Measuring the impact of any single decision or event further down the value chain is difficult — especially given the modern supply chain’s increasingly global and complex nature. For instance, a raw material shortage might lead to production and distribution delays and prompt retailers to source alternatives at a higher cost. It could even result in stockouts that disappoint would-be shoppers.
But the impact of such decisions also ripples back to the source. The higher costs of retail goods stemming from a raw material shortage can result in a surplus when consumers push back, triggering markdowns that alter purchasing behaviors and adversely impact the brand owners’ margins. This demand shift might force manufacturers and suppliers to adjust their production and sourcing strategies, perpetuating a vicious cycle of disruption.
Companies hoping to avoid this cycle — and its costly repercussions — need to make data-driven decisions and gain maximum visibility across every link in the chain. Despite the challenges involved, achieving optimized supply chain planning in the modern market is both possible and essential for continued success — and the right planning software should be the cornerstone of any company’s approach.
Key takeaways
- Supply chain planning (SCP) integrates material flows, capacity, and information with real-time data and analytics to optimize decisions, align strategic goals, and enhance efficiency across all supply chain functions.
- Optimized supply chain planning benefits include cost reduction, improved customer satisfaction, increased efficiency, enhanced decision-making, risk mitigation, and improved sustainability.
- End-to-end supply chain planning integrates all functions and sectors to ensure agility, minimize risks, and stay competitive in a a highly interconnected supply chain environment.
- The chief components of supply chain planning include demand planning, distribution planning, production planning and scheduling, and purchase planning, culminating in an integrated business planning (IBP) process.
- Effective management of planning layers and time horizons requires advanced software capable of synchronizing vertical and horizontal planning.
- A robust, AI-powered planning solution frees planners to do value-adding work instead of being trapped in a constant cycle of reaction and manual adjustment.
What is supply chain planning (SCP)?
Supply chain planning (SCP) is the coordination of material flows, capacity usage, and information to make optimal decisions and meet demand sustainably and profitably.
Manufacturers, consumer goods companies, wholesalers, and retailers all rely heavily on supply chain planning to integrate various functions, including procurement, manufacturing, and logistics. These companies employ real-time data, advanced analytics, and collaboration across different departments and stakeholders to ensure that products are available at the right place and time.
Effective supply chain planning aligns closely with broader planning objectives like sales and operations planning (S&OP) and integrated business planning (IBP). Supply chain planning connects near real-time data and analytics across departments to ensure strategic goals align with operational realities. This integration drives efficiency, enhances responsiveness to market changes, and supports long-term growth and profitability.
6 essential benefits of optimized supply chain planning
Supply chain planning is a mission-critical function for companies along the value chain. Whether or not a business can successfully optimize their planning can spell the difference between profitability and costly errors.
Companies that prioritize optimizing their supply chain planning processes reap benefits like:
- Cost reduction. Optimal planning minimizes excess stock and transportation expenses, reducing overall operational costs. This leads to significant savings and better allocation of financial resources.
- Improved customer satisfaction. Timely and accurate deliveries enhance product availability and customer loyalty. Happy customers are more likely to visit again and refer the business to others.
- Increased efficiency. Proper planning streamlines operations and optimizes resource utilization, boosting workforce productivity. Efficient processes reduce downtime and improve overall operational performance.
- Enhanced decision-making. Better strategic decisions result from real-time insights and scenario planning capabilities. Informed decisions help businesses quickly adapt to market changes and demands.
- Risk mitigation. Great planning processes improve supply chain resilience and balance inventory levels to handle demand variability. Proactive risk management prevents disruptions, maintains smooth operations, and helps reduce the bullwhip effect in supply chain planning.
- Sustainability. Better decisions result in reduced waste and efficient resource use. Sustainable practices enhance a company’s reputation and compliance with regulations.
Companies should strive to achieve these benefits to stay ahead in a market marred by constant disruption, evolving consumer preferences, and intense competition. Their supply chain must be as agile, efficient, and resilient as possible to navigate these challenges successfully.
Focusing on the benefits of optimized planning is more than just a profitability play — it’s a necessity that reinforces a company’s ability to compete and thrive.
Economic volatility, geopolitical tensions, and escalating customer expectations increasingly pressure supply chains. Focusing on the benefits of optimized planning is more than just a profitability play — it’s a necessity that reinforces a company’s ability to compete and thrive. Companies that fail to adapt risk falling behind and face higher costs, lost sales, and diminished market relevance.
The strategic importance of end-to-end supply chain planning
The “chain” in the phrase “supply chain” undersells just how complex it is. It’s more of a sprawling apparatus comprising countless, ceaselessly moving parts. (Of course, “sprawling supply apparatus” doesn’t quite have the same ring to it.)
Optimizing just a single gear in that machine does little to impact the performance of the machine. In the same way, streamlining just a single segment of the broader supply chain returns limited results.
