More than milk: The demands of dairy call for a shake-up in planning
Sep 16, 2024 • 9 min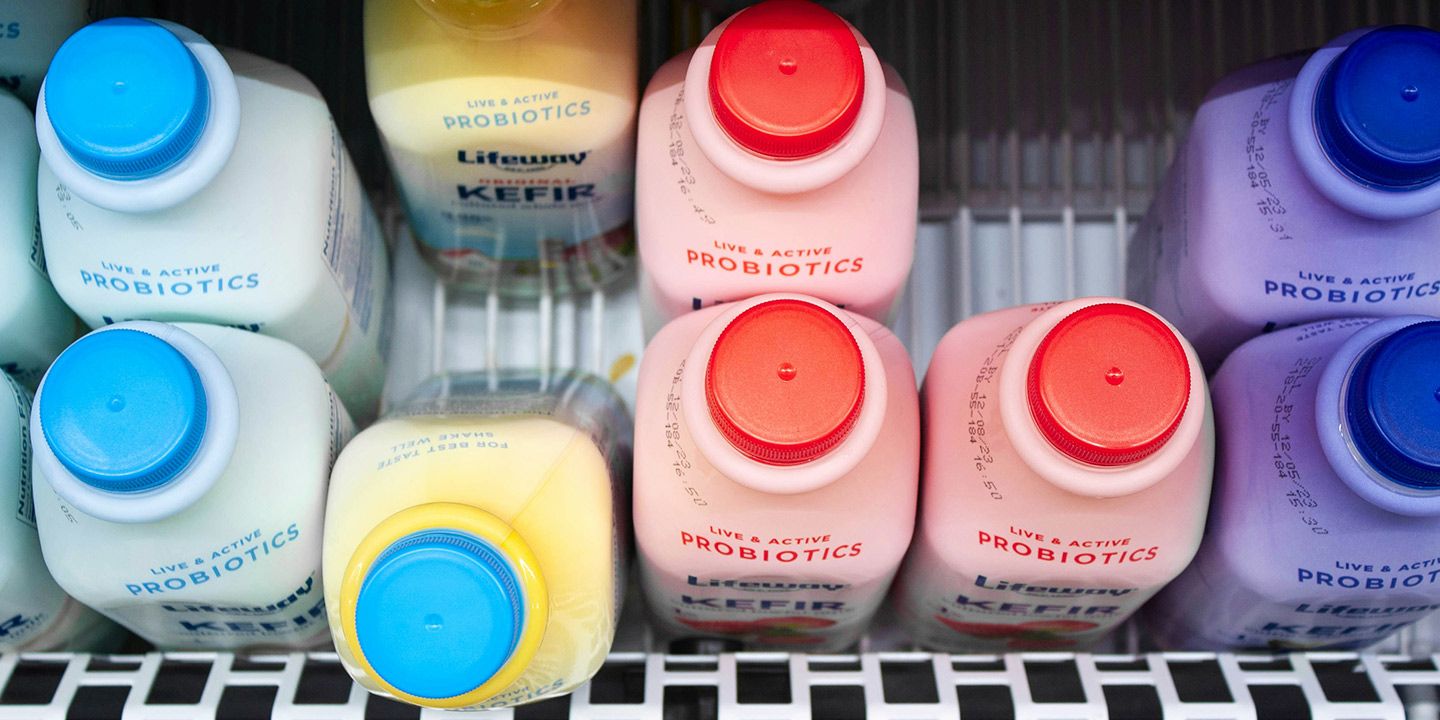
Getting dairy right
Optimizing dairy requires a shake-up, a more connected view across the entire dairy supply chain, and a rethink around processing, producing, and planning. Companies must look beyond milk to bring together cheese, creams, yogurts, ice creams, whey, and numerous additional product ranges and recipes in a holistic supply chain optimization opportunity.
However, it’s not an easy industry to optimize. The complexity of production cycles brought about by supply variability calls for significant investments in production assets and a planning procedure that considers both the long and short term. Too often, these investments and outlooks are currently driven by instinct and conversation rather than data and automation.
To maximize profit and achieve optimal efficiency in today’s dairy industry, it’s time to take overly manual processes out of the equation.
Relying solely on human experience and manual decision-making can only optimize so far when it comes to making vital strategic choices – namely, how to best use the raw milk that will continue to be supplied and where the most value can be extracted by taking into account all pertinent factors: internal capacity and capability, equipment and maintenance costs, labor, customer demand, the fresh-dairy production-dry powder pay-off, the last mile, and everything in between.
AI is the answer and solution in this context, but only if approached practically
The importance of leveraging technology that capitalizes on AI’s full potential to help overcome complexity and maximize business outcomes can’t be overstated. However, business leaders should view AI as a collection of algorithms and apply techniques to specific problems in a practical fashion rather than implementing it for the sake of keeping up.
