Production planning without the headaches
Aug 23, 2024 • 10 min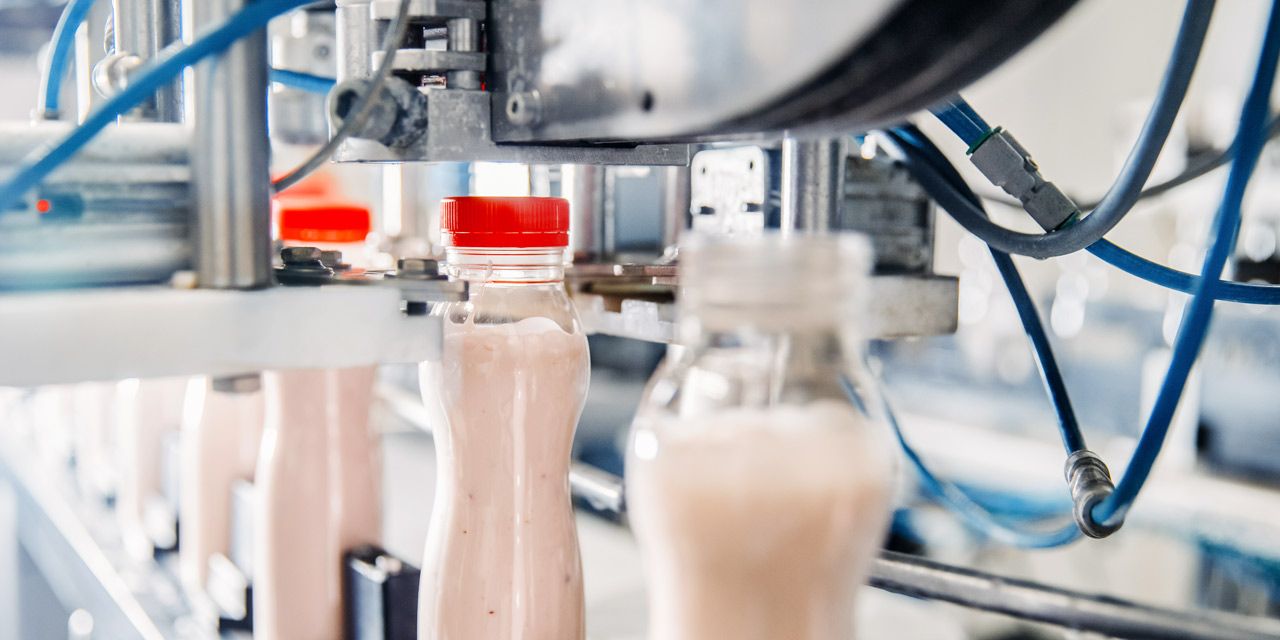
Production planning can propel a company to success or sink it into a mire of costly inefficiencies. An optimized production plan keeps the many (literally) moving parts of the manufacturing process operating smoothly – but building this plan is a balancing act.
Say you’re an ice cream company, and you’re producing multiple flavors. You’ll need to:
- Determine how many units to produce on what lines to meet demand, while reducing cleaning and maintenance time.
- Stock enough raw materials and ingredients but not so much that you jeopardize freshness.
- Regularly test samples for quality and safety while ensuring proper temperature control throughout your network so you don’t end up with puddles.
- Maintain close to 100% utilization on production lines while you have available labor.
These are only a few considerations, not even including external factors like demand volatility, seasonality, and weather events.
Optimized production plans integrate all these factors to ensure a smooth process from plant to spoon.
What is production planning?
Production planning outlines how products will be manufactured, accounting for production constraints and detailing production targets, bills of material, and overall scheduling. Through greater efficiency and reduced costs, optimal production planning ensures the best use of available time and resources, safeguards quality assurance, fulfills demand, and maximizes profitability.
Using our hypothetical ice cream company, let’s look at the elements of production planning:
- Forecasting: An efficient production plan rests on forecast accuracy. Understanding expected demand helps the manufacturer determine how much of each flavor to produce and how much stock to build during slow winter months to fulfill heavy demand during the summer.
- Materials and resources: The materials and ingredients need to be available in the right quantity at the right time. A material plan with optimal inventory levels that align with the production plan will help ensure availability.
