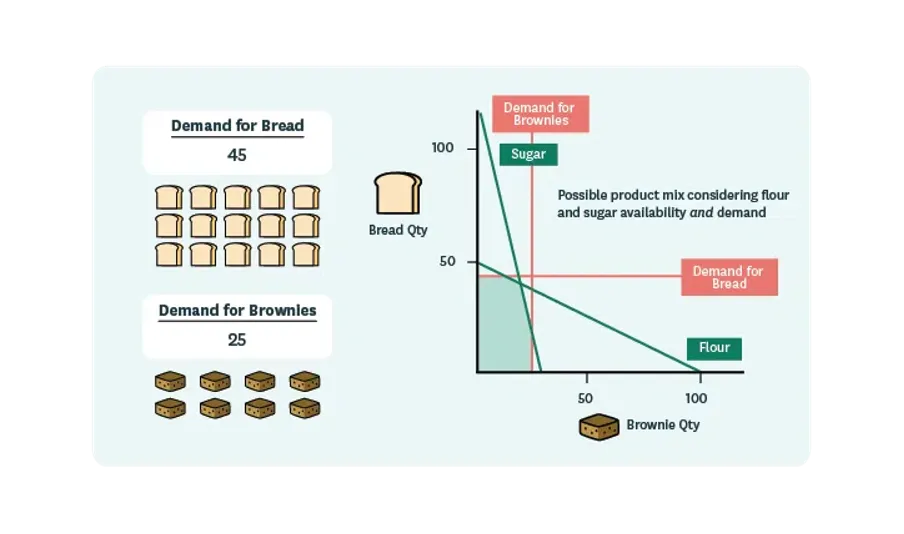
La combinaison optimale de produits est celle qui permet à la boulangerie de réaliser le maximum de bénéfices. Avec une contribution au bénéfice de 1,50 $ pour le pain et de 2,00 $ pour les brownies, le système dispose de toutes les informations nécessaires pour déterminer la composition optimale.
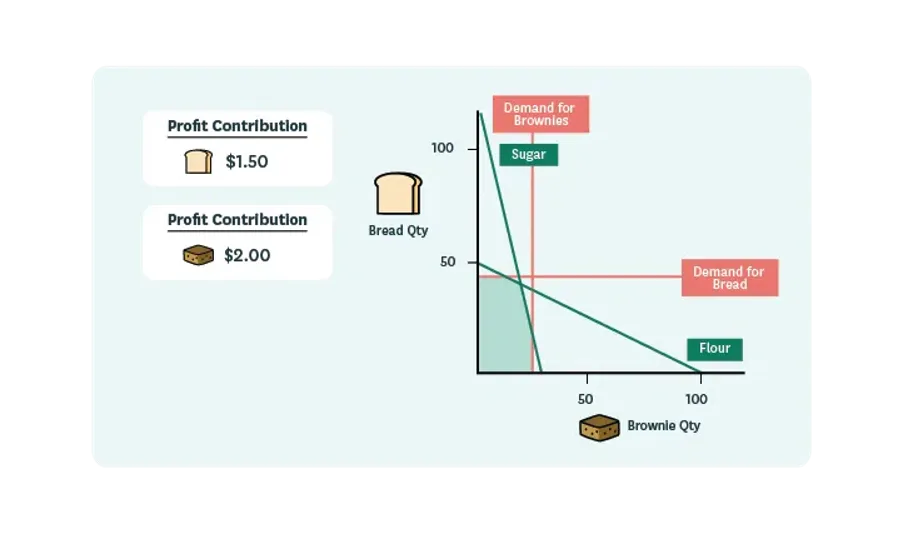
Dans cet exemple, un algorithme de programmation linéaire (LP) est utilisé pour déterminer la gamme de produits optimale. Le système établit la ligne de contribution aux bénéfices et trouve l’optimum. N’oubliez pas que tout cela se fait automatiquement !
