How strategic distribution planning enhances supply chain optimization
Sep 30, 2024 • 10 min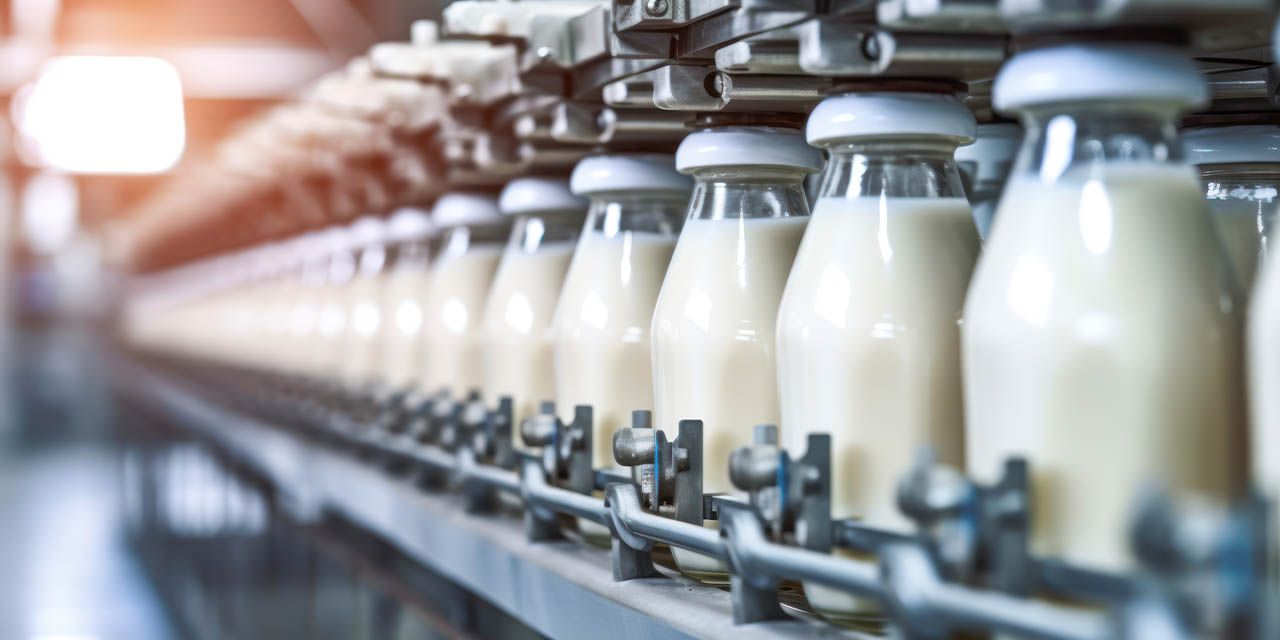
Distribution planning is challenging, especially in the consumer-packaged goods (CPG) and manufacturing industries. It requires companies to synchronize production, inventory levels, transportation capacities, and fluctuating customer demand while often relying on scattered data and manual processes.
Imagine a multi-billion-dollar CPG and manufacturing company with dozens of brands with global reach. The company requires a vast and intricate distribution network to reach each of those products’ diverse markets. Coordinating the distribution of multiple products, all with different requirements and constraints, requires careful and considered planning.
Planning distribution for dozens of products globally with an oversized Excel sheet would be like climbing Mt. Everest with only a hand-held compass to guide you. Solutions utilizing machine learning help planners by providing highly accurate demand forecasts and optimizing inventory levels, transportation routes, and replenishment schedules, enhancing efficiency and reducing costs.
Distribution planning solutions that utilize heuristics and mathematical optimization are the equivalent of climbing Mt. Everest with a sherpa and the latest available technology. They keep you on track, on time, and able to conquer the task.
What is distribution planning?
Distribution planning manages the movement of goods from production sites or suppliers to customers efficiently and cost-effectively and ensures products are delivered on time and in the right amounts precisely where they’re needed. Demand and inventory planning are used to support distribution planning.
Successful distribution planning requires that it be in good alignment with production plans. It can optimize inventory levels, reduce transportation costs by moving products efficiently and cost-effectively, and enhance customer satisfaction by ensuring timely and accurate deliveries.