- Production schedules: Using the forecast and considering production constraints (such as how much ice cream can be mixed by a single mixer), production planners decide inventory targets for each flavor and determine the proper daily batch production size for each product. They also schedule which items to produce on which lines, guiding the process from mixing to packaging.
- Performance and adjustments: Planners monitor production line performance, adjusting schedules as needed to fulfill demand while ensuring quality and efficiency along the supply chain.
Production planning vs. production scheduling
Production planning is a strategy that determines when, what, and how much to produce. Production scheduling is a subset of production planning that makes that strategy a reality. It sets the timetable for the production process, determining when and how each production activity will be completed to meet deadlines.
For instance, in the ice cream manufacturing example, a production plan might outline that in the week of August 5-9, the company must produce:
- 10,000 units of vanilla
- 8,000 units of chocolate
- 3,000 units of strawberry
- 3,000 units of mint
Production schedulers then assess daily and weekly production capacities, including labor and equipment, available raw materials, and perishability constraints, to compile a production schedule.
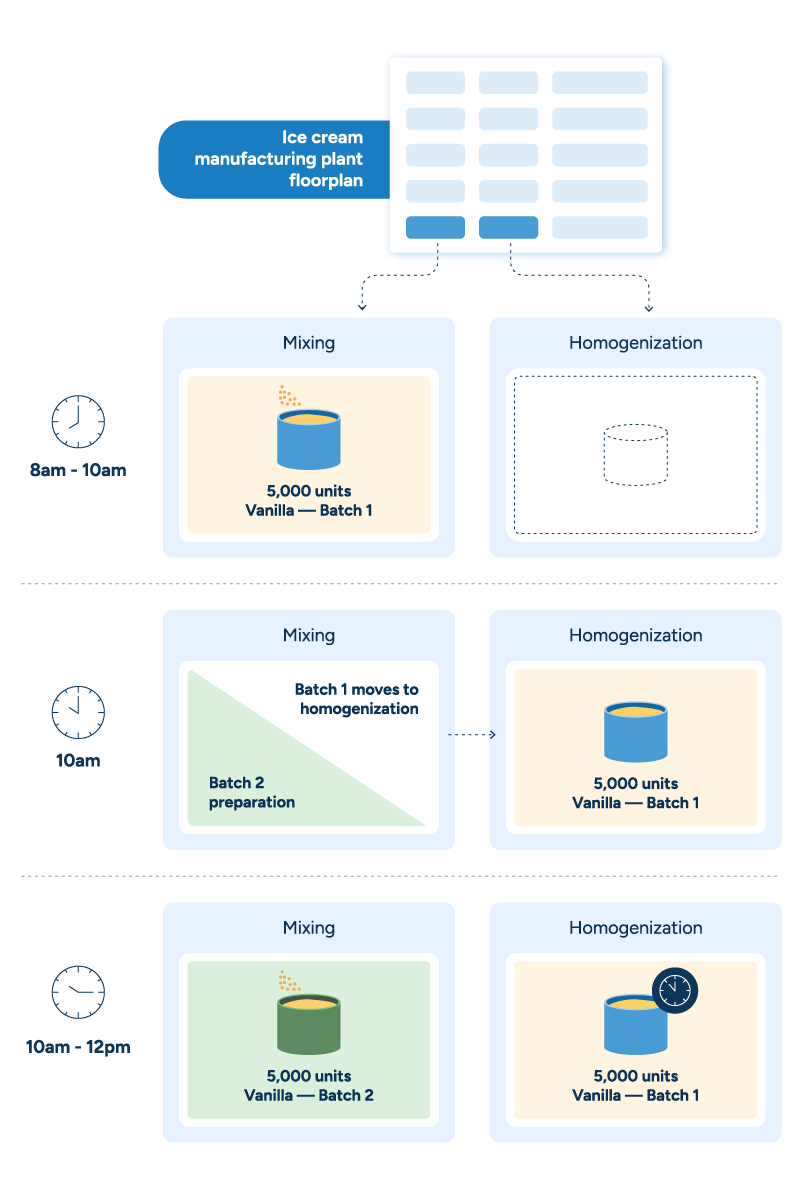
Unless it’s a smaller, artisanal company, the manufacturer will likely have multiple production lines, each requiring its own schedule to reduce idle time and make the best use of available resources.
