Poultry’s potential: Enhancing performance, efficiency, and your bottom line
Poultry processing, like most other protein businesses, faces unique planning complexities that expand far beyond the capabilities of manual decision-making if optimization is to be achieved.
As opposed to traditional manufacturing, where different elements are added over time, poultry processing involves disaggregation. This disaggregation introduces complexities such as carcass balancing, which is critical for maximizing the cut plan for each bird and a key component of profitability. Other critical considerations for poultry processing include managing surpluses, bird weight distribution, forecasting accuracy, gaining end-to-end visibility, enabling clearer and more fact-based leadership, improving inventory management, managing shelf life, and scenario testing to drive more informed business decisions.
Ultimately, the birds won’t stop coming. The primary goal for processors is to manage that supply effectively to keep customers happy and raise the bottom line. The truth is that spreadsheets are no longer sufficient to handle such levels of complexity.
While the full poultry supply chain includes both agriculture and feed production, this document will focus on poultry processing.
The primary sections of the poultry processing supply chain
Section 1: Rearing farms – Egg production – Egg bank – Hatchery
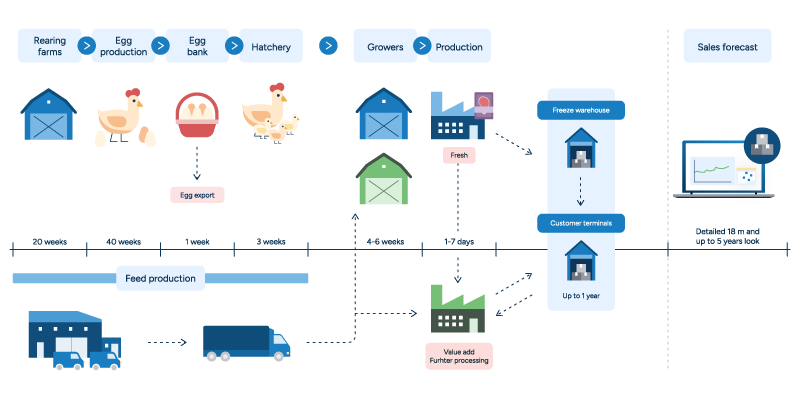
The rearing farms, egg production, egg bank, and hatchery form a critical part of the poultry supply chain responsible for producing day-old chickens, which are then moved to growth sheds for further rearing.
- Rearing Farms: These farms raise hens specifically for egg production. The hens are nurtured and prepared to reach optimal health and maturity so they can lay fertile eggs.
- Egg Production: Once the hens are mature, they start laying eggs that will eventually hatch into chicks. The quality of the eggs is crucial, and the farms must ensure that hens are well-fed, healthy, and in the right environment to maximize egg production and fertility rates.
- Egg Bank: The eggs produced by the hens are collected and stored in controlled conditions. This “egg bank” ensures the eggs are kept in optimal conditions before being transferred to the hatchery. Proper temperature and humidity control are essential during this stage to preserve egg viability.
- Hatchery: In the hatchery, eggs from the egg bank are incubated until they hatch into day-old chicks. The hatchery ensures that the right environmental conditions are maintained for successful hatching. Once the eggs hatch, the chicks are moved to the growth sheds, where they continue their development until they reach maturity for slaughter.
This section of the supply chain is essential for producing healthy, viable day-old chicks, ensuring a steady supply of poultry for the production phase.
Section 2: Feed production
Approximately 60–75% of the total cost of poultry raised for slaughter comes from bird feed, making it the most significant expense in the production process.
Because of this, it’s crucial to ensure that feed production is highly efficient, whether managed internally or outsourced to a third party. Efficient feed production not only helps control costs but also plays a critical role in the quality and health of the birds, directly impacting their growth rate and eventual profitability.
By optimizing feed usage, formulation, and delivery, growers and integrators can significantly reduce overall production costs and improve margins.
