Digital twins in supply chain management: What companies often get wrong
Sep 6, 2024 • 9 min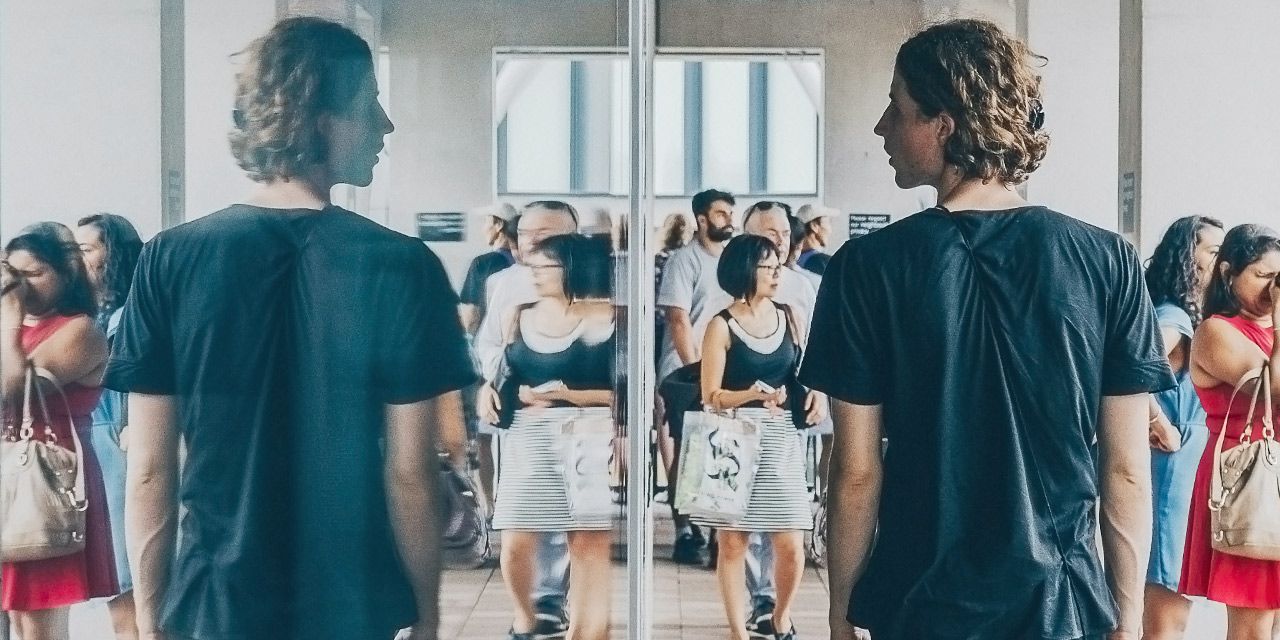
Digital twins are a transformative technology in supply chain management. This kind of modeling can significantly enhance operational efficiency by providing real-time visibility, optimizing inventory levels, and enabling predictive analytics.
But too often, organizations getting started with digital twins set themselves up for failure with misaligned expectations and a lack of support in the adoption process.
Organizations eager to stay agile in a dynamic market should set out to implement digital twin technology from the beginning to realize substantial cost savings, improved decision-making, and a more resilient supply chain.
The far-flung benefits of digital twins in supply chain management
Digital twins offer a significant leap in how consumer packaged goods companies manage their supply chain networks. By functioning as a form of AI, these virtual replicas of physical systems enable companies to test and ensure systems behave as expected using real-time data.
Despite the conceptual familiarity, the adoption of digital twins has been slow (and sometimes fraught with setbacks) due to initial implementation challenges, like unrealistic expectations, a lack of communication between teams, and data complexity.
Overcoming these hurdles is possible, and doing so unlocks critical advantages, reduces reliance on outdated institutional knowledge, and provides actionable insights.
Real-time visibility and predictive capabilities
Digital twin technology gives businesses a virtual, up-to-date overview of their supply chain. This snapshot enables quick, informed decision-making and agility in response to changing conditions.
Further enhancing this capability is the digital twin’s predictive analytics. By leveraging advanced data analysis, these systems anticipate future trends and potential disruptions and allow companies to proactively mitigate risks before they escalate.
Strategic scenario planning and operational efficiency
Because they can predict changes and disruptions, digital twins excel in facilitating detailed scenario planning. Whether anticipating demand shifts, supply chain disruptions, or customer response from new product introductions, digital twins can simulate various futures. As a result, businesses are better prepared to modify their strategies and operations effectively.
Whether anticipating demand shifts, supply chain disruptions, or customer response from new product introductions, digital twins can simulate various futures.
This foresight extends to identifying and addressing inefficiencies and bottlenecks to optimize supply chain processes. Consequently, brands using digital twins can achieve notable cost reductions, performance enhancements, and maintain optimal inventory levels, minimizing both excess and deficits.