Benefits of an optimized production planning process
Manufacturers with robust production plans set themselves up for long-term success, increasing resilience and sharpening their competitive edge through efficient, scalable strategies. The better the planning process, the sooner they start raking in the benefits:
- Increased service levels with minimal inventory: With accurate forecasts, companies can cater to customer demand, anticipating spikes and ensuring available inventory without producing overstock.
- Enhanced efficiency and productivity: Automated solutions help production planners best determine how to use available labor and materials. They also save teams valuable time by generating plans for them to approve and alerting them to isolated anomalies that need review.
- Greater visibility and collaboration: A good production plan does not operate in a vacuum. By integrating with other planning functions and collaborating with trading partners, production planning can adapt to current supply chain needs and drive overall efficiency.
- Better quality control: Manufacturers can reduce spoilage on both ends of the supply chain by keeping tabs on raw material expirations and tailoring production to meet demand.
- Cost savings and reduced waste: By calculating minimal required inventory, manufacturers produce only what they can sell, reducing production costs and cutting waste for both raw materials and finished goods.
- Scalability to support growth: More cost-effective and efficient practices protect working capital investments and generate reinvestment opportunities for network growth.
5 production planning challenges
We’ve talked about the sunny side of production planning, but any planner knows it has its dark moments – like when that vital spreadsheet breaks or a supplier is unexpectedly short on an order. No obstacle is insurmountable, but it pays to be aware of the challenges and develop a counter strategy.
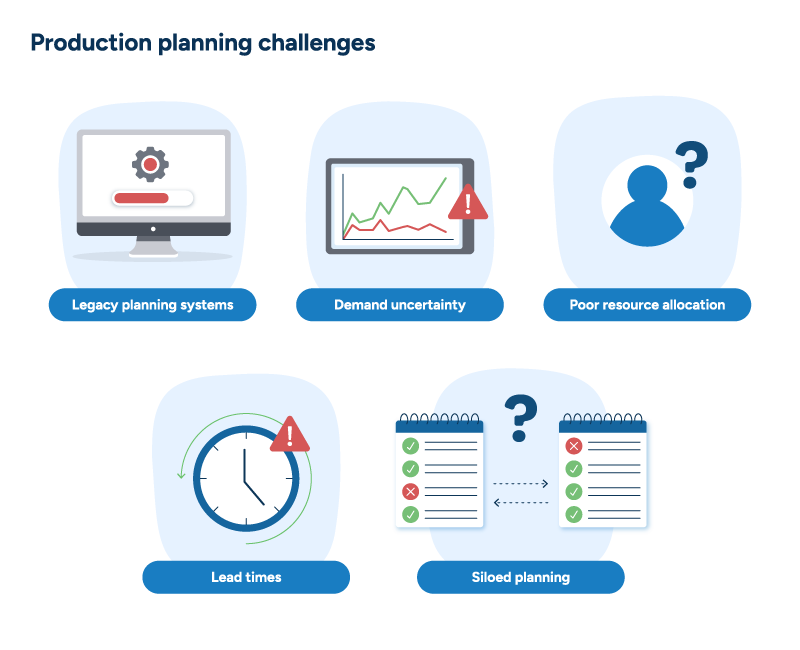
1. Outgrown legacy planning systems
Due to the complexity of manufacturing environments, legacy technology and spreadsheets are no longer feasible management tools.
A spreadsheet, for example, can quickly snowball out of control, becoming a massive lattice of data and formulas that is cumbersome and liable to break. Plus, depending on how decentralized your planning process is, you may have slightly different versions of this gigantic file for different plants around your network, amplifying planning issues exponentially.
Moreover, these tools don’t have the analytical power to optimize for different targets and balance constraints. For instance, suppose you’re determining whether you should use rail or truck to ship your finished goods. Rail would be cheaper but much slower. To assess the feasibility of your options, you need to determine how lead times would impact the start of production. Your not-so-trusty spreadsheet is not built to balance so many constraints simultaneously.
2. Demand uncertainty
From geopolitical tensions to extreme weather events to inflation, no supply chain is impervious to disruption and the ripple effects on customer demand patterns.
Severe demand fluctuations can lead manufacturers through a tricky dance as they try to produce just enough safety stock to take advantage of sales spikes while avoiding excess inventory once demand drops. Since many companies must plan and produce months in advance, these sudden changes are difficult to navigate and can seriously impact manufacturers’ inventory levels, resulting in overstock cluttering up warehouses or stockouts jeopardizing customer satisfaction.