Section 3: Growers
Growers receive poultry chicks from a poultry integrator and are responsible for providing shelter, care, and other necessary services over a specified period. Their role is to raise the chicks to the appropriate maturity level for slaughter, ensuring the poultry meets the desired growth and health standards.
Section 4: Poultry Processing
Poultry processing, the focus of this article, includes several key stages. While these stages can vary from one poultry business to another, they typically consist of:
1. Processing
This stage refers to the process from the kill stage through to producing a completely deboned bird. It involves the slaughter of the poultry, removal of feathers, evisceration, and deboning. The result is raw poultry prepared for further handling or sale.
2. Value Add
At this stage, the poultry is still raw but undergoes further preparation to enhance its value. This may involve adding sauces or marinades, creating specific products like kebabs (placing cuts on sticks), or preparing pre-seasoned cuts. This step allows the product to be more market-ready, catering to consumer preferences for convenience and variety.
3. Fresh
In this phase, the business processes different cuts of poultry (such as breast, thigh, or wings) and packages them in various forms for sale as fresh products. This could include individually packaged cuts, combo packs, or whole birds, typically sold to consumers or retailers who prefer non-frozen, fresh poultry.
4. Further Processing
Also referred to as cooked products, this stage involves cooking the poultry in various shapes and forms. It may include grilling, baking, or frying to create fully cooked products. These cooked cuts are typically frozen to extend shelf life and sold as convenient, ready-to-eat or ready-to-heat products.
5. Frozen
In the frozen stage, poultry products are frozen to meet consumer demand or manage production surpluses. Freezing can be applied to both raw and cooked products, offering the business flexibility in inventory management and enabling long-term storage for off-season sales or bulk fulfillment.
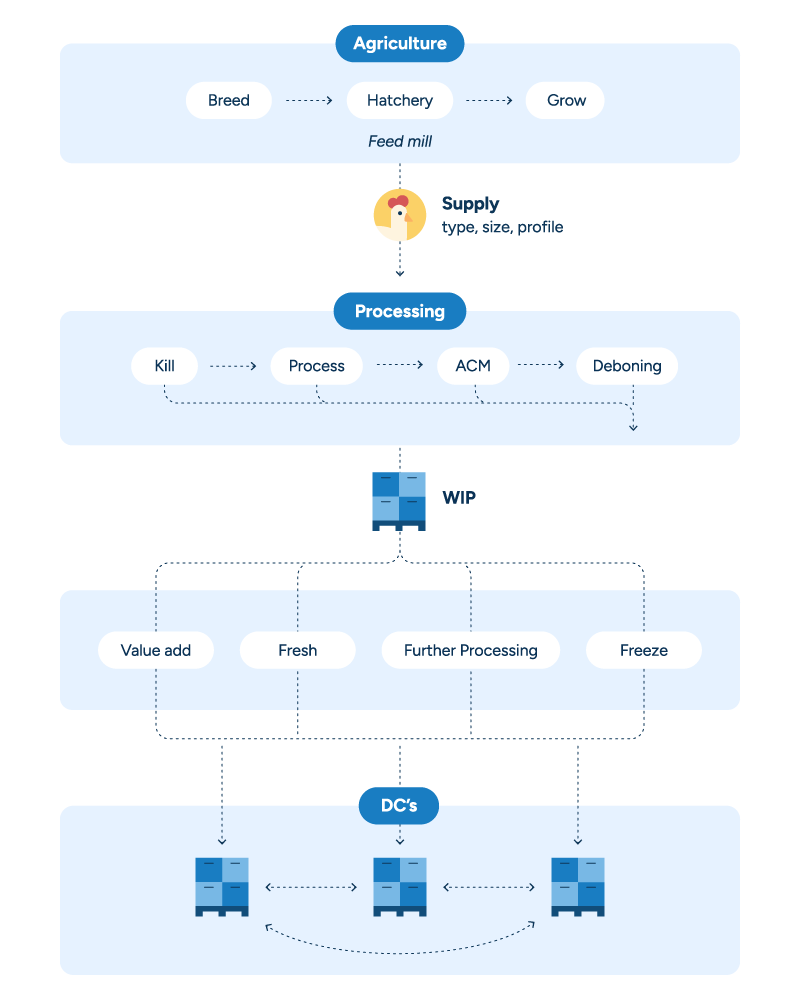
10 essentials to elevating the poultry supply chain planning process
This guide outlines ten essential areas needing one unified, automated system where decisions are made based on facts rather than personal experience, siloed teams, and gut instinct. A system that ensures bird utilization and profits can be maximized, revenues can be enhanced, and poultry processing can reach its full potential.