A holistic strategy that integrates every function — from procurement and production on the supplier side to inventory management and replenishment on the retailer’s part — ensures companies can respond swiftly to changes, minimize risks, and maintain competitive advantage.
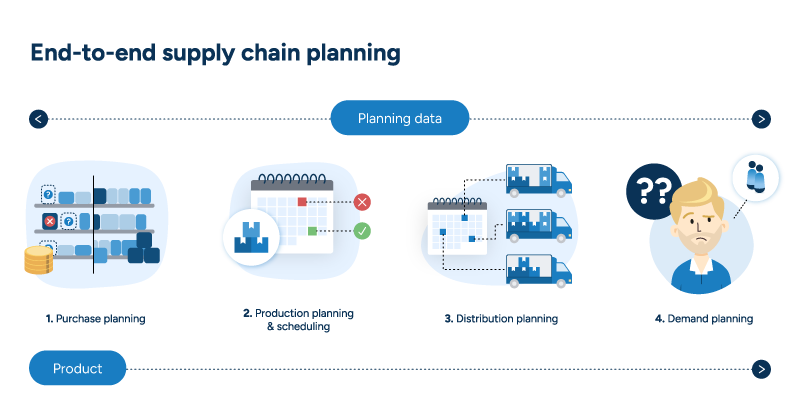
Each supply chain segment has unique challenges, but truly optimized supply chain planning demands visibility, collaboration, and planning across all these areas and industries. This interconnected approach enables seamless coordination, reduces costs, and ensures that products flow efficiently from suppliers to consumers to maximize overall supply chain performance.
SCP in consumer goods and manufacturing
Supply chain planning in the consumer goods and manufacturing industries involves synchronizing supply and demand, managing production schedules, and optimizing resource use. This process requires accurate demand forecasting, inventory management, and production planning to maintain ideal inventory levels, minimize waste, and ensure product availability.
Managing these various responsibilities simultaneously is a monumental task, but planning is further complicated by:
- Fluctuating customer demand. Rapid changes in consumer preferences and seasonal variations make it difficult to predict demand accurately, especially in the fast-moving consumer goods (FMCG) supply chain.
- Complex production requirements. Sequencing production orders to reduce changeover times and comply with regulations, such as allergen control in the food manufacturing supply chain, adds operational complexity.
- Perishability of materials. Managing the shelf life of raw ingredients and finished goods requires careful planning to avoid spoilage and loss.
- Supply chain disruptions. Unexpected events and supply volatility demand quick replanning capabilities to maintain service levels and avoid stockouts.
CPG and manufacturing companies play a crucial role in broader supply chain efforts. Their ability to adapt quickly to disruptions and shifts in demand directly impacts the stability and efficiency of the end-to-end supply chain. Advanced tools and real-time data integration are vital for these companies to create precise forecasts, adjust production plans swiftly, and coordinate effectively with suppliers and distributors.
SCP in wholesale
Wholesale supply chain planning centers around managing large volumes of diverse products and ensuring timely deliveries to various customers, such as retailers and businesses. Effective planning requires accurate demand forecasting, inventory management, and transportation optimization to minimize spoilage, waste, and costs.
Of course, wholesalers face unique planning challenges of their own, including:
- Managing diverse product lines. Handling a wide variety of goods, from non-perishable items to fresh and perishable products, demands precise forecasting and tailored inventory strategies.
- Integrating data from multiple sales channels. Consolidating information from online, in-store, and direct sales to adapt supply chain strategies to customer needs is complex but essential.
- Balancing inventory levels. Maintaining the right stock to avoid overstocking or stockouts while responding to promotions, demand spikes, and supplier variability.
Wholesalers link suppliers and manufacturers to retailers and other businesses, ensuring a steady flow of goods. Their ability to anticipate demand shifts, optimize stock levels, and coordinate with various partners directly impacts the overall supply chain’s responsiveness and efficiency. Advanced analytics and real-time visibility tools are essential for wholesalers to improve decision-making, enhance operational efficiency, and maintain high customer satisfaction across multiple channels.
SCP in retail
Retail supply chain planning ensures product availability on shelves to meet consumer needs and drive customer satisfaction and loyalty. Retailers must effectively manage promotions and seasonal demand fluctuations while coordinating with multiple suppliers to optimize inventory levels and streamline replenishment.
But supply chain planning gets complicated fast for retailers, who often struggle with:
- Managing complex promotions. Retailers must balance inventory to support promotional activities and avoid over- or under-stocking products.
- Responding to seasonal demand. Companies need to adjust supply and inventory levels to accommodate rapid changes in consumer demand during peak seasons.
- Coordinating with diverse suppliers. Teams must maintain seamless operations while sourcing from multiple suppliers with varying lead times and reliability.
- Maintaining real-time visibility. Businesses need accurate, up-to-date inventory data to react quickly to market changes and customer needs.
- Addressing labor turnover and shortages. Retailers navigate challenges in workforce stability, affecting all areas of their operations.