READ MORE: Demand sensing: How to conquer CPG supply chain chaos
3. Poor resource allocation
When scheduling production, planners must make many decisions, such as how to minimize cleaning times, what batch sizes to run, or how to smooth capacity by producing or freezing ahead of time. Moreover, many raw materials and finished goods have varying expiration times that must be factored into production plans.
It’s up to production planners to hit freshness, efficiency, and production targets cost-effectively. With so many contributing factors, this can be a time-consuming and complex process, rife with missed opportunities for efficiency gains.
4. Siloed planning
Lack of coordination seriously hampers effective production planning, and often, technology is to blame. Say the production planners are bogged down in spreadsheets. How good is the data in those spreadsheets? Are all the other planning functions (like demand planning, procurement, and sales) sharing data and working from the same file? Can it support those functions? Are they all aligned on goals and processes?
Chances are, without a robust planning platform, these teams are operating in silos, which can lead to costly inefficiencies, poor inventory management, and low service levels.
5. Lead times
Lead times can upend production plans and schedules. Rigid, time-consuming, or highly manual processes lack the analytical horsepower to pivot as quickly as the market requires. When delays hit (often without warning), planners scramble and work long hours to adjust production plans. The response is rarely optimized, cost-efficient, or rapid because tech stacks aren’t helping planners tackle the unavoidable challenge of lead time variability.
3 essential software features for optimized production planning
So how can a production planner overcome these challenges to develop an efficient production plan that drives profit and raises service levels?
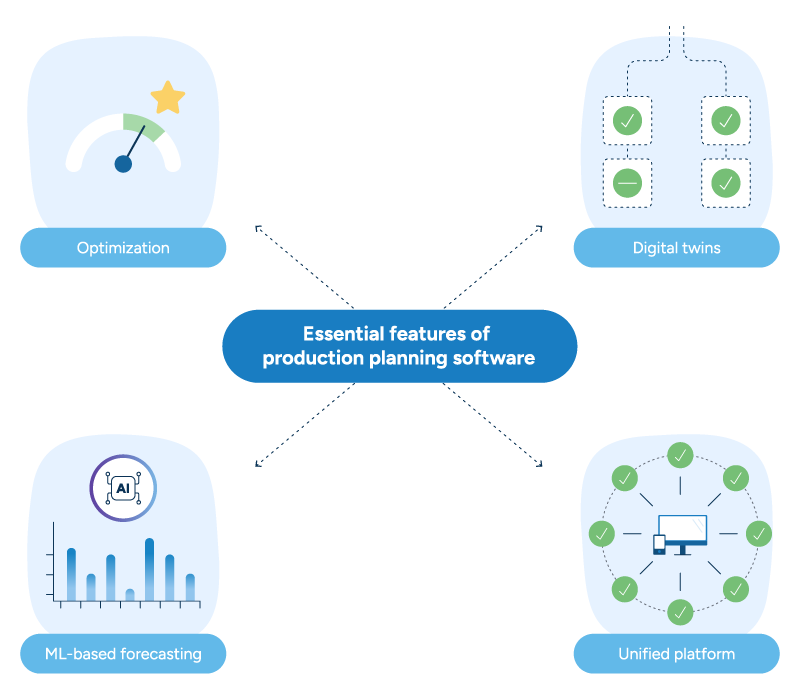
1. Optimization and digital twins
Optimization capabilities smooth and streamline production planning in complex environments. They balance multiple constraints to achieve an objective function, such as maximizing profit or minimizing costs. Manufacturers can customize optimization guidelines, setting both strict rules that protect KPIs like service level targets and softer constraints that accrue penalties but make the plan more flexible.
Since manufacturers must work within their confined solution space – the parameters of strategies, technologies, and materials available to them – this balanced approach helps them work within limitations to achieve those objective functions.
