How to maximize store operational efficiency with a clever supply chain planning solution
Jan 16, 2023 • 4 min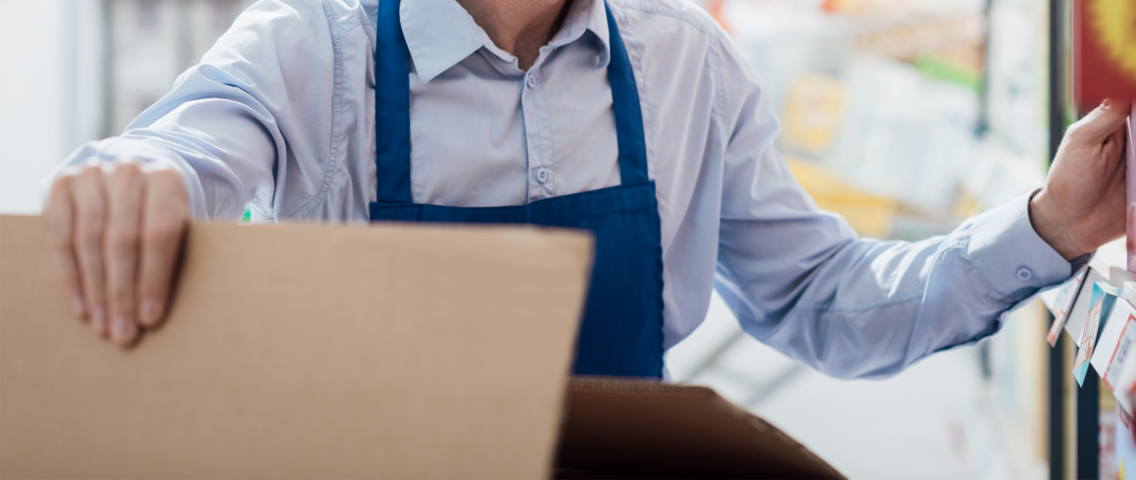
Store operations are the heart and soul of any retail business. The interactions that happen at the edge of retail between customers and staff are crucial to the health of a positively functioning business.
While an end-to-end supply chain system provides the boundaries that retail operations must play within, how store personnel manage the flow of stock and data through stores dictates the operational heartbeat of a company. The importance of retail operations personnel should make them a key influencer in evaluating and selecting a supply chain solution. Unfortunately, we often do not hear their voices at the decision table.
Luckily seeing the benefits of an effective supply chain solution on store operations can be the first step in empowering retail leaders to vocalize their need for a solution that benefits them, their stores, and their personnel.
Ensuring the correct assortment
Well-stocked shelves are crucial for an optimal customer experience—but they’re also one of the main sources of workload for store employees. That’s why ensuring that the right stock is in the right place is essential for efficient store operations.
A solution that takes advantage of forecasting data can help retailers decide the correct inventory needs for each store based on external factors and regional demand. As all store colleagues know, dealing with an overabundance of stock can have a spiral effect on workload, so optimal stock levels are key to workload balance.
Forecasting data can determine how much inventory is needed in-store and how much to save for online orders based on evolving customer buying habits. These estimations allow retailers to make a virtual ring-fence around products reserved for online sales while ensuring enough for those customers who prefer in-store shopping. The operations team is saved from having to make these time-consuming inventory decisions while still having the flexibility to change stock allocations if needed.
Demand data can estimate how many store personnel are needed based on predicted customer flow, the amount of new inventory coming in, and what stock needs to be moved onto the floor for the day. This insight can be a relief for operations leaders who would normally spend hours puzzling out employee schedules and daily task assignments.
Reducing deliveries without sacrificing availability
While an effective supply chain solution can help select the right stock, it can also make delivery of that inventory more efficient for the employees handling the product. An advanced replenishment solution can help retailers smooth out high delivery peaks and balance deliveries over a longer period of time without sacrificing availability.
This delivery model helps store operations take advantage of low-traffic days and times to handle inventory so they can focus on service when customer traffic is heaviest.
A solution that understands planograms and store layouts can pack product cages to arrive “aisle-friendly,” reducing employee time spent on manual work and increasing stocking efficiency. The less time employees take running back and forth from the stockroom or reorganizing a shelf or cage, the more they can spend on value-adding work such as assisting customers.
Improving shelving efficiency through optimized space
A deeper look into the aisles reveals how the operation can become more efficient within the shelves themselves. Optimizing the right amount of product shelf space can maximize shelving speed and efficiency.
Proper space planning can even ensure stock only arrives exactly when needed and can go straight onto the shelf. The right solution can automate planogram and floor plan delivery to mobile devices in stores so staff have the plans and stock information at their fingertips.
With an effective space planning solution, employees will not need to run back and forth to stock rooms to make sure the shelves are full, and customers will be able to find the products they want when they need them. This effective use of floor and back-of-house space not only maximizes employees’ time and efficiency but also improves customer experience.
Alleviating workforce issues
A supply chain technology’s impact on store operations extends even into workforce challenges, helping in-store hiring managers better navigate an ever-changing and uncertain labor force in which finding the right skills is difficult.
When a best-in-class technology is in place to ease staff workload and give the right insights, the skill gaps between employees can narrow, making store performance less dependent on only the highly-trained workers. Retail operations leaders can feel empowered using a technology solution that not only efficiently delivers employee tasks and effectively reduces manual workload but also keeps employees feeling more fulfilled and secure at work.
The multitude of advantages that store operations can receive from a clever supply chain planning solution should make any retail operations leader recognize their importance in its selection and introduction.
Store leaders should be vocal advocates for their supply chain planning solution to ensure their needs are well-considered in decision-making. A modern, flexible supply chain solution will ensure that store operations have the right tools to continue improving processes and overcome the increasing complexity of effective store management.