If this balance is achieved, decision-makers can weigh internal capacity alongside external bottlenecks or fluctuations while laying out potential repercussions of different business scenarios, ensuring that the right decision is always made. And, in a sector where the supply keeps coming, a ‘right all the time’ mentality is precisely what dairy should strive for.
Dairy’s diversity
The difference between dairy and many other sectors is its constancy. Milk will never stop coming, provided everything is in hand with contracts and farmer relationships; its supply is continuous. On one hand, this brings dependability and consistency. However, this can’t lead to complacency when it comes to the phases that follow. Instead, the target should be to utilize that continuous asset for maximum profit. This isn’t as simple as churning out as much fresh milk to customers as possible.
Dairy producers must consider incoming raw materials a huge opportunity to optimize, seek optimal efficiencies, and see where the most value can be extracted from every incoming batch.
Traditionally, much of the ‘optimization’ focus has been on simply using the entirety of the initial supply. That mindset needs to shift to using the entire asset and filtering, storing, adapting, producing, and selling it in the most cost-effective and revenue-inducing way possible.
This shift in focus raises another area of variability and diversity – that dairy encompasses much more than just milk. While the focus often revolves around milk, there are many other avenues to explore to maximize revenue opportunities and give yourself the best chance of utilizing everything that arrives at your door.
When you pivot the approach away from milk itself and also to frozen products, longer shelf-life products, or even more specialist categories such as whey, the reason why more advanced planning is needed becomes clearer. Milk powder, for example, is an obvious output with huge global demand, but setting up its production line is expensive.
How to set up your infrastructure—filling lines and incubation tanks—is joined by the need to involve certain additives or colorings along the process for different products. The equipment, machinery, and labor needed to fulfil these varying elements must also be considered. Transport routes, especially once you enter the realm of cold chain, also need to be considered.
As soon as you expand beyond milk, which most must do to optimize the use of the raw material, the whole operation becomes much more complex. At that point, gut instinct, historical experience, and instinctive bias will work against the aims of achieving ultimate efficiency and maximum value.
This entire spectrum of dairy can be mastered only with end-to-end visibility and advanced planning. This doesn’t mean that all producers should be exploring all product avenues. Far from it—with clearer visibility, insight, and future scenario planning, the best-case value proposition can be put forward, along with a plan for how best to realize it.
Overcoming traditional planning pitfalls
McKinsey recently asked dairy executives what their priorities were moving forward. More than half (53%) emphasized the need to strengthen their corporate purpose for stakeholders. This mission was closely followed by the desire to implement cost reduction and efficiency initiatives (50%) and to enter new categories, markets and geographies (45%). Ironically, only 39% stated that increasing supply chain resilience was a priority.
Optimizing the supply chain with digitized planning and decision-making would make all three top concerns more seamlessly integrated.
To understand where dairy producers should look to achieve these objectives, it’s important to note where the risks lie for those who have not connected all pertinent factors through one central system.
These risks can be split into three areas:
- Demand forecasting
- Operational planning
- Supply planning
Sales teams tend to cling to a status quo that focuses on forecasting according to their own bias—to at least meet, but ideally exceed, sales budgets. The problem with this approach is that forecasting according to what you need to sell doesn’t necessarily translate to what you’re likely to sell. Everything on the production side that fills the in-between is then distorted.
This is where the risks to operational planning come in. Product mixes, inventory builds, line setups, changeovers, tank utilization – they will all be geared towards a level of demand that one siloed department hopes to achieve rather than a quantitative likelihood. From a revenue maximization perspective, this shortfall in demand also impacts promotions and cost markdowns. Once it’s clear that uptake differs from demand, there will be an urge to ensure clearance by reducing prices or introducing promotions too early. You might get items off the shelves, but at what cost?
The production team also needs to try to understand the implications of the demand plan from a supply perspective. However, when this is typically only explored one week – or sometimes even one day – from execution, there is little time to remedy any gaps between supply and this expected (guessed) demand. The effect continues then to supply planning, with the sourcing team in charge of contracts – but also conscious of seasonal fluctuations, weather variables and farm productivity –translating an inaccurate sense of demand before the process begins.
Similarly, supply planning is also hampered if operations and production need to pivot away from the original demand plan. Everything drawn up in terms of load volumes, cold chain ratios, shelf lives, inventory, and expected distribution times might have changed once the original manual demand forecast was found to be incorrect.
Working with intuition rather than facts exposes the fragmented nature of many dairy operations, not only creating a stressful or fractious work environment but also wasting valuable supplies and money.
Mathematical optimization: the AI action plan
The answer is to bring all these strands and their associated data into one system.