CPG and manufacturing companies with complex distribution networks face unique challenges with distribution planning, demand variability, short product life cycles, and regulatory compliance for product safety and quality. They need to react quickly to demand changes and issues such as transportation issues or receiving large new orders.
Distribution planners need to know if they have the excess capacity available and if it can be promised to customers for delivery by a specific date, also known as Available-to-Promise (ATP).
ATP calculations consider current inventory levels, incoming shipments, and existing customer orders to determine how much product can be committed to new orders without affecting previously made commitments. This ensures customer orders are fulfilled accurately and on time, optimizing inventory utilization and improving customer satisfaction.
Because distribution planning directly impacts a company’s operational efficiency, customer satisfaction, and overall profitability, it’s crucial to get it right.
The benefits of optimal distribution planning
A robust and efficient distribution planning system leverages real-time data and advanced technology to coordinate all supply chain activities, minimizing costs and maximizing resource utilization.
Optimal distribution planning facilitates proactive planning and response to demand fluctuations.
Demand sensing impacts distribution planning by providing real-time insights into demand fluctuations. This allows for more accurate and responsive adjustments to inventory levels and delivery schedules, leading to improved efficiency, reduced stockouts, and better alignment with actual market conditions.
The benefits of optimal distribution planning include:
- Cost reduction
Companies can minimize inventory holding costs by maintaining optimal stock levels and reducing excess inventory. Refined transportation routes and load ties reduce transportation and fuel costs. - Improved customer satisfaction
Optimized planning reduces order lead times and minimizes backorders, leading to better service levels. Satisfaction is enhanced by timely and accurate deliveries that meet customer expectations. - Enhanced operational efficiency
Streamlining the movement of goods, reducing transportation and warehousing costs, and minimizing delays all enhance operational efficiency. Accurate inventory levels reduce the need for excess stock and prevent stockouts, which leads to smoother operations and better resource utilization. - Risk mitigation
Anticipate and address potential disruptions in the supply chain, such as delays, stockouts, demand spikes, or excess inventory. By accurately forecasting demand and optimizing inventory and transportation, companies can better prepare for uncertainties, ensuring continuity of supply and minimizing the impact of unforeseen events. - Increased sales and revenue
By ensuring product availability and timely deliveries, optimal distribution planning can help increase sales and revenue while supporting promotional activities and new product launches by aligning inventory and distribution strategies with market demand. - Sustainability
Reduce environmental impact by streamlining transportation routes and minimizing waste due to spoilage or obsolescence and support sustainability initiatives by improving resource utilization and reducing emissions.
Overall, optimal distribution planning streamlines operations, improves inventory turnover, and supports data-driven decision-making, leading to increased efficiency. So why do distribution planners find distribution planning so challenging?

10 challenges to distribution planning
Planning distribution may sound straightforward, but as the size of your business and network grows in complexity, so does the difficulty. With so many locations to plan for, products on the market, and changes and disruptions in the supply chain that require reaction, the customers of CPG and manufacturing companies face a variety of challenges.
- Demand variability
Knowing the type of demand—whether it’s stable, seasonal, promotional, or erratic—allows distribution planning to be more precise and effective. It helps in tailoring inventory levels, optimizing transportation schedules, and aligning warehousing strategies to meet specific demand patterns, thereby reducing costs, minimizing stockouts, and improving overall service levels. Most companies do demand propagation to understand the demand on manufacturing sites or suppliers, but do they know what kind of demand it is? - Inventory management
Balancing inventory levels to avoid both stockouts and excess inventory requires precise planning and real-time data. - Transportation optimization
Selecting the most efficient and cost-effective transportation modes and routes while managing fuel costs and delivery windows is complex. - Complex supply chains
Coordinating multiple suppliers, production facilities, warehouses, and distribution centers adds layers of complexity. - Regulatory compliance
Adhering to various regulations related to product safety, quality, and traceability can complicate distribution planning and execution. - Real-time data and visibility
Accessing and integrating real-time data from various parts of the supply chain is essential for effective planning. - Coordination across functions
Ensuring alignment between procurement, production, sales, and logistics functions is crucial but often difficult. - Scenario planning and risk management
Evaluating the impact of various factors (e.g., supply disruptions, demand spikes) on the distribution plan and developing contingency plans is complex. - Sustainability goals
Balancing operational efficiency with sustainability initiatives, such as reducing emissions and waste, adds another layer of complexity. - Technology integration
Implementing and integrating advanced planning tools and technologies, such as machine learning and real-time analytics, is necessary for complex CPG distribution planning.