Retailers serve a vital function in the end-to-end supply chain, driving demand and setting expectations for suppliers and distributors. Their ability to forecast demand accurately, optimize replenishment, and collaborate with suppliers directly impacts the entire supply chain’s agility and efficiency. Accurate demand forecasting, real-time data integration, and replenishment optimization are essential to reducing costs, improving decision-making, and ensuring a seamless shopping experience for consumers with evolving preferences.
The fundamental components of supply chain planning
Every sector contributes to supply chain planning, but many responsibilities fall to manufacturers and consumer goods companies. These entities manage the production, procurement, and distribution planning of goods. Most tasks are concentrated on the supply side, so these companies most intensely feel the impact of continuous adjustments — particularly as they strive to align shifting demand with supply realities.
Demand planning
Demand planning involves forecasting customer demand to ensure the right products are available at the right time. This process includes analyzing market trends, historical sales data, and other factors to forecast future demand. Demand planning is essential for aligning production and inventory levels with customer needs, reducing the risk of stockouts and overstock situations.
Effective demand planning helps businesses respond quickly to market changes and maintain high service levels. Demand planners must continuously adjust their forecasts to account for promotions, seasonal variations, and other factors impacting demand. Savvy planners can also leverage demand sensing and demand shaping to detect and influence changes in customer behavior and market conditions using sufficiently advanced planning tools.
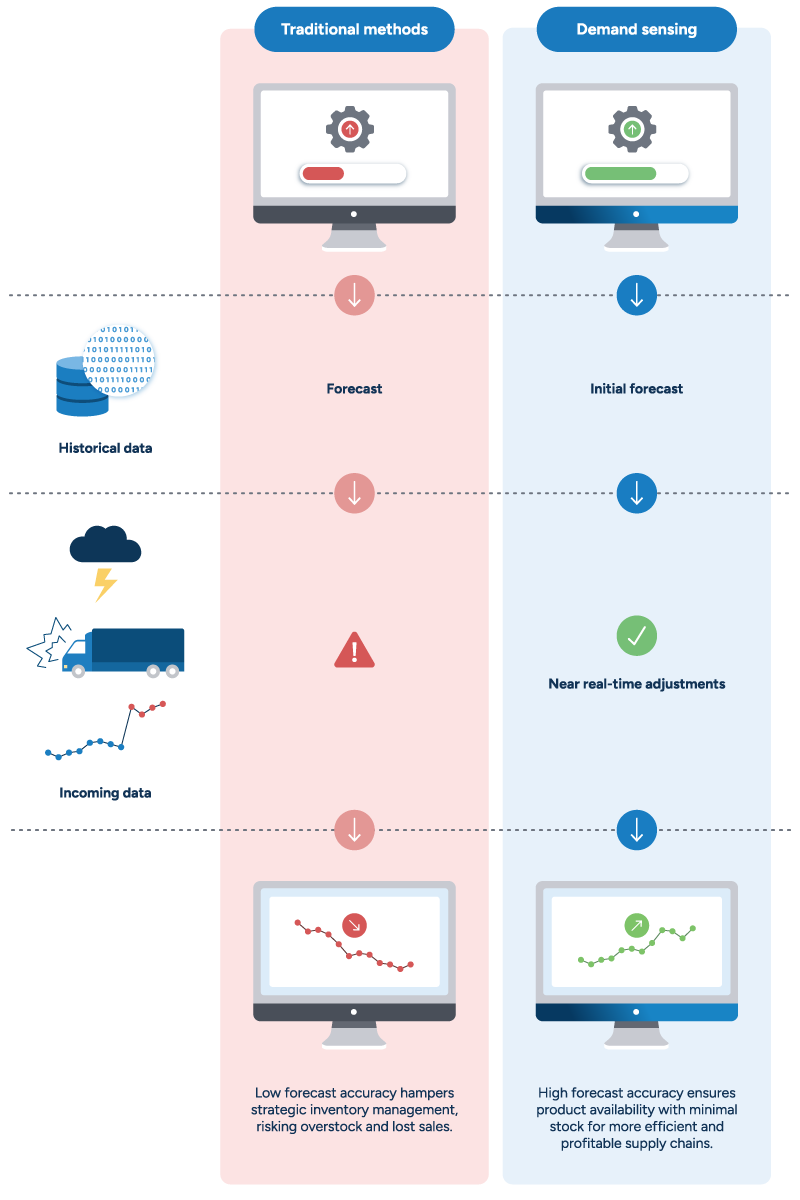
Distribution planning
Distribution planning is essential in supply chain management, ensuring the effective movement of goods from production facilities to end customers. The process involves:
- Selecting optimal transportation routes.
- Managing warehouse operations efficiently.
- Coordinating with various logistics providers to handle the movement of goods.
Distribution planning orchestrates the logistics of getting products to the right place at the right time and as efficiently as possible.