1. Balancing the bird
Balancing the bird is more complicated than it sounds. It is not just the balance of utilizing every part of the carcass, although that is critical. It also refers to a balance of available supply and customer demand. In most cases, there will be an imbalance that will force a planner to make trade-offs that can quickly become very complex.
Optimization—the goal that all poultry planners should strive for—is ensuring that each bird yields maximum profit. This means using the bird in its entirety, ensuring that all its parts find their way into the best possible profit stream.
There is versatility in poultry to reach this extent of optimization. Each chicken can be cut and utilized in numerous ways, with each finished product deriving from the various cuts or bill of materials (BoM). For example, when preparing a chicken teriyaki dish by using meat from chicken legs, the meat can originate from different bird classifications and sizes.
However, the complexity comes from the ‘profit maximization’ element. There are situations, for instance, where customers prefer specific cuts. In other scenarios, customers are more willing to accept substitutions. The trade-off might be a less lucrative end product but with higher demand and guaranteed revenue.
Ultimately, given the unpredictability of bird sizes, the variability of end products, differing customer demands, and fluctuating price points, the ultimate complexity lies in the thousands of cut plans that need to be balanced to manage supply and demand in the most effective way possible.
AI models comprising heuristics and mathematical optimization enable the simultaneous evaluation of numerous options to identify the optimal mix, all while considering factors such as limited supply, demand fluctuations, shelf life, and various business rules and constraints.
2. Surplus management
While striving to balance the bird based on customer demand and available supply, either a shortage or surplus of cuts is still inevitable.
Many businesses only resort to managing surpluses once they actually know how much excess they have in the chiller – a very reactive process – or a manual best guess based on historical results and prior experience. This inevitably leads to clearance sales and markdowns.
As described under point 1, generating an optimized plan means adopting a proactive stance. It means minimizing the volume of surplus cuts that end up in the chiller in the first place. This level of proactivity can only come from visibility, which can only be achieved through digital means.
With clear visibility of surplus cuts over a longer time period—even up to 16 weeks—sales can work to find potential customers ahead of time and the optimal revenue channel for the excess cuts.
This push for maximum value will replace the typical method of enacting quick-fire sales of promotional items to get rid of stock. It will also decrease the need for freezing, meaning you can charge more for fresh items rather than frozen.
Having true visibility of supply and demand—what’s coming in and what needs to go out—gives planners and sales teams a head start on determining where the most revenue can be achieved while freeing up space in chillers/freezers for the next batch to arrive.
3. Agility adoption
The poultry industry is characterized by fluctuating supply and demand dynamics, highlighting two key needs: enhanced, automated visibility to track real-time and forecasted trends and the agility to respond swiftly to these changes. These challenges are particularly pressing for stakeholders in fresh and further processing operations, where the persistent risks are excess inventory or unmet demand.
Processors need to be able to quickly recut their plans in response to changes in demand and supply signals.
In a company heavily driven by spreadsheets and manual cut-and-paste, it might take weeks to adjust the plans, making it impossible to respond quickly enough. Consequently, businesses end up missing demand, sitting with too much surplus in the freezer or having to sell surplus at a highly discounted price.
4. Further processing optimization
The advantage of further processing is the longer planning horizon and the extra time afforded by not racing the original bird out as a fresh product. As a further processing product can be frozen, it gives a much longer shelf life meaning more stock can be held and longer production runs can be enabled.