Distribution planning is especially challenging for CPG and manufacturing companies due to their complex supply chains.
Why distribution planning is critical to CPG and manufacturing companies
CPG and manufacturers face significant fluctuations in demand due to seasonality, promotions, and market trends. They must be able to quickly respond to market changes, such as new product launches or competitive actions.
Many CPG products, especially perishable goods, have short shelf lives. Accurate distribution planning helps to manage these variations so that products are available when and where they are needed and reduces waste and spoilage.
Supply chains for CPG and manufacturers are complex and multi-echelon, including suppliers, manufacturing sites, distribution centers, and retailers. Each echelon represents a different stage in the supply chain, and effective coordination among these layers is crucial for optimizing inventory levels, reducing lead times, and ensuring smooth product flow from production to the end customer. Consumers and customers expect high service levels, including on-time, in-full (OTIF) deliveries.
CPG products must often comply with various safety, quality, and traceability regulations. They need to ensure compliance by maintaining accurate records and managing product flows effectively.
Transportation costs are also a considerable factor for CPG and manufacturing companies. Managing distribution routes, load capacities, and inventory levels can reduce these costs. The ability to drill deeper into the individual modes of transportation, such as which trucks and containers will be used, along with their sizes and capacities, allows for optimization by mode of transportation and distribution lane.
Many CPG and manufacturing companies are focused on reducing their environmental impact and want to minimize transportation emissions and waste to support their sustainability initiatives.
To learn more about how retail, CPG and manufacturing executives are tackling these challenges and supply chain planning for the future, read The State of Supply Chain 2024 report.
Essential features for optimized distribution planning
CPG and manufacturing companies need an optimized distribution planning solution to synchronize the flow of goods from production facilities to local warehouses and distribution centers. Ideally, the solution should include three main features.
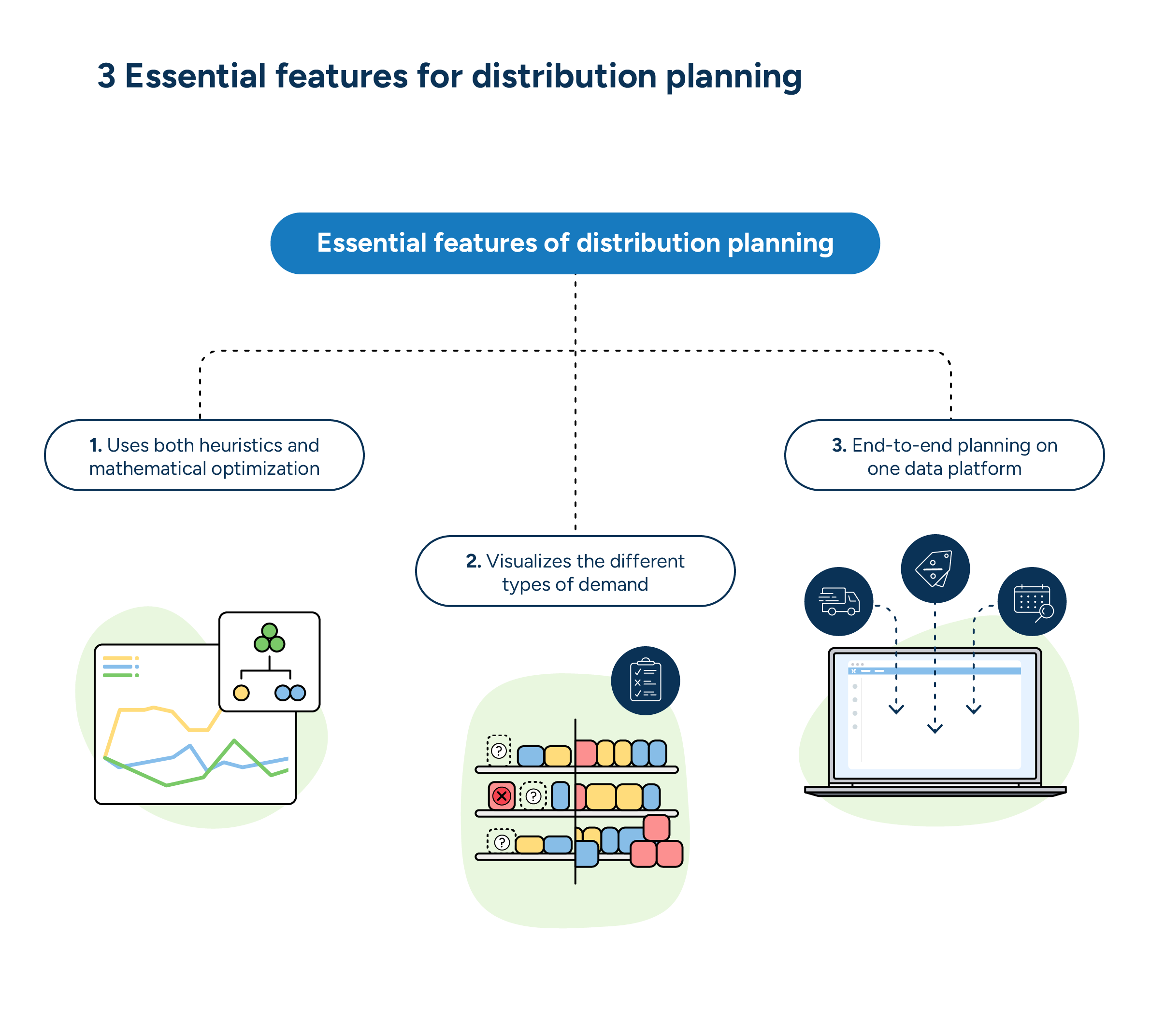
1. Utilize both heuristics and mathematical optimization
Optimized distribution planning in the complex world of CPG and manufacturing should use heuristics and mathematical optimization together.
