Fresh forecasting & replenishment: Master spoilage
Nov 27, 2024 • 6 min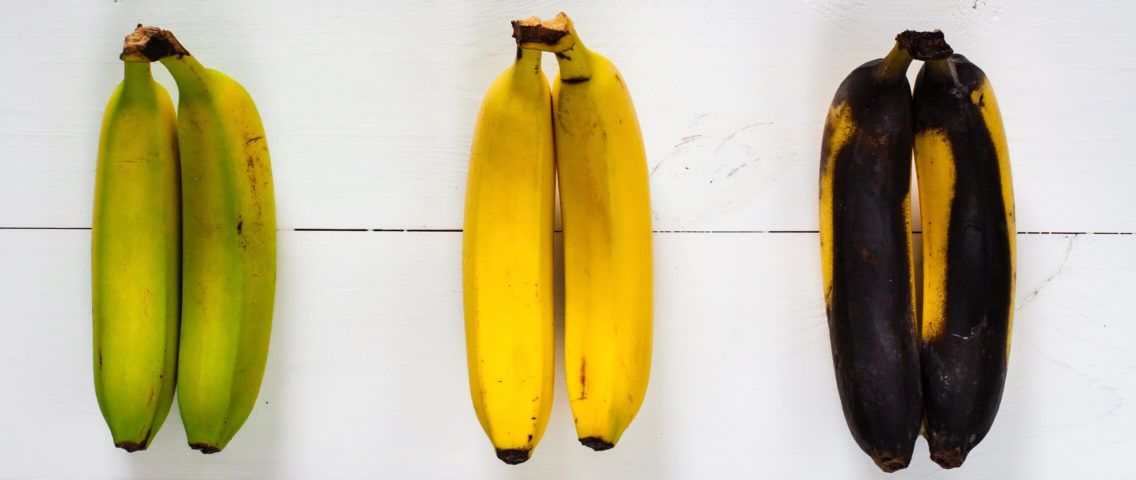
Did you know that about one-third of food goes bad before it’s eaten? All that spoilage is a waste of both money and produce. But with sophisticated supply chain technology and the right approach, you can significantly reduce fresh overstock and prevent waste.
Addressing this issue is crucial for environmental sustainability as well as improving the efficiency of food distribution networks worldwide. By integrating advanced technologies and innovative strategies into our supply chains, we can improve industry margins while preventing carbon emissions.
Ready to make a positive change for the planet and your bottom line? Here are five practical ways to prevent food waste with forecasting and replenishment.
1. Increase demand forecasting accuracy
With specialized AI, retailers can get advanced demand forecasting that accurately predicts sales. So, you have exactly the products your customers want at the right time—no more, no less.
Combine historical data with seasonal and promotional factors
Historical sales data provides a solid foundation for understanding demand patterns, seasonal shifts, and local or regional impacts that can indicate future trends.
But historical data isn’t enough on its own. It’s also important to incorporate external factors like weather and local events to account for variables that can significantly impact demand but are not captured in historical sales alone. For example, a sudden cold snap can increase the demand for fresh herbs (as more customers start cooking hot soups and stews), while a sudden heat wave will likely result in a run on melons, berries, and lettuce.
READ MORE: How to tackle the causes of grocery store food waste
Seasonal trends and promotional activities can also cause significant fluctuations in demand and must be considered in the forecast to align inventory levels with expected demand.