The value doesn’t simply come from having longer-life products available to sell. It also comes from increasing line utilization, producing more with the same equipment and people.
If a line operates at 85% capacity (with the remaining 15% allocated for maintenance, reconfiguration, and cleaning), there may be opportunities to improve this ratio. In further processing, most lines can be adjusted to meet varying production requirements for different products. However, this reconfiguration takes time, during which production comes to a halt. For example, for breaded products, the breading machine needs to be installed into the production line, and after it’s finished, it needs to be removed. With better planning, the line can be kept in a particular configuration for longer, reducing the need for changes and having a sizable impact on the ultimate bottom line.
The challenge with running longer runs is to balance the cost of holding stock, expiry challenges warehouse costs, with the benefits from increasing line utilization. Using mathematical modeling and optimization will automatically find the most optimal mix.
Increasing the line utilization from 85% to 95% means that we will produce roughly an additional 10% at a gross margin that would only consider the cost of the raw material. The impact on the bottom line can be significant. Creating a production plan that considers all of the above factors with a view to broadening that profit window can best be achieved with advanced AI-enabled solutions.
5. Increasing forecast accuracy and accountability
Improving forecast accuracy and accountability in the poultry industry can significantly impact its efficiency, profitability, and sustainability.
- Forecast Accuracy: Accurate forecasts allow producers to make better-informed decisions regarding production schedules, feed purchases, and inventory management. This minimizes waste and price erosion, reduces costs, and ensures that resources are used efficiently.
- Forecast Accountability: When forecasters are held accountable for the accuracy of their predictions, there is a stronger incentive to refine forecasting processes, models and methodologies. This leads to continuous improvement in forecast quality, further optimizing resource allocation.
Improvements in accountability will support improved forecast accuracy, and improved forecast accuracy will specifically help poultry producers in the following areas:
- Optimized Production Planning: The poultry industry is highly sensitive to supply and demand fluctuations. Accurate forecasts allow producers to better plan production schedules, hatcheries, and processing timelines, ensuring that they meet market demand without overproducing or underproducing. This reduces waste and improves profitability.
- Feed Cost Management: Feed is the most significant cost in poultry production, typically accounting for 60-70% of the total production cost. Accurate forecasts of future demand enable producers to purchase feed ingredients in optimal quantities and at favourable prices, reducing costs and improving margins.
- Inventory Management: Accurate forecasting helps in managing inventory levels of both live birds and processed products. By aligning production with demand forecasts, companies can minimize the costs associated with storing excess inventory or dealing with shortages.
- Supply Chain Efficiency: The poultry supply chain is complex, involving breeders, hatcheries, feed suppliers, processors, and retailers. Accurate forecasts help in coordinating all these elements more efficiently, reducing lead times, transportation costs, and bottlenecks.
- Environmental Sustainability: Accurate forecasting can contribute to more sustainable practices by reducing overproduction, which in turn reduces waste, energy use, and the industry’s environmental footprint. It also helps optimize resource use, such as water and land, which are critical in poultry farming.
Greater forecast accuracy means production, bird supply, and the overall supply chain will be aligned with demand. This will help remove this siloed pull in different directions from the equation. Everyone can see the extent of chickens incoming and then make an optimal plan for what to do with them. This also brings accountability, with sales and procurement not able to go rogue or cover their own backs, which could potentially damage overall profit margins.
Moreover, from a job satisfaction and collaboration perspective, this move towards greater accuracy and accountability reduces friction and chaos. Bringing together departments with different aims to try and understand different versions of spreadsheets can become very messy. This messiness can be replaced by one collaborative, seamless source of information to work from together.
6. Establishing visibility
Beyond optimizing the management of surplus birds or cuts and balancing supply and demand, improved visibility also enables a stronger focus on exceptions rather than merely gathering information. Each producer’s needs are unique based on the types of customers, regions, and demand patterns they serve. Some customers will need demand satisfied to exact specifications regardless of any internal bottlenecks or constraints. Others might require more flexibility when it comes to different size demands or shelf life.