Heuristics in distribution planning are used to quickly generate practical solutions for complex problems when exact methods are too slow or infeasible. They provide approximate solutions by simplifying the problem, often through rules of thumb or educated guesses. For example, heuristics might be used to determine the best delivery routes, allocate inventory across multiple locations, or prioritize orders, enabling faster decision-making and operational efficiency. The proposed solutions might not be ideal in terms of overall logistics or other complex requirements, but they may be a necessary compromise. Sometimes, it is worth the effort to squeeze out the last bits of optimization, especially for large corporations as the absolute savings value could still be significant. This is where mathematical optimization comes in.
Mathematical optimization in distribution planning creates highly efficient and cost-effective distribution strategies. It uses advanced algorithms to balance demand and supply, considering various constraints such as production plans, supplier schedules, and order limits. It also optimizes transportation routes, inventory levels, and delivery schedules to ensure that goods are delivered on time and in the right quantities, minimizing costs and maximizing resource utilization. Also important is the ability to optimize distribution planning by mode of transportation and distribution lane. This approach allows for precise, data-driven decision-making that enhances overall supply chain performance.
READ MORE: Supply chain optimization for manufacturers: It’s mathematics, not magic.
2. Visualize the different types of demand
With the propagation of demand, companies can visualize changes in consumer demand that affect various stages of the supply chain. This process collects demand data from different sources, including orders, forecasts, and safety stock, impacting inventory levels, production schedules, and replenishment.
Effective demand propagation ensures that all parts of the supply chain are aligned and responsive to actual market conditions, helping to maintain optimal inventory levels and efficiently meet customer needs.
Knowing the different types of demand and real orders versus production for safety stock is a real asset. It’s crucial to see and understand which demand the planner is asking the plant to produce.
3. Create end-to-end planning all on one data platform
Traditionally, a company may have their demand planning, master planning (which includes production planning and purchase planning), and distribution planning, all as different solutions on separate data platforms. Having all these planning solutions exist on one data platform offers several critical benefits:
- Integrated data and visibility: A unified platform provides a single source of truth, ensuring that all planning functions use consistent and up-to-date data, which enhances visibility across the entire supply chain.
- Improved coordination and efficiency: Seamless integration between different planning processes allows for better coordination, reducing silos and enabling more efficient and synchronized operations.