Enhanced collaboration for continuous improvement
Another significant advantage of digital twins is the way they improve cross-departmental collaboration. A unified platform for data sharing allows different sectors of a company to synchronize their efforts, driving coherent, data-backed decision-making. This collaborative environment, supported by continuous monitoring and analysis, makes it easier for teams to keep improving supply chain management.
Common mistakes in adopting digital twin technology — and how to avoid them
You can’t afford to ignore digital twin technology. Even if your brand is managing without them for now, the sheer amount of data needed to manage supply chains and the rapid pace of change in customer demand necessitates the use of advanced tools.
One of the most common reasons for a brand to put off adopting digital twins to help them with supply chain management is anxiety about how complex it will be to implement the technology. Some companies have gone so far as to try digital twins once to address small issues, only to find the whole process too difficult for their team or not see the results they expected from their first attempt.
The good news is that you can avoid a bumpy onboarding process with the right approach.
Unrealistic expectations
A frequent stumbling block for companies is embarking on digital twin technology adoption without a solid foundation of understanding. Many teams rush into leveraging its potential without dedicating the necessary time to learn about its operational mechanics.
Digital twins offer exciting potential, particularly for areas like retail and CPG. But rushing into it often leads to misconceptions about what is and isn’t possible with supply chains and digital twin technology.
It’s common for brands to feel the need to frame the technology as a magical solution to sell it to executives. However, in practice adopting a digital twin tool into your workflow requires a methodical learning process. While digital twins can do incredible things for forecasting, it isn’t magic.
To mitigate this disconnect between expectation and reality, prioritizing a comprehensive grasp of the technology’s capabilities and mechanics is important. Recognizing that a thorough understanding of what is and isn’t possible with digital twins is essential sets the stage for effective application and integration into supply chain operations.
Communication gaps between departments
Another notable challenge in deploying digital twin technology within supply chain optimization is the disconnect between planning departments and IT teams. Effective communication and collaboration are essential to bridge this gap, helping these teams work in unison, supported by high-quality data and robust IT infrastructure.
Companies need a unified platform for data sharing and decision-making to better facilitate collaboration. Accuracy and consistency are vital in a digital twin model, meaning companies need to prioritize the implementation of strong data governance practices and investment in advanced IT infrastructure.
Companies need a unified platform for data sharing and decision-making to better facilitate collaboration.
Regular cross-functional meetings, joint planning sessions, and shared performance metrics will foster a collaborative culture and further enhance collaboration. Integrating advanced analytics and automation can streamline operations, too, reducing manual efforts and keeping the virtual model up to date. This integration drives better availability, lowers inventory levels, and leads to more efficient operations.
Underestimating data complexity
The role of data in digital twin implementation cannot be overstated. Particularly in industries like retail, wholesale, and CPG, the complexity and volume of data can present daunting challenges.
High-quality, accurately captured data forms the bedrock of any digital twin system. It enables the accurate reflection of real-world scenarios and aids in the testing of “what if” situations, such as the impact of setting up a new warehouse.
Therefore, ensuring data integrity and quality is paramount, as it directly influences the system’s accuracy and reliability. The quality of your data will directly relate to the quality of your digital twin and how well it can forecast for you.
Neglecting knowledge translation and data ownership
An essential step in digital twin projects is translating planning knowledge and insights into actionable data and rules. This process requires a collaborative effort to ensure the digital twin accurately encapsulates operational knowledge and expertise.
Clear ownership of both the data and the solution helps steer the project away from common pitfalls, such as data mismanagement or striving for unattainable perfection. Assigning dedicated personnel to oversee data management and project direction is essential for maintaining focus and achieving success.
Overlooking the importance of incremental improvement
Digital systems, by their nature, evolve through continuous validation and refinement. Accepting that perfection is a journey, not a starting point, encourages a mindset geared towards improvement and adaptability.
Perfection is an evolving target, and steady, incremental enhancements pave the way for achieving operational excellence through digital twin technology.
The journey toward successful digital twin implementation is marked by incremental improvement. Embracing a realistic goal for accuracy—acknowledging that some manual adjustments will always be necessary—sets a pragmatic foundation for progress. Perfection is an evolving target, and steady, incremental enhancements pave the way for achieving operational excellence through digital twin technology.
Companies can address these areas with a strategic and well-informed approach to leverage digital twin technology effectively, unlocking new levels of efficiency and innovation in their supply chain management. This journey, while complex, offers substantial rewards for those prepared to navigate its challenges with foresight and commitment.
We’ve been using digital twins for years
RELEX has been at the forefront of leveraging advanced technologies to optimize supply chain management. One of the key innovations in our approach is the use of digital twins. With a proven track record, RELEX has been implementing digital twin technology for several years, consistently delivering measurable value to our clients.
Digital twins in CPG
In CPG, digital twins often focus on the manufacturing process, supply chain optimization, and product lifecycle management. CPG brands have to make sure they’re using labor and materials efficiently. At the same time, CPG brands often have to manage demand across several sales channels at once.
In manufacturing, we aim to generate manufacturer orders as close to perfect as possible so that the planner can spend less time creating the plan and more time analyzing. To create this perfect plan, though, we need to build a framework or model of their reality – That’s where digital twins come in.
