Unlock profitability with replenishment optimization
Aug 28, 2023 • 6 min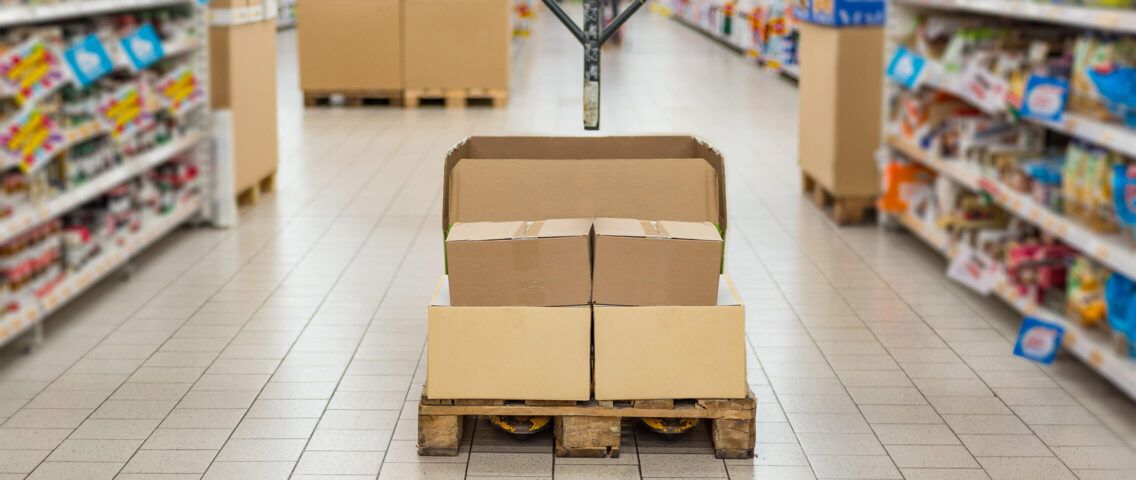
Store replenishment is often overlooked when speaking in retail operational terms. Higher-profile activities such as buying, merchandising, and marketing often overshadow replenishment, despite the latter’s major impact on profitability. Improved store-ordering accuracy and effectiveness have a major impact on sales through shelf availability and reduce handling, storage, and wastage costs in stores and other parts of the supply chain.
Accurate, item-level control is virtually unachievable with manual store ordering, which is why automated, system-assisted replenishment has become the default option for companies who are serious about replenishment optimization. The increasing popularity of auto-replenishment is largely due to the speed and ease with which retailers have achieved significant gains, often amounting to savings of several percentage points of total turnover.
Companies require automated replenishment to survive in an increasingly complex supply chain, which makes it essential for retailers to continually focus on replenishment optimization. Businesses that optimize their demand forecasting, inventory management, and order cycle and quantity setting will achieve better efficiency and higher accuracy in their replenishment processes — not to mention greater profitability.
The case for automated replenishment optimization
Replenishment optimization is the process of improving the accuracy and efficiency of a store’s replenishment operations to reduce costs and increase profitability. More and more frequently, this is achieved by combining advanced inventory and safety stock optimization with accurate forecasting procedures to balance inventory while maximizing sales.
Almost every company sees a return from optimizing their store replenishment processes within months, regardless of the types of products they sell. The more SKUs a company manages, the bigger the return they will see from getting the store replenishment process right. The benefits become more significant if a company carries thousands of products, and gains multiply further when there are several warehouses or stores to manage.
Automated replenishment improvements are especially beneficial for businesses where:
- Significant capital that could be better used elsewhere is tied up in excess inventory.
- On-shelf availability levels are unacceptably low (or aren’t measured), resulting in lost sales and lost customers.
- The total cost of product replenishment needs to be lower.
- Replenishment ordering or buying is decentralized and often handled by local managers.
Manual ordering is inevitably labor-intensive, costly, and simply impractical for the vast quantities of data to be analyzed effectively, resulting in errors and increased costs.
Companies that manage tens or hundreds of thousands of SKUs should use a replenishment system explicitly tailored to their operations to make automated replenishment more accurate, efficient, and cost-effective. Manual ordering in these situations is inevitably labor-intensive, costly, and simply impractical for the vast quantities of data that need to be analyzed effectively, resulting in errors and increased costs.