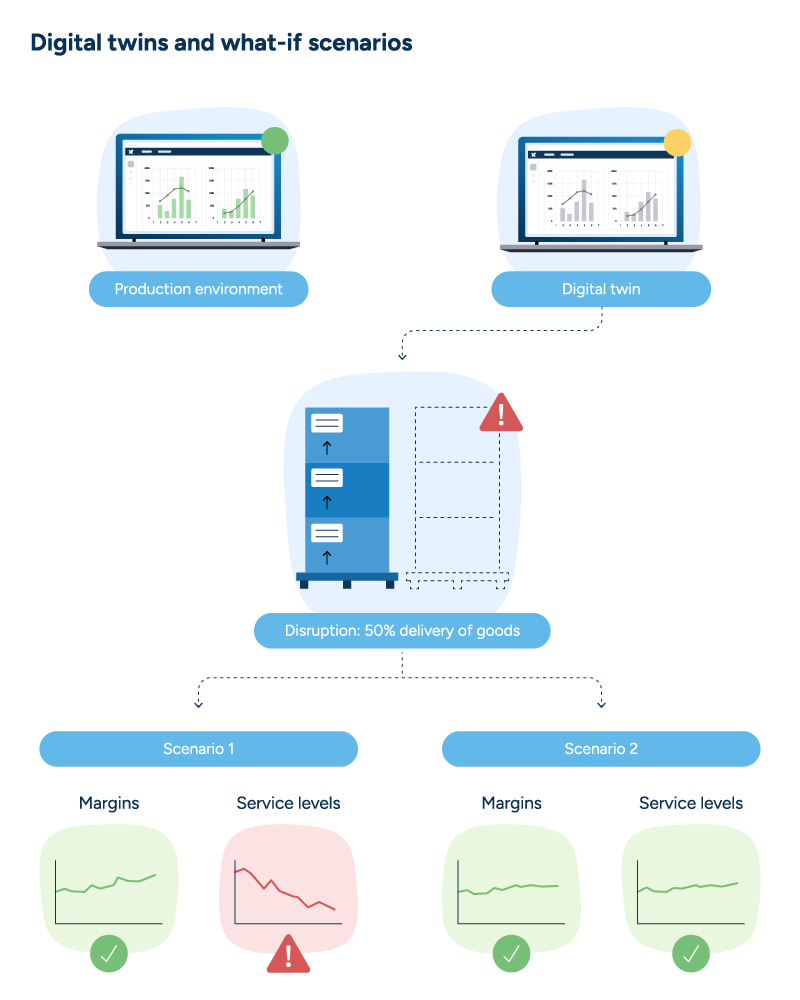
Optimization capabilities are also used in digital twins, replicas of production planning environments that help planners run “what-if” scenarios with real data. For instance, a planner could run a scenario to see what would happen if 50% of an expected supply shipment arrived late and determine how they could adjust production to compensate for these lead times. This accelerates response times and improves decisions when manufacturers must adapt to sudden market shifts.
READ MORE: Vita Coco streamlines operations with optimization and digital twins
2. Machine learning-based forecasts
Production planners depend on accurate forecasts to set proper inventory targets. Machine learning-based forecasts have become the gold standard for a reason. Machine learning (ML) algorithms can absorb and analyze massive amounts of forecast data and account for variability and volatility.
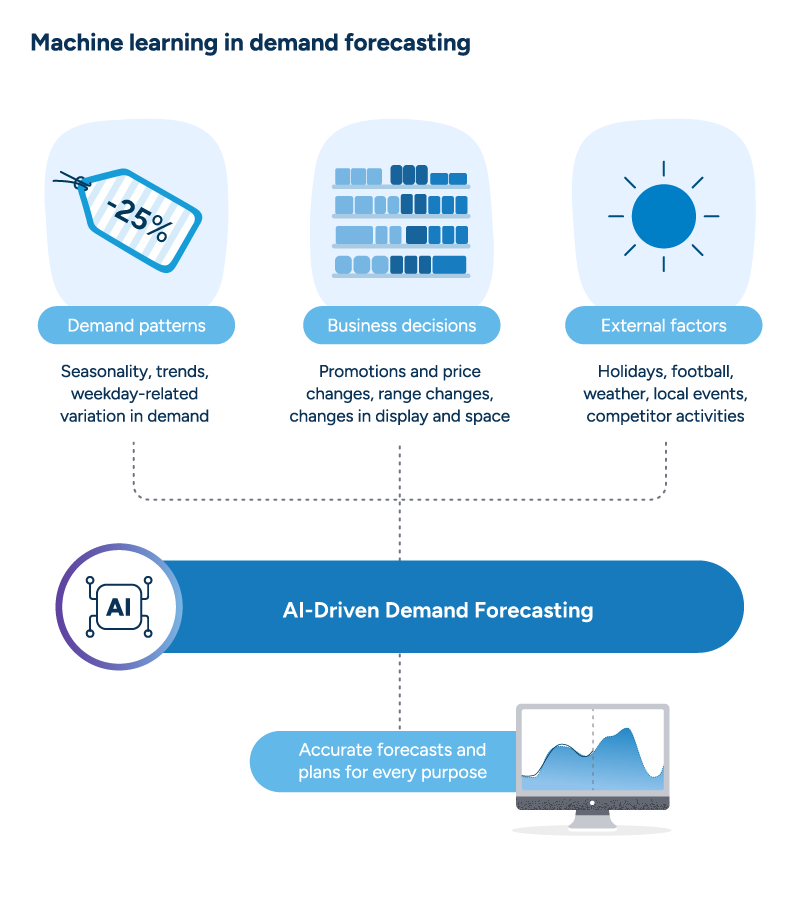
By factoring in demand patterns (like seasonality trends), internal business decisions (like promotions), and external events (like competitor activities), the algorithms eliminate planning drudgery and improve data insights for more accurate forecasts, creating a solid foundation for production plans. Machine learning can also use demand sensing signals such as retail POS data for sharper short-term forecasts.
