Mastering safety stock: Optimizing retail inventory levels with next-level planning software
Feb 13, 2025 • 10 min
Let’s face it: retailers often find themselves trapped in reactive safety stock management.
They’re not choosing this path. Resource constraints and technology limitations force them to rely on outdated single-point forecasts, basic historical data, and quick judgment calls.
Sure, these approaches worked fine a decade ago — but today? They crumble against supply chain volatility and lightning-fast shifts in consumer demand.
The costs add up fast. Weather disrupts seasonal patterns. Social media trends spike demand overnight. Without modern tools, retailers face a lose-lose decision: sink capital into excess inventory or watch sales walk out the door to competitors during stockouts.
Smart safety stock management demands more than traditional forecasting and manual adjustments. Companies must optimize their safety stock to achieve higher service levels and improved financial health — and they’ll need robust inventory planning software to do it. This strategic shift transforms inventory management from an operational liability to a competitive advantage.
What is safety stock?
Safety stock represents the extra inventory businesses maintain to protect against unexpected supply and demand fluctuations. Think of it as an operation’s insurance policy — it’s there to catch a business when surprises hit.
Take a national grocery chain managing fresh food across 800 stores. Historical data shows each store moves roughly 1,000 units of strawberries weekly, with supplier deliveries arriving every three days. But what happens when a heat wave drives unexpected demand for summer fruits? Or when weather delays impact their distribution network?
Without adequate safety stock across their network, the grocery store chain risks empty produce sections during peak shopping hours and disappointed customers taking their grocery lists to competitors.
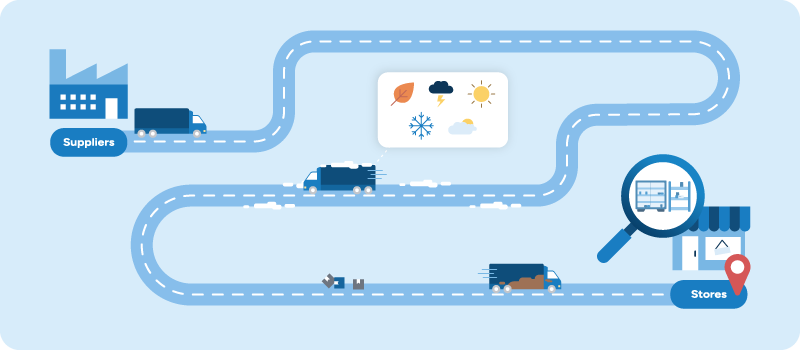
This scenario plays out across large-scale retail operations daily. Whether managing a retail store, a distribution center, or a wholesale operation, safety stock helps companies:
- Handle surprise demand spikes without breaking a sweat.
- Keep customers happy when suppliers hit unexpected delays.
- Maintain smooth operations even when the market throws curveballs.
Safety stock isn’t just about stockpiling inventory. It requires understanding unique business patterns, supplier reliability, and customer expectations. This undertaking involves analyzing sales data, understanding supply chain quirks, and planning for reasonable contingencies.
At the end of the day, it’s all about striking that perfect balance between holding enough inventory and keeping carrying costs in check.
Why is maintaining safety stock important?
Safety stock directly impacts a company’s bottom line through revenue protection and cost management. Major retailers lose millions annually from stockouts, while excess inventory ties up capital and warehouse space that could drive growth elsewhere. Competition in the market keeps growing over time, but getting safety stock right provides an operational win and competitive advantage to keep businesses on top.
There are many benefits to properly maintained safety stock:
- Revenue protection guards against lost sales during demand spikes or supply disruptions, keeping customers satisfied and revenue flowing.
- Operational stability prevents costly rush orders and emergency shipping fees when suppliers face delays.
- Market responsiveness lets companies capitalize on unexpected sales opportunities without scrambling to secure inventory.
- Brand protection maintains customer trust by consistently meeting their expectations for product availability.
But safety stock isn’t a “set it and forget it” solution. Poor management often leads to costly issues on both ends of the spectrum. Too little safety stock forces retailers into expensive emergency replenishment orders and risks permanent customer loss to competitors. Too much safety stock bloats carrying costs, consumes valuable warehouse space, and increases the risk of obsolescence — especially for seasonal or trendy items.
Getting safety stock right provides an operational win and competitive advantage to keep businesses on top.
The real challenge lies in finding the right balance for a specific operation. Leading retailers achieve this by combining sophisticated demand forecasting with a deep understanding of supply chain dynamics. They analyze historical data patterns, monitor supplier performance, and adjust safety stock levels dynamically across their network.