The goal is to deliver products on time and at the lowest possible cost while also adapting to changes in demand and dealing with potential disruptions. In a nutshell: distribution planning orchestrates the logistics of getting products to the right place at the right time and as efficiently as possible.
Effective distribution planning results from a collaborative effort among key stakeholders, each focusing on optimizing different aspects of the supply chain.
- Supply chain managers oversee the strategy.
- Transportation managers optimize routes.
- Warehouse managers streamline operations.
- Logistics coordinators manage day-to-day interactions.
- Inventory managers balance stock levels.
The seamless integration of these various functions is crucial in the broader context of supply chain planning, Advanced distribution planning software enhances this relationship using automated replenishment to ensure product availability and capacity planning to adjust for seasonal demand and promotions. This comprehensive system efficiently meets customer demands, supports sustainable growth, and maximizes supply chain effectiveness.
Production planning and scheduling
Production planning and scheduling are two distinct but closely connected supply chain planning functions. Production planning involves determining what products to produce, in what quantities, and by when, based on demand forecasts and resource availability.
Then there’s production scheduling, which involves creating a detailed timetable for the production process and specifying the exact times and sequences for manufacturing tasks to ensure efficient resource use and timely completion.
Both production planning and scheduling are essential for optimizing production capacity.
Effective production planning and scheduling help businesses maintain high production efficiency and product quality, but managing the process is extraordinarily difficult. It requires dealing with capacity variations, supplier collaboration, and ensuring that schedules align with demand forecasts. Production planners must also quickly adjust schedules in response to disruptions like equipment failures and supply shortages.
Purchase planning
Purchase planning focuses on the timely procurement of necessary components and raw materials for production. This process involves forecasting material requirements based on production schedules, negotiating with suppliers to ensure favorable terms, and managing inventory levels to avoid excess costs.
The role of purchase planning most often falls to the procurement team, who focus on:
- Strategic supplier engagement to build strong, reliable relationships with suppliers to manage supply variations and disruption risks efficiently.
- Using sophisticated tools to accurately forecast material needs and adjust orders swiftly, ensuring materials are available when needed.
- Balancing cost and inventory to strategically manage inventory to maintain necessary stock levels while minimizing holding costs.
- Collaborative decision-making to coordinate closely with production managers and suppliers to align purchasing decisions with production demands and market conditions.
Effective purchase planning ensures material availability, contributing to the business’ overall sustainability and profitability. Integrating advanced purchase planning software and strengthening supplier relationships allows companies to optimize procurement processes and adapt quickly to production and market changes.
Horizontal and vertical planning with advanced planning and scheduling (APS) software
Harkening back to the “sprawling supply apparatus” metaphor: supply chain planning is more than a single sequence of gears lined up in a perfect row. Gears fit into each other in multiple levels, and turning a gear in one level spins another three levels higher. Each gear is a different size than the next, with every cog faster or slower than the ones above or below.
Likewise, the various functions of supply chain planning — from demand planning to purchase planning — don’t operate in perfect sequence. They exist simultaneously and overlap constantly, creating multi-dimensional planning challenges. Companies must vertically plan to align multiple teams around a single strategic decision or risk unintended consequences. But planning also requires horizontal planning to consider each team’s unique schedules and project timelines.
Proper optimization of the planning process requires alignment across the multiple planning layers and time horizons — and doing so strategically requires advanced planning and scheduling software (APS) to keep everything on track.
Horizontal planning
Horizontal planning involves managing supply chain activities across different time horizons, from immediate operational decisions to long-term strategic planning. Short-term planning focuses on day-to-day operations such as inventory management and order fulfillment, while long-term planning addresses broader objectives like capacity expansion and market development. The challenge is ensuring that short-term actions align with and support long-term goals, as misalignments can have significant long-term consequences.
Organizations addressing the challenges of horizontal planning require robust planning software that supports multi-horizon planning and provides visibility across all timeframes. Such software:
- Allows for efficient management of daily operations
- Helps in planning for future capacity and market changes
- Ensures the ability to adapt plans in response to changing conditions
This approach coordinates efforts across various planning horizons and enhances the supply chain’s overall strategic flexibility.
Vertical planning
Vertical planning involves coordinating different organizational teams and functions, such as procurement, production, logistics, and sales. Each team has its own objectives and responsibilities, but their activities must align to ensure a cohesive and efficient supply chain.
The difficulty lies in synchronizing these diverse functions, as misalignment can lead to inefficiencies, increased costs, and missed opportunities. This synchronization is all the more challenging considering teams plan continuously on various time horizons and granularities, including operational, tactical, and strategic planning.
Each team has its own objectives and responsibilities, but their activities must align to ensure a cohesive and efficient supply chain.