Read more: Demand forecasting for retail and consumer goods
3. An automated solution on a unified platform
Since successful production plans depend on well-executed purchasing plans, manufacturers need to align purchasing and production processes. This combination, called master planning, should be interwoven with all the other planning functions.
A unified, automated solution vastly improves visibility and cross-functional collaboration.
- Automation saves planners from time-consuming grunt work and spreadsheets, providing them with ready-to-review plans so they can focus on more proactive strategy.
- Hosting these automated functions on a single platform simplifies data-sharing between teams.
- A unified solution helps create a centralized, AI-driven planning process that is still flexible enough to adapt to the needs of individual plants.
This kind of collaborative approach can head off potential problems. For instance, the solution could run a what-if scenario with a forecast – before that forecast gets finalized – and adjust the forecast or production plan as needed to ensure the two plans don’t conflict. Best of all, this can be an automated check that runs nightly.
Real-world results: Blendwell boosts service levels with integrated production planning
Blendwell Food Group produces and packs dried fruits and nuts for retailers across Europe. After a period of growth and increasing complexity, the company’s spreadsheet-based planning was not meeting requirements. The manufacturing process suffered from bottlenecks and grappled with long lead times and short shelf lives. Production and procurement planning relied solely on sales forecasts without factoring in current inventory levels, increasing the risk of overproduction. The forecast process took days and could only be completed monthly.
Teaming up with RELEX, Blendwell fully integrated its planning operations from forecasting to production, procurement, and inventory planning. The forecast allows for real-time adjustments that improve planning workflows. The automated solution provides insights into sourcing and production capacity, so Blendwell can manage demand fluctuations and supply chain volatility. Through optimization and “what-if” scenarios, the company can assess the potential impact of opportunities and risks. Plus, better supply chain visibility minimizes planning lag and allows teams to proactively identify issues before they escalate.
Blendwell has noticed significant waste reduction and achieved a 5-10% improvement in both forecasting accuracy and service levels.
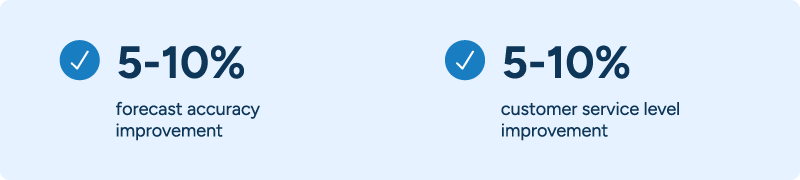
Creating a future-proof production planning process
Production planning does not have to be a perpetual headache. With the right strategies and best-in-class solutions, planners can feel confident in their decisions and less like they’re playing a game of blind man’s bluff.
By drawing on machine learning insights and the flexibility of optimization, manufacturers achieve competitive service levels and increase revenue while keeping inventory and production costs under control. These solutions help companies adapt to volatility and demand fluctuations for a thriving, profitable supply chain, even amid market upheaval.
Learn more about how manufacturers achieve rapid ROI from their technology investments by making production planning an integrated part of their supply chain planning process.