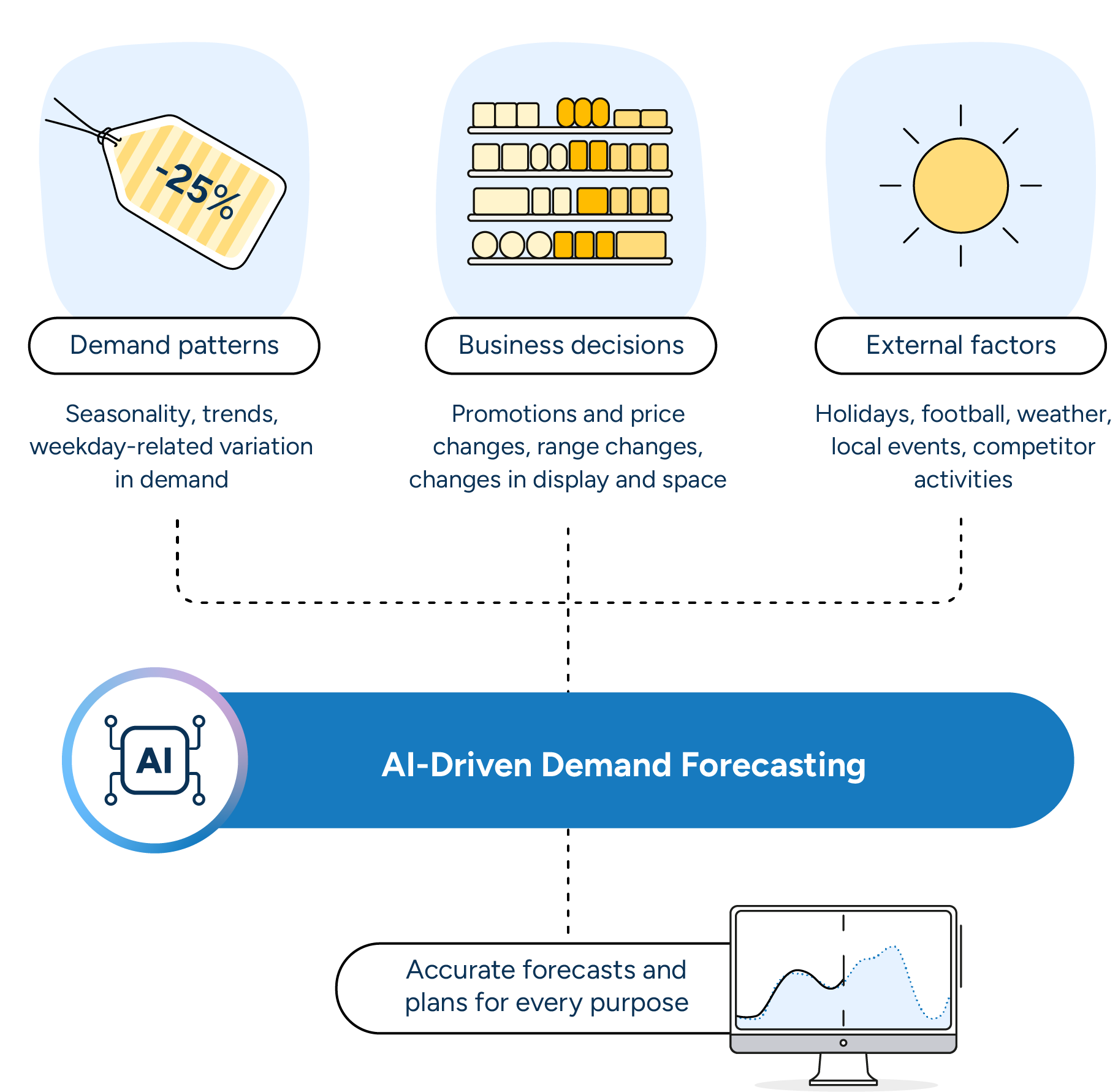
Regularly review and adjust forecasting models
Remember that improving forecasting accuracy is not a one-time activity. Regularly reviewing and adjusting forecasting models helps to incorporate new data and insights, enhancing their accuracy over time. Using KPIs to measure forecast performance provides a quantitative basis for evaluating the forecasting process’s effectiveness and identifying improvement areas. This feedback loop is crucial for refining methodologies and making informed decisions.
Share forecast data with suppliers
Collaboration with suppliers is essential for a responsive and efficient supply chain. Sharing forecast data enables suppliers to understand your demand patterns and prepare accordingly, reducing the risk of supply disruptions. By working together to adjust lead times and order quantities, both parties can respond more flexibly to changes in demand, ensuring that inventory levels are optimized and customer needs are met.