Overcoming the challenges of vertical planning requires robust communication and collaboration tools that enable real-time data sharing and decision-making. Planning software can integrate data from various functions, providing a unified view of the supply chain. This integration allows teams to coordinate their activities more effectively to ensure that:
- Procurement aligns with production schedules
- Logistics plans support sales forecasts
- All functions work towards common goals
Advanced planning and scheduling software offers scenario planning and optimization capabilities, helping organizations anticipate and mitigate potential disruptions.
Striking a balance between vertical and horizontal planning
Balancing vertical and horizontal planning ensures that high-level decisions complement operational constraints and that daily tasks support overarching goals. But companies often struggle to strike this balance due to the complexity and interdependencies involved. Misalignments between strategic decisions and operational realities lead to inefficiencies, increased costs, and missed opportunities.
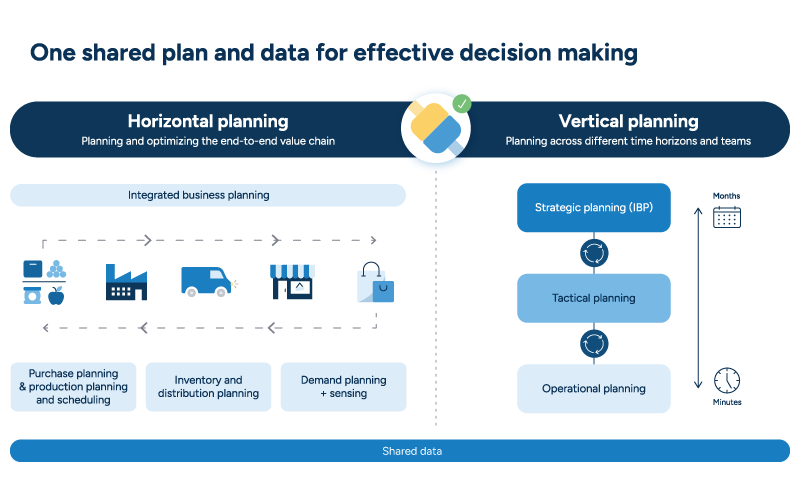
An advanced planning and scheduling solution is essential in overcoming these issues. Such software integrates vertical and horizontal planning data, providing a comprehensive view of the supply chain.
Companies can use APS software to strike a balance between vertical and horizontal planning with:
- Integrated planning systems. A solution that merges data from vertical and horizontal planning offers a comprehensive view of the supply chain, aligning strategic goals with operational capabilities.
- Cross-functional collaboration. An APS solution fosters communication across various teams and planning timelines, synchronizing vertical and horizontal plans with tools like regular cross-functional meetings and shared platforms for data exchange.
- Scenario analysis and flexibility. Advanced planning and scheduling software enables organizations to use scenario planning tools to explore different strategies and make decisions that consider immediate needs and future consequences.
Successfully implementing these strategies enhances operational efficiency and ensures the supply chain remains resilient and adaptable to changes. This approach reduces costs and aligns closely with business objectives, creating a robust framework for sustained growth and competitive advantage.
True vertical and horizontal planning alignment requires integrating sales and operations planning (S&OP) and integrated business planning (IBP). These frameworks ensure that strategic goals harmonize with daily operations across all supply chain functions. Companies can embed S&OP and IBP into their strategic and operational processes to synchronize planning, minimize costly misalignments, and promote a unified, effective planning environment.
6 strategies for optimizing supply chain planning with advanced software
Even the biggest, brightest, and hardest-working planning team could not manage the seemingly endless work required to optimize their organization’s supply chain — at least, not without the essential help of a state-of-the-art planning solution.
A robust artificial intelligence (AI)-powered supply chain planning solution arms teams with a slew of tools to synchronize every corner of their supply chain. Teams can gain end-to-end visibility, make data-informed decisions, and gauge the impact of their actions within a single unified platform. Data-guided insights and automation ensure personnel can spend more time on value-adding strategic planning and less time in a loop of constant, manual adjustments.
An advanced planning solution helps with executing those planning strategies, using cutting-edge features that empower teams to:
1. Deploy AI to enhance forecasting and supply chain optimization
AI is the cornerstone of modern supply chain planning. Solutions that use AI to improve everything from forecasting accuracy to inventory optimization will change the game for those who adapt. Algorithms analyze large datasets to identify trends and enable predictive analytics, helping companies anticipate market changes and consumer demands with precision. Businesses increasingly rely on AI innovations as they transition from reactive to proactive planning, adapting to market conditions before they impact the bottom line.