5 key benefits of automated replenishment optimization
The chief obstacle to embracing automated replenishment comes from the need to either adopt or upgrade to a robust replenishment platform capable of handling the task. Businesses may initially balk at the idea of adopting a new platform for several reasons:
- A fear of the cost of a brand-new platform.
- A preference for developing a platform in-house, despite the human and fiscal cost of development system maintenance.
- A hesitance to change to unknown tools from known tools, despite the limitations of the latter.
However, modern replenishment platforms are surprisingly easy to implement, especially when managed by an experienced software partner. Further, the financial benefits of optimized replenishment are so staggering that the cost savings of adopting a new platform often eclipses the initial investment within a matter of months.
The five key benefits of using a modern, automated replenishment optimization system are:
1. Reduced process costs
An automated replenishment system never stops working. It constantly monitors stock, sales, and demand. Human errors, such as forgetting to place an order, are eliminated. A sound replenishment system also automatically adjusts replenishment orders based on changes in forecasted demand, increasing service levels and sales while improving customer satisfaction.
2. Lower stock levels
A well-calibrated store replenishment system classifies products individually and assigns different attributes to them. This allows service level targets to be set higher for the products that customers consider most important and purchase most frequently. By using a system that recognizes sales frequency, profit margin, or sales value, a company can manage inventory to best ensure long-term profitability.
3. Improved inventory turnover
Because a replenishment system can manage safety stocks more accurately than any human buyer, it can also improve inventory turnover. If inventory management is done manually, it is impossible to evaluate the safety stock requirements of each SKU accurately. Instead, the items must be managed as groups, using basic rules of thumb.
4. Higher service levels
Any worthwhile store replenishment system will be able to calculate and set the safety stock level for each SKU separately to meet service level targets as efficiently as possible. This is achieved by factoring in the predictability of demand, delivery lead time, and delivery accuracy for each item. The greater degree of accuracy in inventory management offered by a good replenishment system makes it possible to simultaneously increase service levels and inventory turnover.
5. Enhanced exception management
A quality replenishment system will make the replenishment process more cost-effective. By automating stock level monitoring and routine replenishment orders, a considerable amount of management time can be redeployed to more challenging tasks such as assortment planning, supplier negotiations, sales support, exception management, and staff development.
A good replenishment system can also anticipate product shortages, late deliveries, seasonal products (where there’s a risk of excess stock), and other exceptions faster than any human. In many cases, the system can respond to the exceptions automatically and, in others, flag them to managers for expert attention.
The essential features of an automated replenishment system
Every company is different, and every company has a unique supply chain, cost structure, and management style. Replenishment systems need to fit the company rather than require the company to fit a preexisting system. Such systems must be customizable to support the specific features of each supply chain — and the system’s supplier must understand the customer’s business in all its complexity.
Replenishment systems need to fit the company rather than require the company to fit a preexisting system.
To ensure quick and meaningful results, an efficient replenishment system must also include features that:
- Automatically support demand forecasting at the SKU-store-day level and consider periodic or seasonal variations as well as trends and changes in demand.
- Calculate efficient safety stock levels at the SKU store-day level by considering the predictability of demand, delivery lead times, and delivery accuracy.
- Optimize cost-based order quantities and cycles at the supplier or product level.
- Combine automated routine orders with order suggestions for specific essential items, as well as automatic exception management.
Replenishment is inexorably tied to other supply chain planning functions, such as demand forecasting and inventory management. A worthwhile replenishment platform must also excel in these functions to help retailers create a holistic approach to supply chain management and improve processes across the board regardless of industry.
Take fresh products, which are notoriously tricky to manage. Even slight forecasting and replenishment imbalances can lead to costly food waste or disappointed customers. A sole focus on replenishment only deals with part of the equation, ultimately leaving the problem unsolved.
READ MORE: Why Ahold Delhaize selected RELEX to improve their forecasting and replenishment
Time is money — so save both with replenishment optimization
Store replenishment is an area where many retailers do not follow best practices. This is especially true in the realm of fresh food — something we’ve learned firsthand at RELEX from our years of experience helping retailers improve their replenishment processes. And while retailers may not be able to employ every best practice at all times, they should prioritize the most feasible and impactful development areas from the perspective of their business.
The fact is that a highly technical solution can evaluate your replenishment needs faster, more accurately, and more cost-effectively than a purchasing team can hope to do manually. Computers track data better than people, allowing those people to use their time solving other complex problems that computers can’t. Managers can be relieved from tasks like data crunching so they can use their expertise to support staff in their work and improve the business overall.