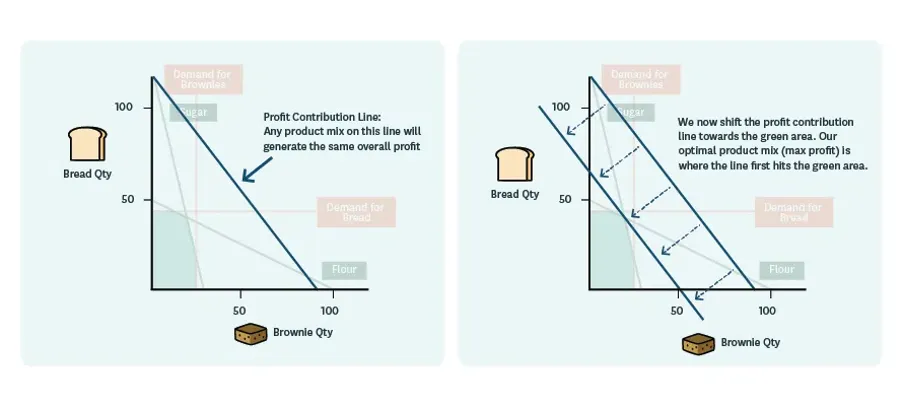
La combinaison optimale de produits est de 40 pains et 20 brownies.
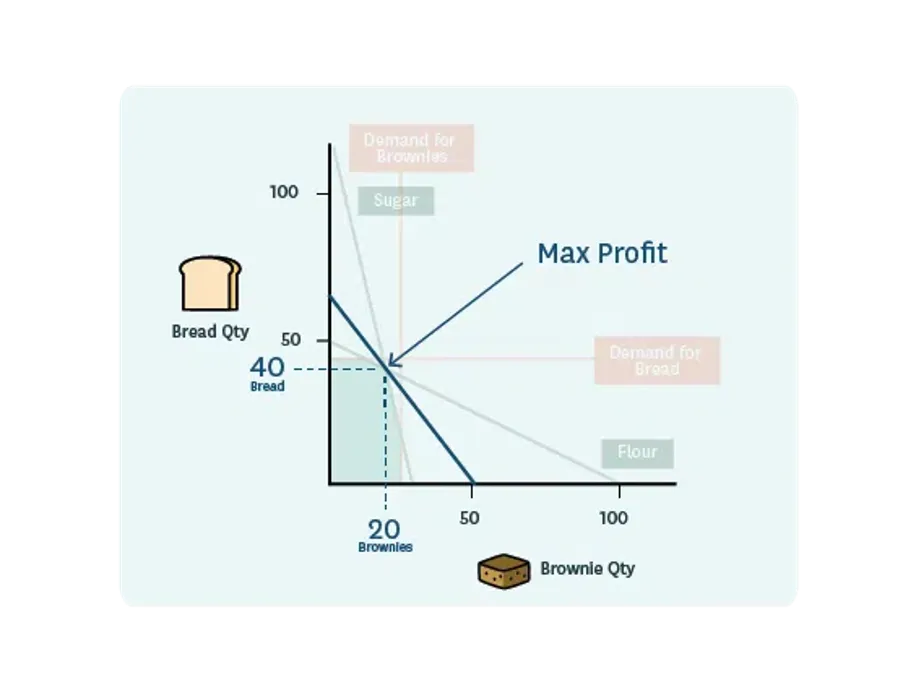
L’exemple ci-dessus est très simple, mais la beauté de l’optimisation mathématique réside dans le fait qu’il est possible d’obtenir les mêmes résultats optimisés pour les chaînes d’approvisionnement les plus complexes. Les algorithmes peuvent optimiser la production, le stockage et la distribution de milliers de produits en concurrence pour des matériaux et des ressources limités en quelques secondes.
Optimisation de la gamme de produits sans optimisation
Sans optimisation, un plan aurait supposé un approvisionnement illimité en farine et en sucre. Ce n’est qu’ensuite que des contraintes peuvent être ajoutées, nécessitant l’intervention manuelle d’un planificateur.