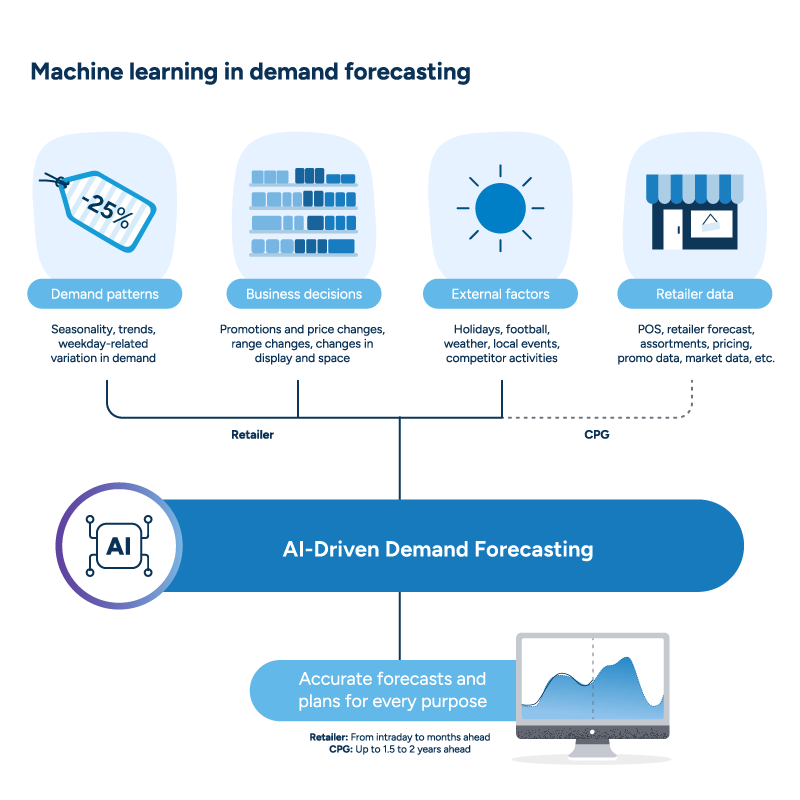
The strategic use of AI in supply chain planning hinges on its ability to process and learn quickly from vast amounts of data. Machine learning models allow teams to continually refine their forecasts and strategies based on new data and outcomes. This dynamic learning process improves prediction accuracy and enhances the overall agility and resilience of the supply chain.
2. Integrate data for smarter decision-making
A company can generate reliable, actionable insights when they trust the quality and consistency of the data used in their decision-making. Advanced planning software integrates and analyzes data from diverse sources, enabling organizations to make informed, data-driven decisions. This integration facilitates a holistic view of the supply chain, allowing for more accurate predictions and strategic planning.
A company can only generate reliable, actionable insights if they trust the quality and consistency of the data used in their decision-making.
Consolidating data from suppliers, customers, and internal operations under a single platform enables organizations to apply advanced analytics to uncover hidden inefficiencies and opportunities. This integration empowers companies to optimize processes based on robust data insights, not assumptions.
3. Enhance supply chain collaboration with real-time collaboration tools
Integrated platforms also encourage real-time data sharing — a critical component of supply chain collaboration. These solutions provide simultaneous access to the same data for internal stakeholders and collaborators at trading partners. This real-time collaboration aligns operations with fast-changing market conditions and builds partnerships responsive to supply chain dynamics.
This strategy relies heavily on the planning software’s capability to support seamless communication and data exchange among all parties involved. Ensuring every trading partner has access to up-to-date information allows them to plan together and make collective, effective decisions for enhanced supply chain reliability.
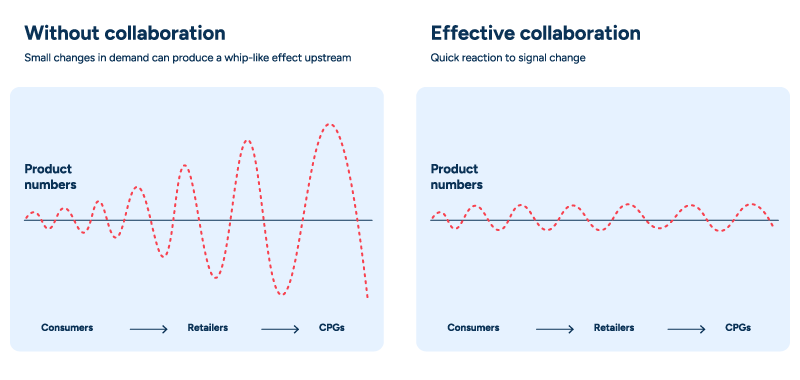
4. Optimize inventory with smart algorithms
Companies require effective inventory management to meet customer expectations and maintain financial health. An advanced solution implements algorithms to create dynamic inventory models that reflect real-time market conditions. These algorithms help businesses maintain optimal inventory levels, ensuring product availability while minimizing the costs associated with over- or understocking.
Inventory optimization algorithms analyze historical sales data, current market trends, and predictive insights to recommend the best inventory strategies. These strategies help businesses respond swiftly to demand shifts without compromising service quality or operational costs. Companies that maintain the right inventory balance can more easily avoid the pitfalls of excess stock and more effectively capitalize on market opportunities.
5. Embrace digital twin technology to enhance planning
Advanced planning software supports digital twin technology, allowing companies to create virtual models of their supply chains. Digital twins serve as a sandbox for testing ideas, providing a safe environment to foresee the results of decisions like:
- Simulating and improving manufacturing processes to enhance efficiency and reduce downtime.