2. Balance replenishment
Implementing replenishment solutions that balance the risk of stock-outs and spoilage is crucial for maintaining optimal inventory levels and store operations efficiency.
- Integrate your replenishment systems with your existing inventory management software to adjust order quantities based on real-time data, keep your stock levels aligned with current demand, and minimize the risk of overstocking and stock-outs.
- Use adaptive order parameters that change dynamically to account for fluctuations in demand patterns and the varying shelf life of different products. Continuously adjusting these parameters keeps inventory levels optimized, reducing waste and improving product availability.)
- Implement delivery flow smoothing so products arrive at an even pace throughout the week. Smoothing replenishment helps store associates keep up with customer demand efficiently without becoming overwhelmed at peak times.
How and when you replenish products can significantly affect the amount of waste you produce. Transform replenishment from a routine task to a competitive advantage while cutting your spoilage rates.
3. Integrate planning processes
A unified platform integrates planning processes, tools, and data across stores and distribution centers (DCs). Sharing real-time data throughout the supply chain provides exceptional visibility for more accurate forecasts. This increased visibility allows for rapid responses to changes in demand and supply conditions, as well as the capability to plan for the long term.
While a unified approach fosters visibility and collaboration, it doesn’t eliminate the need to manually check in with other departments. Regular cross-departmental check-ins are still necessary to discuss inventory and demand planning.
