The need for a next-level advanced planning and scheduling (APS) solution in manufacturing
Dec 13, 2023 • 7 min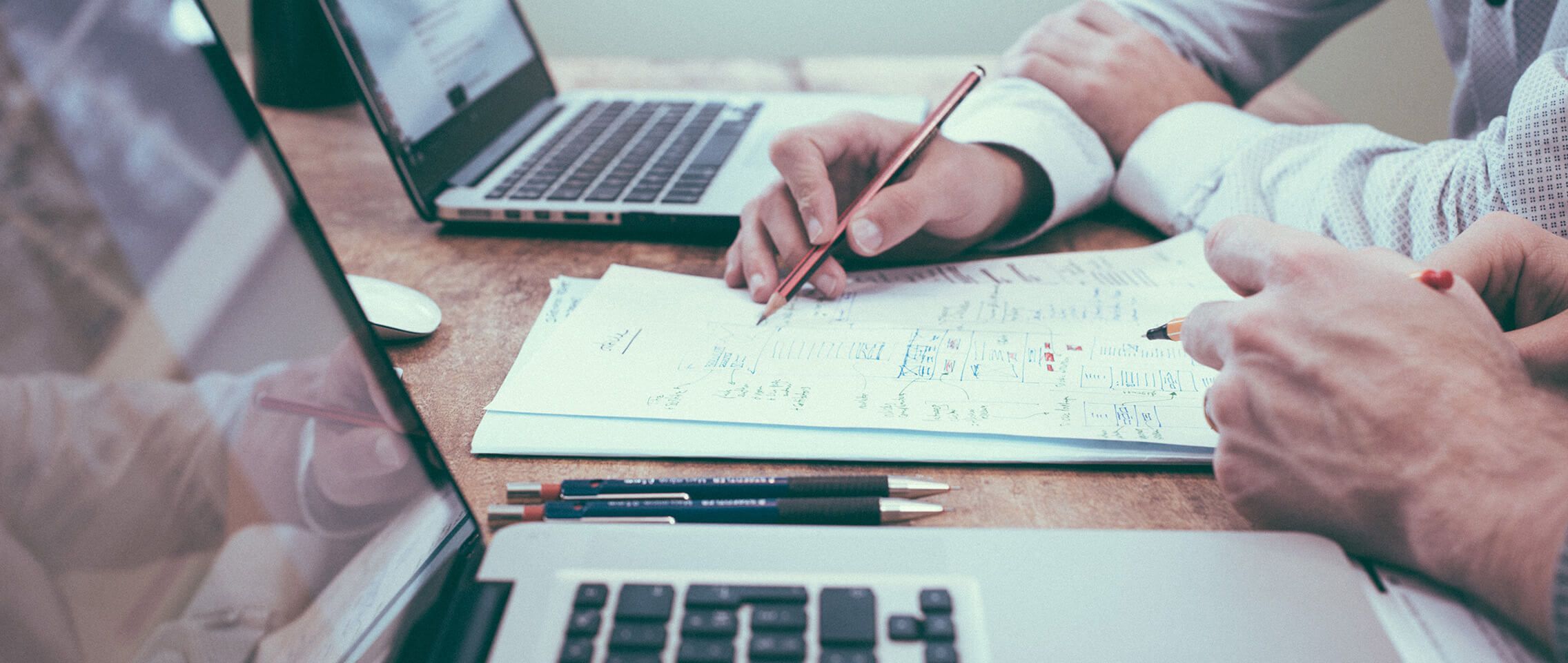
Material requirements planning (MRP) has been a mainstay of manufacturing long enough to pre-date almost everyone in the industry today. Experts spoke of its merits in think pieces dating back to the 1970s when it was rightfully viewed as a remarkable advancement in material and inventory management.
Many organizations still rely on MRP, which is an impressive feat for the legacy software. However, the increasing complexity of the global supply chain has revealed the limitations of decades-old MRP technology, costing manufacturers substantial revenue.
Fear not, for the upgrade to MRP has already arrived — in synchronized, adaptive, and autonomous advanced planning and scheduling (APS) systems.
Advanced planning and scheduling systems build on what made MRP integral to manufacturing in the first place but provide more robust solutions to the current supply chain problems plaguing manufacturers. Today’s manufacturing requires greater flexibility, visibility, and optimization than MRP systems can provide — capabilities the most robust modern solutions have in abundance.