- Monitoring equipment health to predict failures and schedule timely maintenance.
- Virtually testing and refining product designs before physical prototyping.
Digital twin technology offers a detailed and accurate simulation of the supply chain, allowing companies to anticipate the results of changes before implementing them. This strategic testing and planning ensures that each decision is data-backed, likely to succeed, and capable of withstanding various challenges.
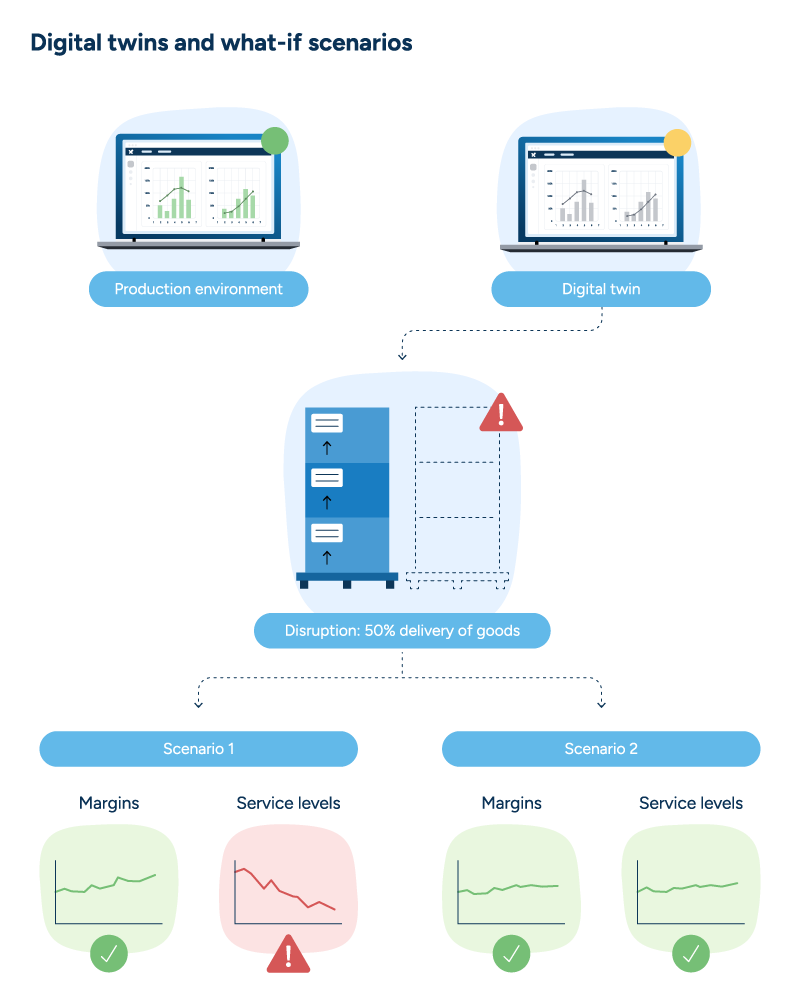
6. Implement risk management with scenario planning tools
Scenario planning tools focus on simulating specific risk scenarios and strategizing appropriate responses using advanced modeling capabilities. These tools allow businesses to input different variables and conditions to simulate potential risks and evaluate their impacts.
Scenario planning tools allow companies to quantify the impact of disruptions and test mitigation tactics.
Companies use scenario planning tools to simulate various risk scenarios, like supply shortages and logistical delays. Teams evaluate the response effectiveness of multiple strategies in a controlled environment, allowing companies to quantify the impact of disruptions and test mitigation tactics. They can then develop tailored contingency plans that ensure operational continuity, optimize response times, and minimize unforeseen financial and operational impacts.
Real-world examples of supply chain planning success
Choosing the right supply chain planning solution is critical for future success, but taking implementation from a vague idea to an actual reality can feel daunting. And without the right solution provider, implementation can certainly be a roller coaster.
But it doesn’t have to be. Many companies have implemented new supply chain planning solutions and used them to great success, realizing remarkable results by taking advantage of next-generation capabilities — including those achieved by these RELEX customers.
Finsbury’s tailored supply chain planning solution
Leading UK bakery Finsbury Food Group struggled with supply chain complexities due to limited visibility into sales data and inventory levels. This lack of transparency led to frequent overstocking and stockouts across their diverse range of bakery products. With operations spread across multiple sites and a complex product mix — including items with short shelf lives — Finsbury needed an integrated solution to optimize their supply chain planning and enhance operational efficiency.
The RELEX consultants worked closely with our experts and took the time to understand our business. This meant they could design a solution that was right for Finsbury.