Integrated planning enables you to standardize your processes by developing consistent methods for inventory management, demand forecasting, and replenishment. Once these processes are in place, you’ll need to review performance data and feedback regularly and adjust your planning processes accordingly. And not just once – to remain effective and responsive to changing conditions, be sure to maintain a continuous improvement program to identify and address inefficiencies as they arise.
4. Track inventory on a batch level
Effective batch management is crucial in grocery to ensure product freshness and minimize spoilage. By tracking inventory on a batch level, you can monitor expiration dates and manage product transformations, maintaining the highest quality of products for your customers.
Monitor fresh products with expiration date tracking systems
Expiration date tracking systems alert staff when products are nearing expiration dates, ensuring that products are either sold before they spoil or appropriately marked down to encourage quick sales. Integrating these technologies with your inventory management system streamlines operations and reduces manual errors.
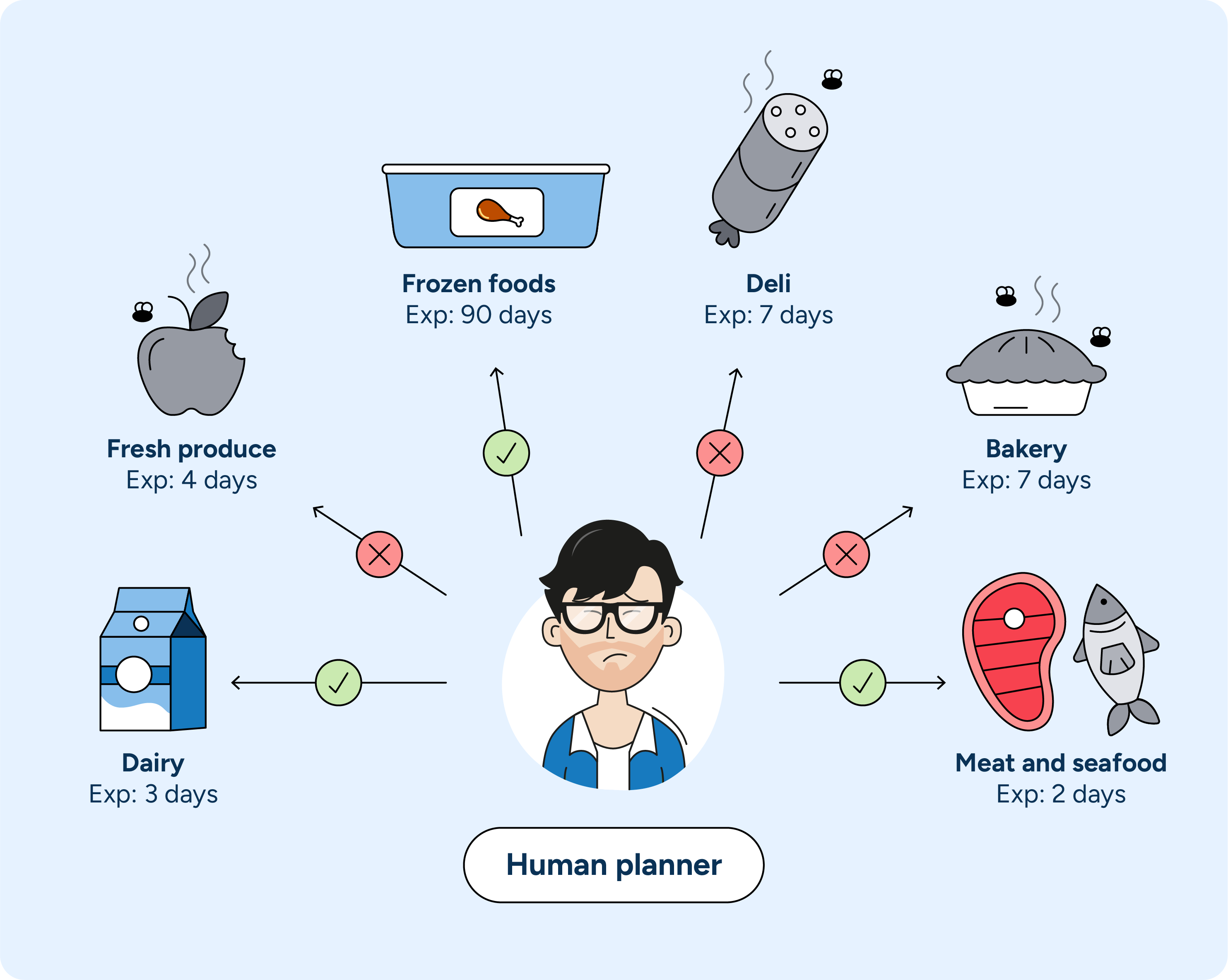
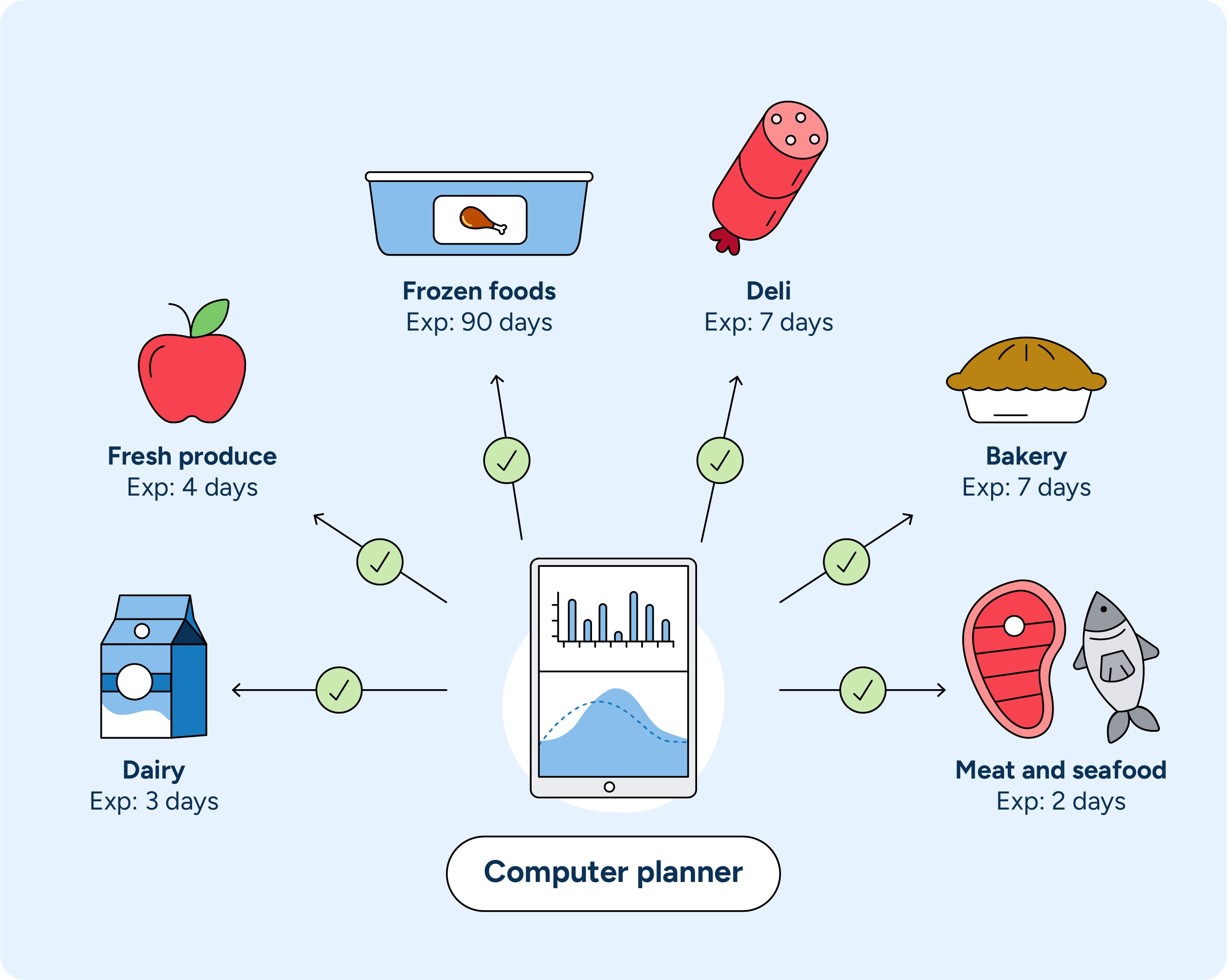
Analyze batch data for continuous improvement
Regularly analyzing batch data identifies trends and patterns in spoilage, helping you adjust ordering practices and inventory levels to better match demand. This data enables you to optimize inventory levels to always have enough stock to meet customer needs without overstocking. Batch-level stocking enables first-in, first-out (FIFO) inventory management practices (our next recommendation) because it offers clear visibility into what’s already come in and what’s coming next.
Implement FIFO inventory management practices