Visibility is a slightly generic term, but in the current context, it derives only from digitization and automation. It envelopes the ability to elevate areas of customer service, ingredient management, capacity management, the labor force, storage and warehousing, 3PL utilization, shelf lives, and all other aspects that feed into an optimized supply chain planning process. You can’t plan without visibility, and seeing only with human eyes will offer a fraction of what needs to be seen.
At present, most companies run their supply chains on a stack of different, siloed spreadsheets. True visibility, by contrast, should enable a complete view of all aspects of the supply chain over an entire planning horizon. For poultry, this amounts to around 13 weeks, with companies understanding where they will be across key parameters at each stage of that horizon.
Those parameters relate to production capacity and whether more resources need to be added. They include inventory levels and expiry issues, as well as distribution requirements. The supply of birds and ingredients for different recipes also needs to be visible across this time span.
Without a solution that provides end-to-end visibility of the above, the result is a very reactive process, near misses, and—likely—actual misses: too much inventory, a race to clear surplus products at lower prices, and a mismatch between supply and demand.
7. Leadership enablement
When you’re relying on multiple spreadsheets and different departments are pulled in different directions based on the information from these manually derived documents, the notion of leadership also becomes hazy.
Planners usually have a master spreadsheet comprising formulas that only they would understand, overriding the influence of a management arm that would also have to defer to this complicated representation of digital-meets-manual. Instead of amalgamating different manually input data sets and creating confusion, systemized planning allows all departments to work with one interpretation of facts. There is no more bias and no more personal authority to preserve customer or supplier relations.
Time and time again, human experience, bias, and instinct get quickly undone by a crunch of numbers through a dedicated, unifying, automated system. We have seen situations where a planner’s gut feeling tells them to do one thing, only to later find that this would lose the business a lot of money if all relevant factors were visible and had been taken into account.
A system with one clear source of fact-based analysis enables and strengthens leadership, helping to override departmental gut feelings. The result is quicker decisions, less deliberation, more concise and rapid information relayed to customers, and a consistently clear view of how real-time plans are impacting the bottom line.
Meanwhile, everyone reporting to that leadership team is spending less time collating and deliberating inaccurate information and instead is focusing on actions.
8. Improving inventory management
Inventory management within the poultry industry is related to 3 areas:
- Frozen
- Further processing (cooked products)
- Ingredients
One aspect is, of course, setting the right safety stock. Traditionally, safety stock is set as a number of days of coverage, and many times, it is based on limited analytical insight.
Using mathematical modeling and optimization, businesses diversify the safety stock based on variables such as demand variation, forecast accuracy, supply lead-time and supply lead-time variances (ingredients), the cost of holding the stock, the cost of missing demand, and minimum batch sizes. However, this primarily relates to ingredients.
When it comes to frozen and further processing, these products can be used to balance demand and supply over a longer period, hence, we might want to define a maximum stock. This can also be used to balance further processing line capacities.
Stock optimization also spans optimal stock distribution, ensuring the right stock is in the right place at the right time. There are gains to be made and money to be saved by reducing distribution times and optimizing pallet and transport loads.
The role of 3PLs also falls under this category as producers expand their warehouse footprint and transport fleet. The cost of receiving, holding and dispatching pallets all need to be recorded, quantifiable and accurate figures that feed into the cost of operations, and weighed up for optimal decisions.
More broadly, inventory management also covers obsolete items, managing the expiry of goods to extract the most money out of each product through price markdowns and promotions without panicking ahead of time and potentially missing out on value.
Inventory management still holds the key to numerous opportunities to lose or gain efficiency and revenue.
9. Running scenarios
The ability to run scenarios can be very important when preparing for an efficient supply chain. We’re not so much talking about replicating the status quo as about the impact of adding new dimensions to the process. What-if scenarios are an essential part of supply chain decision making?