Should businesses calculate safety stocks manually?
Manual safety stock calculations might work for a corner store, but today’s complex business environment demands more sophisticated solutions.
Picture a company juggling hundreds or thousands of SKUs across multiple locations. Sure, teams could break out calculators and spreadsheets — but should they?
The real question isn’t whether companies can calculate safety stock manually but whether doing so makes strategic sense for their business.
Here’s the reality about manual calculations:
- They’re prone to human error. The more products a business manages, the more likely mistakes will creep in. One decimal point in the wrong place, and suddenly a company is holding twice the inventory needed — or worse: half of what customers demand.
- They devour time and resources. Team expertise is better spent on strategic decisions and customer relationships, not endless spreadsheet updates. Manual calculations force skilled professionals to spend hours on repetitive tasks instead of driving business growth.
- They can’t keep pace with market changes. Consumer demands shift rapidly, supply chains hit unexpected bumps, and seasonal patterns evolve. Manual calculations simply can’t adapt quickly enough to these real-world dynamics. A team might calculate perfect safety stock levels today, only to find them obsolete next week when a competitor launches a major promotion.
- They miss critical patterns. Basic formulas often overlook sophisticated factors like promotional impacts, emerging market trends, or changing customer behaviors. Without incorporating these insights, companies risk making inventory decisions based on incomplete information.
Small businesses operating in stable markets with limited SKUs might manage with manual calculations — for now. But as operations grow or markets become more volatile, the limitations of manual methods become increasingly apparent. These constraints create inefficiencies, drive up costs, and leave opportunities on the table.
As operations grow or markets become more volatile, the limitations of manual methods become increasingly apparent.
The question then becomes: Why should companies struggle with manual calculations when automated solutions can handle complex calculations more accurately, adapt to market changes in real time, and free teams to focus on strategic growth?
How to calculate safety stock levels
The right planning software can also help businesses stop looking to the past to solve problems in the future.
Most businesses still rely on historical data, looking backward to move forward. They analyze past sales patterns, calculate average demand, and set safety stock levels accordingly.
A basic, traditional safety stock formula often looks something like this:

If your store typically sells 100 units per day but sees sales spike occasionally to 150 units, and your supplier takes 5 days to deliver, you’d calculate:

The problem: past performance doesn’t guarantee future results. Yesterday’s patterns might not match tomorrow’s reality. What if that spike to 150 units happened during a promotion that won’t repeat? Or what if a business is entering its peak season when demand typically doubles?
Modern retail requires a more dynamic approach that integrates forecasting data to predict and prepare for future demand patterns. This means looking at not just averages but forecast variance — how much your actual sales typically differ from your forecasts. If your forecast is typically off by 20-30 units each day, that’s crucial information for setting safety stock levels.
This forward-looking approach considers factors like:
- Seasonal demand shifts before they happen
- Promotional impacts across your network
- Supply chain disruption risks
- Market trend predictions
- Supplier closures
- Product terminations
A basic forecast-integrated formula might look like:

This formula introduces an important statistical tool called a Z-score. A Z-score translates your desired service level into a number that works in calculations. These values come from statistical tables that map service levels to standard Z-scores:
- 90% service level = 1.28
- 95% service level = 1.645
- 97% service level = 1.88
- 99% service level = 2.326
Retailers don’t need to calculate these Z-scores themselves, as they’re standard statistical values used across industries. Instead, planners simply specify their desired service level, like 95% or 99%. Modern planning software translates these percentages into the right Z-scores automatically, eliminating the need for manual lookups or conversions.
This formula packs more punch than traditional methods because it combines two critical factors:
- Forecast variance (for measuring how much your actual sales typically deviate from predictions).
- Lead times (for how long it takes to get more inventory).
The mathematical combination of these factors gives retailers a safety stock number that’s more likely to match future needs.
Of course, the actual calculations used by modern planning software go far deeper, incorporating machine learning algorithms and real-time data analysis. These systems process thousands of variables simultaneously to optimize safety stock levels across your entire network.
4 ways to optimize safety stock with the next-level planning software
Much like paper ledgers and wall-mounted inventory boards before them, spreadsheets and manual calculations belong in the past. Modern businesses need modern solutions. Advanced planning software makes safety stock calculations easier while transforming them into a strategic advantage, with features like:
1. Smart, AI/ML-driven forecasting
Traditional forecasting feels like throwing darts blindfolded. Modern platforms reduce the randomness, analyzing everything from seasonal trends to customer buying patterns to create predictions that actually match reality. A truly comprehensive solution will keep learning and improving, catching subtle patterns human analysts might miss.