Everything that contributes to the final notion of ‘optimization’ – the departments, the customer demand, the external factors, the supply volumes, the transport capacity, the product categories, machine and shift capacities, the associated price points, and the optimal times to markdown and promote –must be brought together into one source of truth. This holistic breakdown of siloes, biases and opportunities to generate value will also – as a result – yield a level of agility that strengthens corporate positioning, that reduces costs and makes operations more efficient, and paves the way for new categories, markets and geographies.
In this sense, true supply chain optimization can perhaps be better described as mathematical optimization.
The model forms one strand of the AI ecosystem with an ability to evaluate concurrently any and every viable option to produce the most profitable way forward. It sits alongside ML for promotion and forecasting predictions, heuristics to align plans and minimize efficiency losses, and generative AI, which is still in its nascency. In the context of dairy, in particular, mathematical optimization can form the basis for all the production and operational decisions that can be made once the supply, capacity, demand, disruption, and cost elements are all – truly – understood.
For the planner, this is far from a takeover or an undermining of their role. Instead, it gives them more time to focus on exceptions and establish desired objectives the system can feed off. It gives them greater foresight of potential problems, which can be communicated to all partners and departments. It requires very little input from them, although manual configurations are possible.
The increased speed of optimization algorithms allows them to run multiple what-if scenarios with the help of a digital twin to ensure the up-to-dateness of business rules, costs, and constraints. More generally, mathematical optimization allows the planning function to be more strategic and contribute more concertedly to those aforementioned business priorities.
This level of operational, business, and culture shift can often be daunting. Still, modularity is one of the most significant benefits of a mathematical optimization journey in the supply chain. Yes, the holy grail is to have all services and functions feeding into It to ensure all corners of the business are being considered and analyzed seamlessly. But realistically, it will be a gradual evolution to minimize risks and costs, driven by a prioritization agenda that we at RELEX can assist with.
Evolving with RELEX
RELEX typically advises businesses to start this optimization journey by focusing on master planning, particularly production planning. Production planning—optimizing the use of incubation tanks, the management of ageing or expiring products, and when to pivot to longer-lasting products, knowing how and when to adapt recipes according to demand while also ensuring they’re profitable—is the most crucial strand of the overall journey and can set the tone for the ultimate solution that dairy operators should now be striving towards.
RELEX is one of the few innovators in the supply chain space that can address all typical challenges experienced by specific food and drink industries. We don’t generalize. Instead, we treat dairy as a distinct industry with unique challenges and opportunities.
If you are looking for examples of how we are targeting solutions towards specific challenges, look no further than the cold chain. More than most other considerations, it epitomizes the complexity and diversity of dairy. Maintaining the integrity of the cold chain is crucial for preserving the quality and safety of all dairy products, from the point of receipt and collection to the moment they are handed over to the consumer.
The extent of temperature-controlled environments any dairy product must pass through along the way makes spoilage, reduced shelf lives and health risks very real dangers. To this end, our optimization tool brings together metrics related to storage, transportation, packaging, temperature monitoring and control, and handling processes – all to ensure the most efficient delivery of a healthy end product.
Another specialized challenge that RELEX has worked hard to combat includes tank management. Producers often have a limited number of tanks, which can restrict production capacity. Coordinating the timing of batches with availability and production capacity is critical to avoid delays or the spoiling of batches. This management becomes more complex with a product such as yogurt as the whole tank must be used for that one purpose before resetting it.
Further, if your packing line is not ready when your incubation tank is, you’re not only wasting capacity but also impacting the broader plan and schedule. RELEX helps model tanks as resources used in product structures, acknowledging and preparing for the fact that they can’t be reused until emptied, cleaned, and reconfigured and aligning that known tank capacity and capability with the packaging process after that. Whether it happens as quickly as you’d like is redundant. Knowing the actual lead times across the process allows planners to do what they do best: plan.
Synchronizing production stages, adapting to supply variability, optimizing packaging of products such as yogurt, and even introducing mobile tanks are further dairy-specific challenges we have seen operators struggle with as we have embarked on our own journey through the sector.
The result is a one-stop shop for addressing these bottlenecks and converting them into optimized efficiency and revenue opportunities.
Shaking up the sector
Dairy is so much more than just milk. The milk will always arrive, but optimizing its use is another matter. Manually deciding which products to prioritize and pivot to, how to master operations and production, what demand to fulfil and at what prices, and how to prepare for future supply presents too many trapdoors to fall through. It works against the ultimate goal of producing the most profitable product mix from available supply in the most efficient way possible.
Not only is there now a solution that can integrate all these internal and external elements, but it does so through a mathematical optimization model that will embolden your planners and your supply chain more generally. Learn more about how RELEX is helping the dairy industry realize significant commercial opportunities, more scope for diversification, and greater efficiency and profits.