MRP: How it works — and how it doesn’t
In pre-MRP times, the operative word in planning was “manual.” Planners logged existing inventory levels in spreadsheets and calculated raw material orders themselves. Teams placed orders to suppliers either by phone or through written purchase orders. Every step of the process required human input, which meant the entire system was highly prone to human error.
MRP systems rescued manufacturers from the cost of most of these manual mistakes. The software performs advanced calculations to ensure the right materials are available at the right times to produce finished products on schedule. An MRP system improves overall operational efficiency and profitability beyond what humans could accomplish with spreadsheets and calculators.
An MRP system improves overall operational efficiency and profitability beyond what humans could accomplish with spreadsheets and calculators.
MRP logic works backward from a finished goods production plan, using each item’s Bill of Material (BOM) to calculate raw material components. Companies typically derive product plans from a demand forecast, customer orders, or a combination of both with consideration for current stock-on-hand and safety stock requirements.
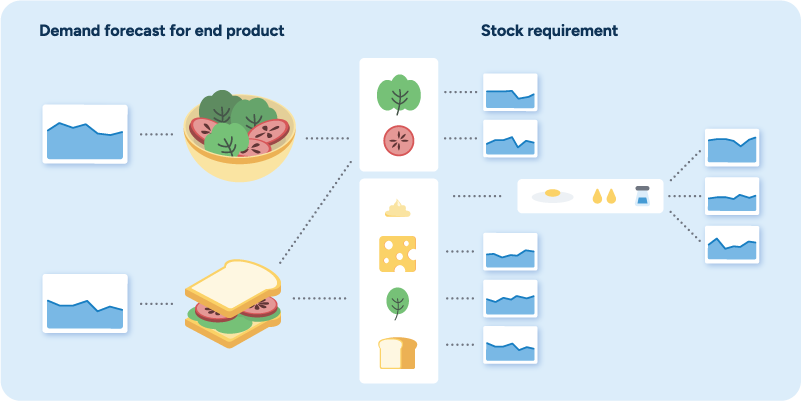
This logic functions well in two scenarios specifically:
- Where supply and demand are well-balanced over time.
- Where manufacturers have infinite short-term production capacity with raw materials readily available.
This situation is rarely the case for many industries, particularly food and beverage. Meat, poultry, and fish manufacturers are the least likely to be able to rely on MRP. Any number of variables can cause sudden demand shifts, including:
- Seasonality, like increased demand for ice cream in the summer.
- Business decisions such as promotions, especially those initiated with short notice to hit monthly or quarterly sales targets.
- Business constraints and challenges, like raw material scarcity, machine availability, and unexpected quality implications.
Supply chain teams often face both demand and supply fluctuations simultaneously. MRP handles the material breakdown without any problem, but the system falls short when it comes to determining what, when, and how much to produce due to factors like:
- An inability to work with finite capacity, as manufacturers plan production based on a fixed lead time.
- Limited cost implications of the plan with no considerations for aspects such as overtime costs, storage costs, and working capital.
- Physical space constraints that limit how many produced goods can be stored at any given time.
Supply and demand imbalances often result in supply chain teams extracting multiple data elements from their ERP and other sources into Excel to manually create a balanced plan. This exercise often mires teams in such labor-intensive tasks as calculation logic validation and input/output sense checking.
Frequently, a plan takes so long to generate and validate that supply and demand shift in the meantime, requiring work on a new plan to start immediately.
Unfortunately, the manual work doesn’t end with generating a plan. The team must also validate that the plan is the optimal one for the business, adding more work and time to the endeavor. Frequently, a plan takes so long to generate and validate that supply and demand shift in the meantime, requiring work on a new plan to start immediately. Supply chain teams end up knee-deep in the sort of manual work that MRP was supposed to minimize in the first place.
Advanced planning and scheduling solutions build and improve upon MRP
The high volume of manual work related to the MRP process is largely due to its step-based logic. The production of Item A requires Items B and C, which require Items D, E, F, and G. This logic works in simple situations, like when a company focuses on making a single product. The process starts to fall apart as manufacturers add further complexity to the system, like multiple product lines, real-time supply and demand updates, and specific production constraints.