Exemple 2 : Constitution d’un stock
Les entreprises confrontées à la saisonnalité ou à de grandes promotions doivent trouver le meilleur moyen de constituer des stocks en prévision d’un pic de la demande.
Il existe deux stratégies de base : constituer progressivement le stock nécessaire au fil du temps ou ajouter une capacité supplémentaire à l’approche du pic.
La constitution progressive des stocks permet de maintenir un calendrier de production régulier et rentable et de tirer parti des capacités inutilisées. Toutefois, comme elle implique de conserver les stocks plus longtemps, les coûts de stockage et de manutention sont plus élevés. Cette stratégie présente également un risque accru de péremption et d’obsolescence des produits.
Les diagrammes ci-dessous illustrent la constitution progressive des stocks en maintenant une utilisation constante de la ligne (40 unités par semaine) en prévision d’un pic de la demande au cours des semaines 28 à 32.
Constitution d’un stock sur une période plus longue
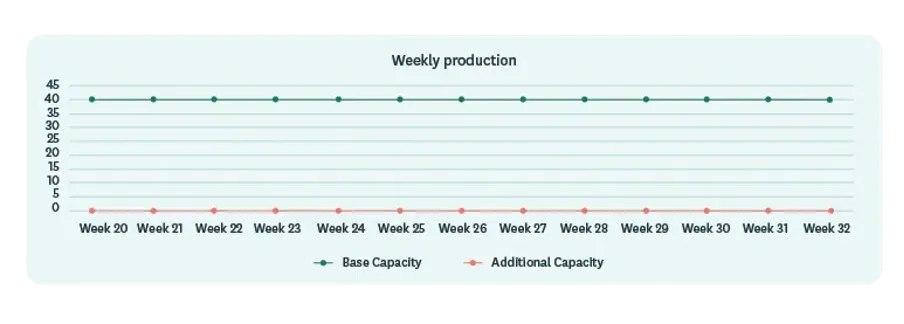
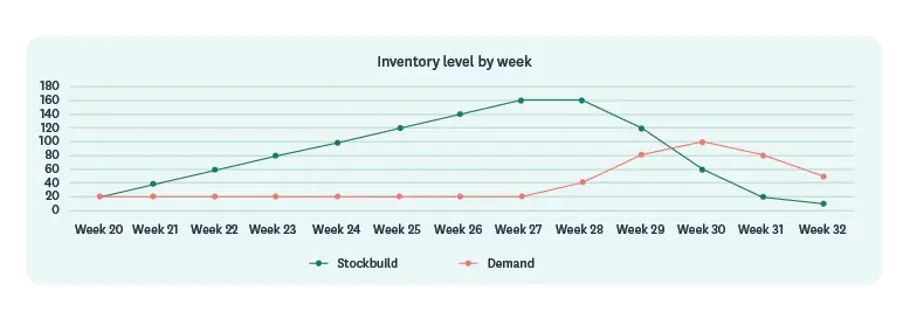
L’autre solution consiste à augmenter la capacité de production à proximité du pic de la demande. Cela peut se faire par l’ajout d’équipes supplémentaires, le redéploiement des capacités internes ou le recours à des partenaires d’externalisation.
Construire plus près du pic de production permet de maintenir les niveaux de stocks et les coûts liés aux stocks à un faible niveau. Toutefois, l’ajout d’une capacité de production à court terme se paie généralement au prix fort, si tant est qu’il s’agisse d’une option.