Liam McVey, Group Demand Planning Manager
RELEX Solutions provided a customized supply chain planning solution that used advanced forecasting and replenishment tools. Finsbury consolidated sales and inventory data into one platform to gain real-time visibility and improve forecasting accuracy. This led to a 25% reduction in stockouts, a 20% decrease in inventory holding, and a 10% improvement in waste reduction. The impact of RELEX in optimizing Finsbury’s supply chain enabled the company to make more informed decisions and enhanced overall supply chain agility.
Rastelli’s improved demand forecasting and replenishment
Premium meats and seafood supplier Rastelli Foods Group faced significant supply chain challenges as they expanded their operations. Inefficient inventory management and unpredictable demand patterns across various sales channels resulted in overstocking and understocking issues, disrupting their supply chain flow. Their diverse customer base spanned retail and food service, so Rastelli needed a sophisticated, unified supply chain planning approach to ensure sustained growth and service excellence.
RELEX Solutions delivered an advanced supply chain planning system tailored to Rastelli’s specific needs. The solution used precise demand forecasting and replenishment tools for better inventory control and more accurate demand responsiveness. This led to a 30% reduction in inventory levels, lowering carrying costs without compromising service quality.
Specialty Bolt and Screw advanced planning solution
Specialty Bolt & Screw, a leading global distributor of fasteners and supply chain solutions, faced significant supply chain challenges due to rapid growth and an expanding product portfolio. The company struggled with inefficient inventory management and forecasting, resulting in excess stock, high inventory carrying costs, and delayed order fulfillment. The lack of a cohesive approach to supply chain planning hindered their ability to meet customer demand effectively while maintaining optimal inventory levels.
The ability to dynamically adjust our inventory and forecasting in real-time has set a new standard for operational excellence within our organization.
Matt Larsson, VP of Supply Chain Operations
RELEX Solutions implemented a powerful, data-driven supply chain planning solution that leveraged machine learning to enhance demand forecasting and inventory optimization. By integrating data across all operations, Specialty Bolt & Screw achieved a 20% reduction in inventory levels, improved order fulfillment rates, and reduced lead times.
Plan for success with optimized RELEX supply chain planning
The current state of supply chain planning faces several significant challenges. Planning relies heavily on assumptions due to a lack of real-time data and advanced analytics. Outdated systems and fragmented data sources lead to a costly latency in decision-making, and a lack of visibility prevents businesses from understanding potential outcomes. And many organizations fail to analyze past plans and impact once decisions are made, leading to repeated mistakes and missed improvement opportunities.
There is a brighter future for planning just ahead, and software plays a crucial role in bridging the gap.
- Future planning is AI-powered, with companies relying on data-driven insights to reduce assumptions and automation to minimize repetitive, labor-intensive tasks.
- Future planning is highly collaborative, with stakeholders working from the same data at the same time on the same platform.
- Future planning is also adaptive, with comprehensive visibility into the entire supply chain affording companies the privilege of proactive planning and enhanced responsiveness.
Investing in the right supply chain planning and optimization solution is investing in future supply chain resilience. Of course, talking about adopting a new solution and actually implementing one are two very different realities. The interconnected nature of supply chain operations means that any failure can have widespread and costly repercussions. Even simply changes can confuse users, let alone a comprehensive overhaul.
RELEX has a proven track record and decades of expertise in helping companies navigate the complexities of supply chain planning implementation.
When navigating the sprawling supply apparatus — er, supply chain — having an experienced guide like RELEX can make all the difference. RELEX has a proven track record and decades of experience helping companies navigate supply chain planning implementation. Our highly configurable platform seamlessly connects with existing systems, including ERP platforms, and minimizes the need for costly customizations. Our thoughtful approach — starting small but scaling quickly and strategically — ensures that companies can adapt without overwhelming their operations.
With a 100% implementation success rate and a philosophy of treating customers as friends, RELEX ensures that every gear in your supply chain machine aligns perfectly, turning pain points into potential opportunities for sustainable growth.
Supply chain planning FAQ
What is the supply chain planning cycle?
The supply chain planning cycle involves several key stages:
- Demand planning
- Distribution planning
- Production planning and scheduling
- Purchase planning
It starts with forecasting demand, followed by aligning supply capabilities, scheduling production, and optimizing distribution to ensure products reach customers efficiently. This cycle is iterative and requires continuous monitoring and adjustments to respond to demand shifts and supply disruptions.
How is supply chain planning related to S&OP and IBP?
Supply chain planning is a core component of both sales & operations planning (S&OP) and integrated business planning (IBP). S&OP focuses on aligning demand and supply over a tactical horizon, ensuring that operational plans meet business goals. IBP extends this by integrating financial planning and strategic objectives, providing the organization with a unified approach to long-term planning and decision-making.
What does a supply chain planner do?
A supply chain planner forecasts demand, manages inventory levels, and coordinates supply chain activities to ensure timely product availability. They analyze data to predict future needs, create supply plans, and work with various stakeholders to balance supply and demand. They aim to optimize efficiency, reduce costs, and improve customer satisfaction.