Modern platforms reduce randomness, analyzing everything from seasonal trends to customer buying patterns to create predictions that actually match reality.
These modern solutions rely on artificial intelligence (AI) to create smarter forecasts—specifically, machine learning (ML). ML algorithms dig deep into past performance data, uncovering hidden patterns and relationships. This goes beyond better predictions, enabling teams to understand why certain patterns emerge. The system grows smarter over time, continuously refining its predictions based on new data and outcomes.
READ MORE: The complete guide to machine learning in demand forecasting
2. Real-time supplier performance tracking
Supply chain surprises don’t need to hurt like they do. Modern software tracks supplier performance in real time, monitoring everything from delivery times to reliability patterns. Teams receive early warnings about potential delays, allowing them to adjust safety stock before problems occur. And platforms like RELEX account for lead time variability, allowing planners to account for less reliable suppliers.
3. Smart optimization
Gone are the days of choosing between stockouts and excess inventory. Advanced inventory optimization models juggle multiple variables simultaneously. For instance, a system like RELEX factors in:
- Holding costs
- Service levels
- Spoilage and expiration dates
- Lead times
- Demand patterns
- The unit in which a product must be ordered (such as batches or pallets)
The right solution can find the sweet spot where inventory costs stay low while service levels remain high. What makes this approach special? It adapts continuously as conditions change, maintaining optimal levels without constant manual adjustments.
4. Time-saving automation
The best systems go beyond calculation automation to amplify human expertise. Automation handles the number-crunching, freeing supply chain professionals to focus on strategic decisions. Teams spend less time wrestling with spreadsheets and more time driving business growth. This combination of artificial and human intelligence creates results that could not be achieved alone.
How ICA Sweden optimized safety stock with RELEX
Theory and features sound great on paper, but real-world results prove the true value of modern safety stock management. The transformation of ICA Sweden offers a perfect example of what’s possible with the right software.
Sweden’s leading grocer faced a complex challenge: managing inventory effectively across 1,300 independently operated stores. ICA Sweden’s manual systems couldn’t handle the complexity of coordinating safety stock levels across this vast network. Seasonal demand swings created particular headaches, with stores struggling to maintain appropriate stock levels during promotional periods and holiday peaks.
The result? Some stores carried excess inventory while others faced stockouts — a classic safety stock dilemma at scale.
RELEX transformed ICA Sweden’s safety stock management through a comprehensive approach. The implementation leveraged AI-driven forecasting to predict demand patterns store by store, automatically adjusting the amount of safety stock based on each location’s unique needs.
Dynamic safety stock calculations adapted to seasonal variations and promotional impacts in real time, particularly crucial for ICA Sweden’s extensive fresh produce selection. The system automatically adjusted inventory levels for seasonal items, ensuring optimal stock even during the peak summer demand. Combined with the system’s ability to process vast amounts of data, this intelligent handling of products eliminated the manual burden on store managers while dramatically improving forecast accuracy.
Not only has our collaboration produced tangible results, such as the 32% decrease in safety stock inventory, but working with RELEX has been easy and innovative.
Andreas Persson, Head of Replenishment, ICA Sweden
The results transformed ICA Sweden’s operations:
- Safety stock inventory dropped by 32%.
- Forecast accuracy jumped by 6.69 percentage points.
- Capital previously tied up in excess inventory became available for strategic investments.
These improvements translated into tangible business benefits. Lower inventory levels reduced carrying costs, while more accurate forecasting meant fewer stockouts and happier customers. The freed-up capital could now support growth initiatives instead of gathering dust on warehouse shelves.
Uncomplicate safety stock calculation with the right planning software
Recognizing the limitations of manual safety stock management marks only the first step. Companies must transform this awareness into action, moving beyond outdated tools that drain resources and limit growth potential.
Success demands a strategic approach. Rather than viewing safety stock as a mere operational concern, companies should evaluate their current methods against broader business goals. Modern solutions work best when they empower experienced teams to focus on strategic decisions while automation handles routine calculations and adjustments.
The evidence points clearly in one direction: yesterday’s tools can’t solve today’s challenges. Companies that embrace modern safety stock management now position themselves to navigate market complexity, reduce costs, minimize waste, and drive sustainable growth. Those that don’t risk falling behind competitors who have already made the shift.