- Enhanced responsiveness: Real-time data sharing and advanced analytics enable quicker and more informed decision-making, allowing the supply chain to respond swiftly to changes in demand and supply conditions.
- Cost savings: Optimizing all planning functions on a single platform helps reduce redundancies, lower operational costs, and improve resource utilization.
- Reduce stockouts and excess inventory: Combining demand, master, and distribution planning improves forecast accuracy and alignment, leading to more precise inventory management and reduced stockouts or excess inventory.
Overall, end-to-end planning on one unified platform drives greater efficiency, agility, and cost-effectiveness in the supply chain. RELEX distribution planning seamlessly integrates and optimizes the entire supply chain on one data platform, ensuring timely and cost-effective deliveries through advanced, real-time data analytics and automation.
WATCH: End-to-end supply chain planning for CPG
Real-world results: Vita Coco – Optimizing Vita Coco’s global operations
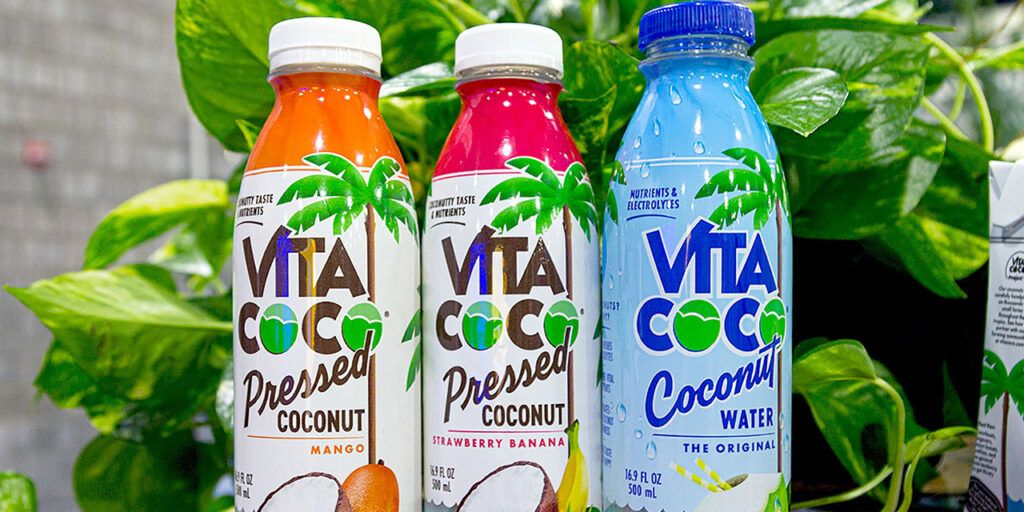
Since its foundation, The Vita Coco Company has seen exceptional growth. With operations in 31 countries and an annual turnover of 428 MUSD (2022), Vita Coco is today the world’s largest brand in coconut & plant waters.
Synchronizing a supply chain spanning 15 factories (and growing) and 20+ market warehouses on several continents servicing every major customer in the US and Europe is challenging. Jonathan Burth, COO of The Vita Coco Company, says, “Finding the right vendor was crucial. We needed an integrated planning solution capable of modeling and optimizing our entire supply chain. With so many nodes, constraints, and alternative supply routes, the only way to maximize profitability is by using true optimization technology. This is exactly what RELEX offers.”
The ability to create optimized plans that consider costs, real-world constraints, and business preferences has led to significant cost reductions at Vita Coco. Burth confirms this, saying, “RELEX has helped us to unlock millions of dollars in cost of goods value, mainly owing to better sourcing and distribution planning.”
Creating an optimized end-to-end planning process
Creating an end-to-end CPG and manufacturing planning process means having comprehensive visibility and coordination across the entire supply chain, from demand forecasting to production and distribution. This leads to improved efficiency, reduced costs, and enhanced responsiveness to market changes. This ultimately leads to better customer satisfaction and increased profitability.
Optimized distribution planning improves collaboration across functions, supports data-driven decision-making, and helps mitigate risks, ultimately enhancing customer satisfaction and scalability.
Learn more about how to gain real-time visibility into inventory and supply chain operations with RELEX distribution planning as part of an end-to-end process. Increase efficiency by automating routine tasks using advanced analytics and automated planning capabilities.