A new product, a new market, a new warehouse, a new 3PL provider, additional production lines, and a new chicken shed to grow the birds. Again, with only manual instinct to go on, the ambition to strike while the iron is hot, to channel profits into investments, and to scale at pace is understandable. But everyone knows of examples where these more expansive decisions have played out poorly or have proven to be a stretch too far and too quickly.
Scenario planning capability ensures that the ‘new’ is considered and delivered at a scale that generates maximum value. Moreover, it is important that these scenarios are clearly presented through a dashboard that encourages users to make the right decisions from the information available.
Running various scenarios allows poultry producers to test different outcomes and strategies. It represents a much more proactive approach that helps optimize operations, anticipate challenges, and make informed business decisions.
10. Establishing an S&OP framework
Sales and Operations Planning (S&OP) is an extra critical process within the poultry industry due to the industry’s complexity, perishable products, and the need to balance supply with fluctuating demand. The S&OP process creates an understanding across the entire supply chain of why certain decisions are made, and it removes organizational silos.
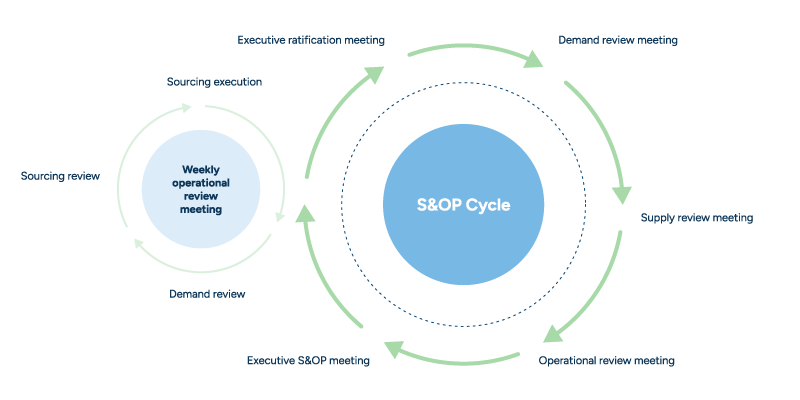
To enable a solid S&OP process, you need essentially two things:
- A system that will provide all (or at least most) of the answers to the questions that the S&OP process needs. The information needs to be provided accurately and automatically.
- A well-defined process.
Below are the key steps to establish an S&OP process:
Step 1: Defining the planning horizon
Each company will have a different planning horizon based on their own specific challenges and customer portfolio. It’s important to begin by defining your own.
Step 2: Defining the S&OP and S&OE process
A meeting card for each review meeting must be established, covering several key aspects. These include what the review meetings should consist of, their frequency, who will chair and attend them, the desired outputs, the necessary inputs, and the governance process to ensure all of the above is adhered to.
Step 3: Defining input questions
There will be certain questions that S&OP requires answers for in each meeting. It’s important to list these questions ahead of time, assigning different talking points to the different stages of the planning horizon. Examples of key questions would be, “Do we have enough capacity? Are we holding too much stock? What are the projected shortages? How much surplus can we expect?”
Step 4: Defining the governance process
As referred to in Step 2, the chosen process and timelines need to be underpinned by an effective governance model—a set of rules and consequences that ensures everyone follows the process. It is important that there is an overarching process that will identify and rectify any non-adherence to the defined process.
Effective S&OP complements all other strands related to greater visibility and clarity of decision-making. It enables more fact-based leadership decisions and supports the role of digitized scenario planning.
By following this framework, you can ensure everyone is singing from the same hymn sheet to get the most out of your S&OP.
Playing chicken and winning
Poultry planning is unique and complex, but there is also an established consistency within the sector. The key is to optimize—to use every bird in the most cost-effective and lucrative way. This means balancing the carcass, gaining visibility of real-time demand relative to supply, prioritizing differing customer needs while minimizing surpluses, and running scenario simulations to make optimal business decisions.
Such optimization can’t be achieved manually or via spreadsheets. The only way to play chicken and win is to put these complex processes in the hands of artificial intelligence—heuristics, mathematical optimization, machine learning, and generative AI.