Constitution de stocks à l’aide de capacités supplémentaires à l’approche du pic de la demande
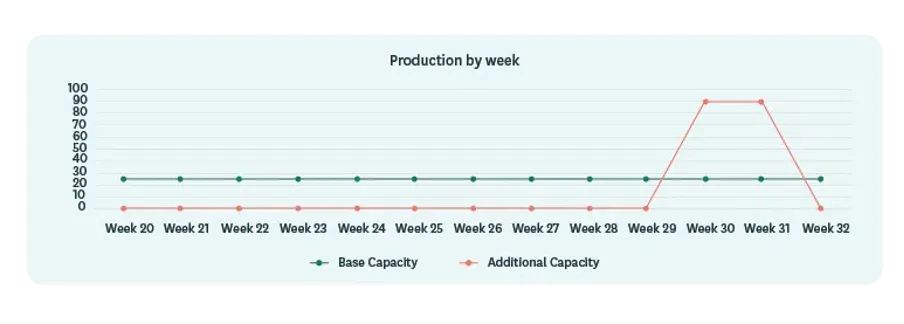
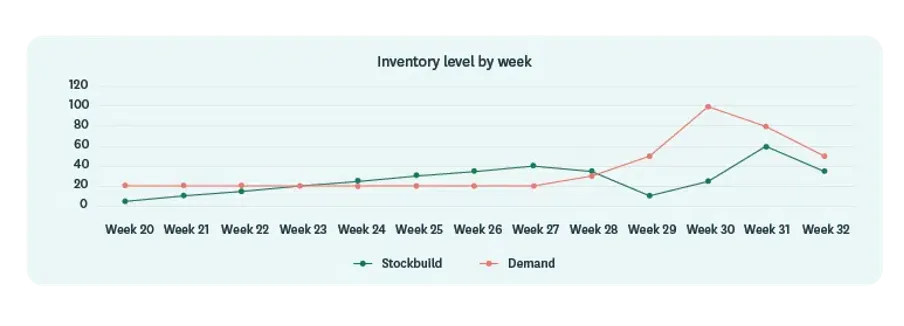
Les graphiques ci-dessus montrent la différence entre les deux options. Mais comment savoir quelle est la meilleure option ? Il pourrait même s’agir d’une combinaison des deux options.
Si l’on considère un seul produit de manière isolée, il ne s’agit pas d’un problème complexe. Des scénarios plus réalistes impliquent souvent des centaines, voire des milliers de produits en concurrence pour les capacités de production, de stockage et de distribution sur plusieurs sites. Dans ce cas, la solution optimale est rarement évidente et peut surprendre même des planificateurs expérimentés.
Planification de la constitution du stock avec optimisation
Dans un monde où les ressources sont limitées et les perturbations apparemment infinies, la planification implique toujours des compromis. Une solution d’optimisation de la chaîne d’approvisionnement identifiera la stratégie de constitution de stocks qui répond le mieux aux objectifs généraux de votre entreprise, qu’il s’agisse de maximiser les bénéfices globaux ou d’atteindre les objectifs de service à la clientèle au coût le plus bas possible.
Tant que le solveur mathématique a accès aux données qui encadrent le problème de planification, il peut effectuer l’optimisation nécessaire. Comme le solveur mathématique prend en compte l’ensemble de la chaîne d’approvisionnement, le planificateur n’a pas besoin de demander au système de constituer des stocks. Le système s’en charge automatiquement dans le cadre de la réalisation de l’objectif d’optimisation.
Dans cet exemple, le modèle de chaîne d’approvisionnement définit les coûts et les contraintes liés aux heures supplémentaires, au coût du capital, à la péremption des produits, à la taille des lots, à la gamme de produits, etc. Combiné à la demande et aux informations sur les stocks disponibles provenant de systèmes tiers, le solveur dispose de tous les éléments nécessaires pour calculer le plan optimal.
Planification de la constitution des stocks sans optimisation
La planification du même stock à l’aide des fonctionnalités MRP et DRP d’un système ERP est un défi tout à fait différent.
Incapables de prendre en compte les coûts et les contraintes, le MRP et le DRP doivent faire une série d’hypothèses, notamment une capacité infinie et des délais de production et de distribution fixes. Cependant, la capacité est rarement illimitée et les délais ne sont pas fixes par définition. Ils dépendent plutôt de la disponibilité des matériaux et de la capacité de production, de stockage et de distribution. Par conséquent, les plans générés par le MRP sont de bien moindre qualité, et le planificateur se retrouve avec beaucoup de travail pour valider la faisabilité opérationnelle du plan.