If you haven’t already, it’s time to implement FIFO. This method sells older stock before newer stock, reducing the likelihood of products expiring on the shelf. By consistently rotating stock, you can ensure that customers receive the freshest products possible.
5. Implement exception-based management
You can implement automated systems for everything from inventory tracking to ordering to replenishment. Automating daily tasks frees up employees for more value-added activities, such as maintaining product freshness. Automation allows your team to focus on managing exceptions and disruptions more effectively so any issues can be addressed and resolved promptly.
The next step is to prioritize exception management by establishing alerts for potential problems, such as stock-outs or overstock situations. Additionally, optimizing labor usage by integrating workforce planning, especially during peak hours, helps ensure product quality and minimize spoilage. Labor management systems can help schedule staff based on demand forecasts, ensuring you have the right coverage.
You’ll also need to provide ongoing training for employees on exception-based management practices and make necessary adjustments as needed. Use performance data to identify areas for improvement and implement changes.
Harnessing AI for a sustainable future in grocery retail
As we move forward, adopting AI to improve sustainability will undoubtedly become more common, setting a new standard for the grocery industry. The transformative impact of these technologies offers a glimpse into a future where grocery retailers not only thrive economically but also serve as pillars of sustainability within their communities. The path forward is clear: by embracing smart decision-making and specialized AI, grocery retailers can lead the charge towards a more sustainable, waste-free world.