Optimization solutions were developed to address these expanding layers of complexities. This includes advanced planning and scheduling (APS) solutions, which enhance traditional MRP by integrating more advanced algorithms to balance and handle multiple layers of production planning.
The most effective solutions cover three critical bases:
- Synchronized planning, which unifies decision-making across functions and planning layers.
- Adaptive planning, which aligns the entire business daily with constantly evolving market conditions.
- Autonomous planning, which automates decisions to enhance efficiency and drive profitability.
APS solutions with these three capabilities can generate a proposed plan based on MRP logic while considering all defined business rules and constraints simultaneously. The solution factors in these constraints automatically as part of a daily or weekly refresh.
Examples of applied constraints include:
- Maximum and minimum production capacity.
- Warehouse capacity.
- Distribution capacity.
- Minimum orders.
- Production quantities.
In addition to the above constraints, manufacturers may need to consider several business rules. Business rules are often more ambiguous than constraints and may include:
- The importance of Product A over Product B based on specific criteria.
- The importance of Customer C over Customer D based on particular criteria.
- A strong preference for working capital to not exceed a set amount of money.
Businesses can set these rules within a robust solution to create optimized plans in line with pre-defined business objectives. In most cases, this means optimizing for either profit maximization or cost-effectiveness. The rules only require a refresh when the overall business environment changes.
A spike in demand might cause an MRP system to create a plan beyond the production capabilities of a given site, whereas an optimized plan would know the finite limitations and work within them.
The ability to build plans within sets of constraints and rules comes in handy when demand needs outweigh supply realities. A spike in demand might cause an MRP system to create a plan beyond the production capabilities of a given site, whereas an optimized plan would know the finite limitations and work within them.
It wouldn’t be a stretch to initially imagine that an APS solution’s more advanced calculations would only compound a planning team’s workload. After all, MRP systems can’t handle more straightforward calculations without additional manual work.
Fortunately for planners, more advanced solutions automate and simplify a planner’s work in ways a simple MRP calculation could not. The solution automates data extraction, complex business rule application, and plan validation, automatically freeing up planners for the kinds of value-added tasks machines cannot perform.
Time can also be saved with real-time adjustments. When unexpected events such as machine breakdowns or changes in customer orders occur, the solution reevaluates and alters the schedule to meet the initial end date goal.
APS software facilitates an end-to-end integrated supply chain
Operational efficiency and profitability hinge on optimizing each part of the manufacturing process, so companies must look for holistic production planning and scheduling systems that address the supply chain. A synchronized, adaptive, and autonomous solution beats MRP when comparing production, scheduling, and purchase planning. Add distribution and demand planning into the mix, and the gap in capabilities between the two types of software becomes even more apparent.
Distribution planning
MRP has never quite been able to support distribution planning, while robust modern solutions can.
Companies can integrate supplementary systems or extensions like MRP II to tackle distribution planning. Still, optimization solutions have distribution planning capabilities out of the box, factoring in considerations ranging from shipping costs to customer preferences to help reduce lead times and costs within a company’s distribution network.
Unified planning
Perhaps the most significant advantage advanced planning and scheduling software has over MRP software is its connectivity. Teams working within a single solution use the same up-to-date data to make decisions, allowing them to make short- and long-term strategic decisions around the same information. Those without need multiple tools and integrations and, in reality, don’t manage to achieve the same levels of collaboration.
Complex challenges require advanced solutions
Advanced planning and scheduling solutions aren’t without their challenges. The solution is more complex than alternatives and often requires a certain level of configuration to fit a manufacturer’s unique needs and integrate with a manufacturer’s existing IT infrastructure. Overcoming these challenges requires an easily configurable solution that helps companies overcome these difficulties and quickly realize the value of their investment.
Thankfully, some providers on the market offer to share their wealth of experience to help mitigate these challenges. Easily configurable solutions can be delivered by themselves or a trusted partner network — especially one with an experienced track record of success like RELEX.
If years of volatile supply and demand, rising costs, and thinning margins have taught us anything, the supply chain is only growing more complex. Stay ahead of supply chain woes and prioritize long-term profitability with a synchronized, adaptive, and autonomous planning solution from the leaders in supply chain planning and optimization.