L’incapacité de la planification des ressources à fournir un plan pouvant être exécuté “prêt à l’emploi” n’est qu’une partie du problème. Comme la planification des ressources ne tient pas compte du coût et de la rentabilité globale du plan, il est pratiquement impossible de déterminer si le plan répond aux objectifs commerciaux de l’entreprise.
Changer le rôle du planificateur
En tant que planificateur, l’utilisation d’une solution d’optimisation de la chaîne logistique est très différente de celle d’un système MRP (sans optimisation mathématique).
Avec le MRP, les planificateurs peuvent voir qu’il y a un problème, mais ils doivent trouver eux-mêmes comment le résoudre. Cela prend du temps et les décisions de planification importantes risquent d’être basées sur une intuition plutôt que sur des données et des faits en temps réel.
La création d’un plan entièrement réalisable et commercialement optimisé à l’aide d’un logiciel d’optimisation de la chaîne d’approvisionnement est presque instantanée. Qu’il s’agisse de préparer différents scénarios de planification pour le cycle S&OP mensuel ou de résoudre un problème de production immédiat, les planificateurs peuvent apporter une plus grande valeur ajoutée à l’organisation.
Grâce à un système qui modélise et optimise l’ensemble de la chaîne d’approvisionnement, les planificateurs et les parties prenantes de l’entreprise ont une visibilité complète de toutes les activités planifiées et de leurs interactions. Si un aspect du plan est modifié, les répercussions sont immédiatement visibles. Cela permet une prise de décision plus rapide et de meilleure qualité.
Les six principaux impacts de l’optimisation sur le rôle d’un planificateur sont les suivants :
- L’amélioration de l’automatisation de la planification permet de consacrer plus de temps aux exceptions.
- L’amélioration des capacités d’analyse de la visibilité de la chaîne d’approvisionnement permet aux planificateurs d’identifier et de traiter les problèmes de la chaîne d’approvisionnement avant qu’ils ne deviennent des problèmes.
- Les plans peuvent être exécutés “prêts à l’emploi” avec peu ou pas d’ajustements manuels.
- La rapidité des algorithmes d’optimisation permet aux planificateurs d’effectuer plusieurs analyses de simulation avant de prendre des décisions importantes.
- Le planificateur maintiendra le “jumeau numérique”, en actualisant les règles, les coûts et les contraintes de l’entreprise.
- En règle générale, la fonction de planification devient plus stratégique au fur et à mesure que la confiance grandit. Elle peut notamment jouer un rôle plus central dans le cycle de planification des ventes et des opérations (S&OP) ou de planification intégrée des activités (IBP) de l’entreprise.
Comment démarrer l’optimisation de la chaîne d’approvisionnement
L’optimisation de la chaîne d’approvisionnement peut apporter une valeur ajoutée significative aux entreprises de fabrication et de distribution de toutes tailles. Grâce aux récents progrès de la technologie informatique, les solutions sont devenues de plus en plus abordables et conviviales, et les entreprises qui souhaitent en tirer parti peuvent le faire en toute confiance.
La nature modulaire des solutions d’optimisation de la chaîne d’approvisionnement permet aux entreprises de commencer à petite échelle et d’étendre progressivement l’empreinte de la solution, minimisant ainsi les risques et les coûts du projet. RELEX recommande de cibler d’abord les domaines de planification où la technologie apportera le plus de valeur ajoutée. C’est pourquoi de nombreuses entreprises choisissent de s’attaquer à la planification de la production et des stocks à long terme avant de passer à l’ordonnancement de la production à court terme.
En fin de compte, la planification de la chaîne d’approvisionnement basée sur l’optimisation mathématique a le pouvoir de transformer votre entreprise – en particulier lorsqu’elle est utilisée comme l’un des nombreux outils de la boîte à outils de la planification de la chaîne d’approvisionnement d’une entreprise. Toute entreprise de fabrication ou de distribution qui n’utilise pas encore cette technologie devrait découvrir ce qu’elle représente pour son service à la clientèle et ses résultats.