With digital twin technology, it’s possible to simulate production lines, accurately predict customer needs (through demand sensing), and even influence the market (with demand shaping).
Digital twins in wholesale
Wholesale brands must manage large lot sizes and many different customers, so their biggest challenges are often around preventing waste (especially from spoilage of fresh products) and improving their order fulfillment process so they can get deliveries to their customers in a timely manner.
In wholesale, digital twins are often used to simulate warehouse operations and optimize inventory levels.
Digital twins in retail
For retail, though, digital twins are more focused on store operations, customer experience, and inventory management. They simulate store layouts, optimize product placement, and improve customer experience by understanding customer preferences.
At RELEX, our collaborative approach aligns digital twins with the unique operational realities of our customers. Involving customers in the development and validation process results in high accuracy and functionality so that digital twins can meet their specific needs and challenges.
We also understand the importance of high data quality. Effective communication between planners and IT teams is crucial to overcoming common implementation challenges. By maintaining high data quality standards, we ensure that our digital twins provide reliable and actionable insights.
How RELEX uses digital twin modeling
At RELEX, digital twins are integral to enhancing forecasting and replenishment, optimizing inventory, and improving supply chain visibility. Digital twins simulate scenarios and provide real-time analytics to enable precise demand forecasting, efficient inventory management, and proactive decision-making. This technology maintains optimal stock levels, streamlines processes, and fosters collaboration across supply chains.
- Forecasting and replenishment (F&R): Digital twins play a crucial role in creating accurate demand forecasts and optimizing replenishment processes. By simulating various scenarios and predicting future trends, digital twins help us ensure that our clients have the right products in the right place at the right time.
- Scenario planning: Digital twins enable companies to simulate different scenarios, such as any shifts in demand or supply disruptions. This allows for better planning and decision-making, helping our clients stay ahead of potential challenges.
- Inventory optimization: With real-time visibility and predictive analytics, digital twins help maintain optimal inventory levels. This reduces holding costs and prevents stockouts, ensuring that our clients can meet customer demand without overstocking.
- Supply chain visibility: Digital twins offer a comprehensive, real-time view of the supply chain, including inventory, production, and logistics. This visibility helps in making informed decisions quickly, improving overall supply chain efficiency.
- Process optimization: By identifying inefficiencies and bottlenecks in the supply chain, digital twins suggest optimal solutions to improve overall performance and reduce costs. This continuous optimization ensures that our customers’ supply chains are always operating at peak efficiency.
- Collaboration and continuous improvement: Digital twins provide a common platform for different departments to share information and collaborate. This ensures coordinated decisions and continuous improvement in supply chain operations, improving collaboration as well as innovation.
A real-world example of supply chain optimization using digital twin technology
The Vita Coco Company is the world’s largest brand of coconut and plant waters, operating in 31 countries with an annual turnover of $428 million in 2022. Vita Coco relies on an asset-light supply chain, partnering with coconut processors and local co-packers across Asia and South America.
However, managing a supply chain spanning 15 factories and 20+ market warehouses was complex. Synchronizing a global supply chain requires an integrated planning solution capable of true optimization. Vita Coco needed a system to model and optimize their entire supply chain to maximize profitability.
The company turned to RELEX for advanced supply chain planning. The team built a digital twin of Vita Coco’s supply chain within the RELEX platform. This digital twin captured every node, cost, rule, and constraint, transforming the planning puzzle into a mathematical problem. The model considered varying costs, lead times, capacity constraints, and minimum order volumes to determine the most profitable sourcing plan.
The digital twin also integrated shipping costs and import duties, allowing the logistics department to work from planned container requirements when negotiating with logistics brokers. This comprehensive approach enabled Vita Coco to convert its demand forecast into a fully optimized 18-month supply plan, guiding production scheduling, packaging material requirements, logistics operations, and inventory management.
Results: The implementation of RELEX digital twin technology led to significant strategic gains for Vita Coco:
- Cost reductions: The optimized plans unlocked millions of dollars in cost of goods value through better sourcing and distribution planning.
- Improved business planning process: The integrated, optimized supply plan provided a common basis for the sales and operations planning (S&OP) cycle, enhancing efficiency and focus in discussions.
- Enhanced decision support: The ability to simulate various business scenarios improved financial planning and budgeting processes.
The future of digital twins in integrated business planning (IBP)
Advancements in AI and digital twin technology are already revolutionizing supply chain management within integrated business planning (IBP), and this is just the beginning. AI can automate data mapping, reducing manual work and improving accuracy.
As new technologies emerge, AI will enable supply chain digital twins to expand their capabilities and enhance precision. These innovations will foster collaboration, support continuous improvement, and ensure supply chain plans are accurate, feasible, and aligned with strategic goals.
Looking ahead, the integration of AI and digital twins will lead to better decision-making, enhanced efficiency, and more resilient supply chain operations, positioning organizations to thrive in an increasingly complex and dynamic market.